Anti-clogging stereoscopic structure grinding tool and preparation method thereof
A three-dimensional structure, anti-clogging technology, used in grinding/polishing equipment, abrasives, grinding devices, etc., can solve the problems of easy adhesion of abrasive dust, affecting the grinding effect, heating and turning red, etc., to ensure surface finish, improve The effect of grinding efficiency and good printing effect
- Summary
- Abstract
- Description
- Claims
- Application Information
AI Technical Summary
Problems solved by technology
Method used
Image
Examples
Embodiment 1
[0038] 1) Glue coating: under vacuum conditions, pre-coat a layer of pre-treated glue layer on the corona-treated abrasive substrate 1, using 220-line anilox rollers, elastic scraping on the table, and reverse scraping. Scratch coating, drying at 80°C for 18 minutes for pre-drying, and then applying a layer of resin coating with a thickness of 90-100 μm by electrostatic spraying under vacuum conditions.
[0039] 2) Mixing: Mix the abrasive into the phenolic resin resin at a mass ratio of 1:2, stir for 25 minutes, then add activated ZSM-5 zeolite powder at μm level and stir for 25 minutes, and then add aromatic polyacids as organic ligands The coordination polymer self-assembled with aluminum ions is stirred for another 25 minutes, dried in an equal-step temperature field environment, and gradually heated from 25°C to 55°C at a rate of 5°C / 10min, so that the mixture can fully react to obtain a mixture;
[0040] 3) Printing: The mixture obtained in step 2 is continuously scraped...
Embodiment 2
[0044] 1) Glue coating: under vacuum conditions, pre-coat a layer of pre-treated glue layer on the corona-treated abrasive substrate 1, using 200-line anilox rollers, elastic scraping on the table, and reverse scraping. Scratch coating, drying at 80°C for 17 minutes for pre-drying, and then applying a resin coating with a thickness of 90-100 μm by electrostatic spraying under vacuum conditions.
[0045] 2) Mixing: Mix the abrasive into the phenolic resin with a mass ratio of 1:2, stir for 22 minutes, then add μm-level activated zeolite powder and stir for 27 minutes, then add the multi-dentate organic ligands containing oxygen and nitrogen and The coordination polymer formed by the self-assembly of aluminum ions is stirred for another 25 minutes, dried in an equal-step temperature field environment, and gradually heated from 25°C to 55°C at a rate of 3°C / 10min, so that the mixture can fully react to obtain a mixture;
[0046] 3) Printing: The mixture obtained in step 2 is cont...
Embodiment 3
[0050] 1) Glue coating: under vacuum conditions, pre-coat a layer of pre-treated glue layer on the corona-treated abrasive base material 1, using 300-line anilox rollers, elastic scraping on the table, and reverse scraping. Scratch coating, drying at 80°C for 18 minutes for pre-drying, and then applying a layer of resin coating with a thickness of 90-100 μm by electrostatic spraying under vacuum conditions.
[0051] 2) Mixing: Mix the abrasive into the phenolic resin resin at a mass ratio of 1:2.5, stir for 28 minutes, then add activated zeolite powder of μm level and stir for 21 minutes, then add the multi-dentate organic ligands containing oxygen and nitrogen and The coordination polymer formed by the self-assembly of aluminum ions is stirred for another 24 minutes, dried in an equal-step temperature field environment, and gradually heated from 25°C to 55°C at a rate of 6°C / 10min, so that the mixture can fully react to obtain a mixture;
[0052] 3) Printing: The mixture obta...
PUM
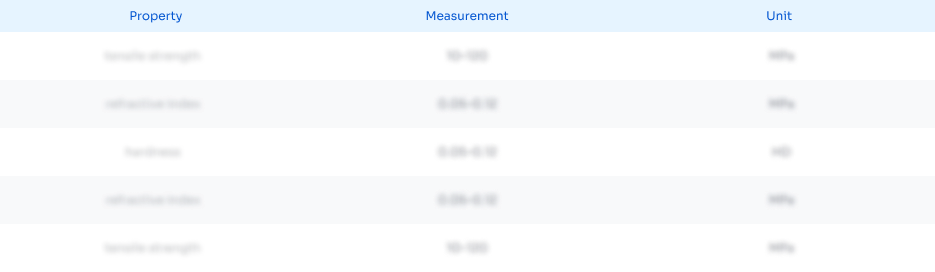
Abstract
Description
Claims
Application Information

- R&D
- Intellectual Property
- Life Sciences
- Materials
- Tech Scout
- Unparalleled Data Quality
- Higher Quality Content
- 60% Fewer Hallucinations
Browse by: Latest US Patents, China's latest patents, Technical Efficacy Thesaurus, Application Domain, Technology Topic, Popular Technical Reports.
© 2025 PatSnap. All rights reserved.Legal|Privacy policy|Modern Slavery Act Transparency Statement|Sitemap|About US| Contact US: help@patsnap.com