Spherical copper coating tungsten composite powder, preparation method and application thereof
A composite powder and copper-coated technology, which is applied in the field of preparation of copper-tungsten composite powder and spherical copper-coated tungsten composite powder, can solve problems such as difficult large-scale production, complicated process, and cumbersome steps.
- Summary
- Abstract
- Description
- Claims
- Application Information
AI Technical Summary
Problems solved by technology
Method used
Image
Examples
Embodiment 1
[0095] Example 1: Intermittent electroplating of copper-coated tungsten composite powder with pyrophosphate bath
[0096] (1) Common tungsten powder with an average particle size of 5-20 μm (such as figure 1 As shown) is spheroidized by radio frequency plasma spheroidization device, the main process parameters are: central gas (argon) flow rate 20-30L / min, side gas (argon gas) flow rate 90-120L / min, carrier gas (argon gas) The flow rate is 3.5L / min, the feeding rate is 5-10g / min, the reaction chamber pressure is 60-80KPa, and the operating power is 60-70KW. (2) the tungsten powder (such as figure 2 and image 3 shown) into the pyrophosphate copper plating solution, wherein the plating solution includes: copper pyrophosphate 60g / L, potassium pyrophosphate 320g / L, triammonium citrate 15g / L, potassium sodium tartrate 20g / L, ammonia water 3ml / L. Use citric acid and potassium hydroxide to adjust the pH value of the pyrophosphate copper plating solution to 8.3 to 8.5, and adju...
Embodiment 2
[0097] Example 2: Intermittent electroplating of copper-coated tungsten composite powder with pyrophosphate bath
[0098] (1) Ordinary tungsten powder with an average particle size of 1-10 μm is spheroidized by a radio frequency plasma spheroidization device. The main process parameters are: central gas (argon) flow rate 25-35L / min, edge gas (argon) The flow rate is 120-140L / min, the carrier gas (argon) flow rate is 4.5L / min, the feeding rate is 10-25g / min, the reaction chamber pressure is 90-100KPa, and the operating power is 40-60KW. (2) Join the tungsten powder processed through spheroidization in step (1) in the pyrophosphate copper plating bath, wherein the plating bath includes: copper pyrophosphate 60g / L, potassium pyrophosphate 320g / L, ammonium citrate 25g / L, ammonia water 3ml / L. Potassium hydroxide is used to adjust the pH value of the pyrophosphate copper plating solution to 8.5 to 8.8, and the temperature of the pyrophosphate copper plating solution is adjusted to...
Embodiment 3
[0099] Example 3: Intermittent electroplating of copper-coated tungsten composite powder with pyrophosphate bath
[0100] (1) Ordinary tungsten powder with an average particle size of 5-15 μm is spheroidized by a radio frequency plasma spheroidization device. The main process parameters are: central gas (argon) flow rate 20-30L / min, edge gas (argon) The flow rate is 90-120L / min, the carrier gas (argon) flow rate is 5L / min, the feeding rate is 5-10g / min, the reaction chamber pressure is 50-70KPa, and the operating power is 30-60KW. (2) Add the tungsten powder treated by spheroidization in the step (1) to the pyrophosphate copper plating bath, wherein the plating bath includes: copper pyrophosphate 60g / L, potassium pyrophosphate 320g / L, ammonium citrate 15g / L, potassium sodium tartrate 20g / L, ammonia water 2ml / L. Use citric acid and potassium hydroxide to adjust the pH value of the pyrophosphate copper plating solution to 8.0 to 8.4, and adjust the temperature of the pyrophosp...
PUM
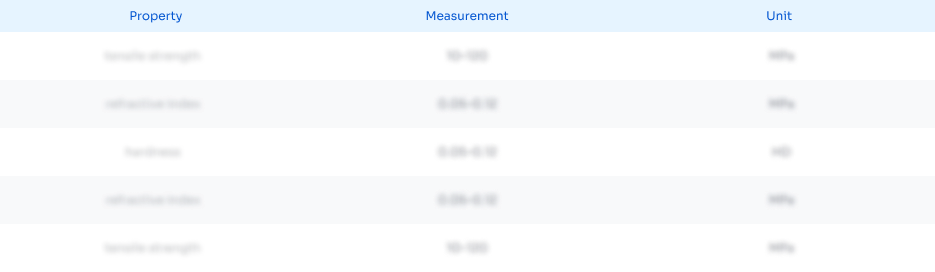
Abstract
Description
Claims
Application Information

- Generate Ideas
- Intellectual Property
- Life Sciences
- Materials
- Tech Scout
- Unparalleled Data Quality
- Higher Quality Content
- 60% Fewer Hallucinations
Browse by: Latest US Patents, China's latest patents, Technical Efficacy Thesaurus, Application Domain, Technology Topic, Popular Technical Reports.
© 2025 PatSnap. All rights reserved.Legal|Privacy policy|Modern Slavery Act Transparency Statement|Sitemap|About US| Contact US: help@patsnap.com