A kind of al-mg-er-zr heat-resistant aluminum alloy and its preparation process
An al-mg-er-zr and preparation process technology, applied in the field of metal alloys, can solve the problems of insignificant alloy microalloying effect, high annealing temperature, unfavorable strengthening, etc., so as to suppress the recrystallization process and increase the recrystallization temperature. Effect
- Summary
- Abstract
- Description
- Claims
- Application Information
AI Technical Summary
Problems solved by technology
Method used
Image
Examples
example 1
[0020] Example 1: An alloy ingot was prepared by smelting in a graphite crucible and casting in an iron mold, and the raw materials used were pure aluminum, pure magnesium, and master alloys of Al-6Er and Al-4Zr. At a melting temperature of 770±10°C, first melt the aluminum ingot, then add Al-Er and Al-Zr master alloys, add pure magnesium after the master alloy is melted, and add hexachloroethane to degas after the pure magnesium is melted. Stir, keep warm and stand for 10 minutes to make the components of each element in the melt evenly distributed before iron mold casting. Four Al-Mg-Er-Zr alloys with different compositions were prepared, and their actual compositions were measured by XRF, as shown in Table 1 below.
[0021] Table 1 Experimental alloy composition
[0022]
example 2
[0023] Example 2: The alloy in Example 1 is subjected to isochronous annealing treatment at 150-550° C., and the same is taken every 25° C. figure 1 The Vickers hardness of the alloys at different temperatures is given. It can be seen from the figure that the hardness of alloys A1, A2, and A3 all reach the peak at about 475 ° C, while the hardness value of Al-Mg alloy A4 is in the whole isochronous annealing process. basically unchanged. This shows that adding Er and Zr composite microalloying alloy has a very significant strengthening effect in the annealing process. In addition, it can be seen that as the magnesium content increases, the hardness value of the as-cast alloy also increases sequentially, and the increase in the hardness value during the annealing process increases accordingly with the increase of the magnesium content. For example, the peak hardness of the A1 alloy is higher than that of the as-cast alloy The alloy is 10Hv higher, the peak hardness of the A2 a...
example 3
[0024] Example 3: The alloy in Example 1 was subjected to isochronous annealing treatment at 150-475° C., then cold rolled on a rolling mill with a total deformation of 80%, and then recrystallization annealing treatment was performed on the cold rolled alloy. Such as figure 2 The recrystallization annealing hardness change curve of the alloy is given, image 3 The metallographic photographs of the alloy after recrystallization annealing are given. From image 3 In (a), it can be seen that the A1 alloy has not started to recrystallize after recrystallization annealing at 450 °C; image 3 In (b), it can be seen that the A2 alloy has begun to partially recrystallize after recrystallization annealing at 400 °C; image 3 In (c), it can be seen that the A3 alloy has also begun to partially recrystallize after recrystallization annealing at 375 °C; image 3 In (d), it can be seen that the A4 alloy has been completely recrystallized after recrystallization annealing at 325 °C. ...
PUM
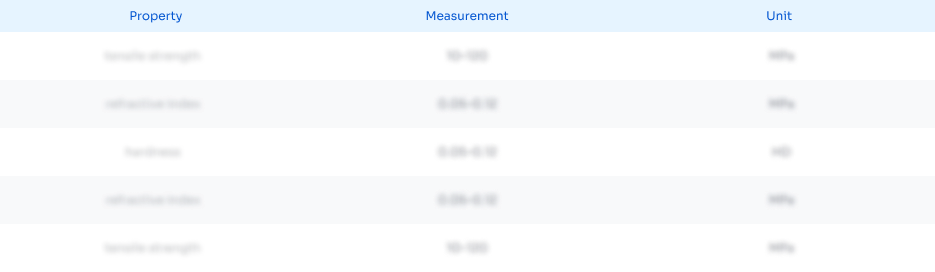
Abstract
Description
Claims
Application Information

- R&D
- Intellectual Property
- Life Sciences
- Materials
- Tech Scout
- Unparalleled Data Quality
- Higher Quality Content
- 60% Fewer Hallucinations
Browse by: Latest US Patents, China's latest patents, Technical Efficacy Thesaurus, Application Domain, Technology Topic, Popular Technical Reports.
© 2025 PatSnap. All rights reserved.Legal|Privacy policy|Modern Slavery Act Transparency Statement|Sitemap|About US| Contact US: help@patsnap.com