Solid oxide fuel cell stainless steel bipolar connector and manufacturing method thereof
A solid oxide, bipolar connector technology, applied in the direction of fuel cells, fuel cell parts, final product manufacturing, etc., can solve the problems of insufficient bonding force between the surface modification layer and the substrate, and the surface modification layer is not dense enough. , to achieve the effects of excellent interface compatibility, excellent high temperature oxidation resistance, and good electronic conductivity
- Summary
- Abstract
- Description
- Claims
- Application Information
AI Technical Summary
Problems solved by technology
Method used
Image
Examples
Embodiment 1
[0019] Before electroplating, cut the 430 (containing Cr17%) stainless steel plate into a sample with a size of 2cm×4cm×0.1cm, and punch out the gas flow field on the surface; use dilute sulfuric acid solution, acetone, alcohol, etc. to clean the surface of the sample in sequence To remove impurities such as organic matter on the surface and oxide layers. The cleaned sample is activated by pulse current on the surface of the sample, and the negative current density in the activation process is 6A / dm 2 , the forward current density is 4A / dm 2 , The positive and negative pulse times are 0.1ms and 0.4ms respectively, and the total activation time is 5min. After the sample has been surface activated, the sample is then subjected to pulse electrodeposition of a Co-Ni alloy layer with a forward current density of 3A / dm 2 The negative current density is 2A / dm 2 , the positive and negative pulse time ratio is 1.5:1.0, and the total plating time is 30min. The plating solution used ...
Embodiment 2
[0021] 430 (containing Cr17%) stainless steel is made into the sample of embodiment 1, and the cleaning process and activation process are the same as embodiment 1. After the sample is surface activated, the sample is pulsed electrodeposited Co-Cu alloy layer, the forward current density is 2A / dm 2 The negative current density is 1A / dm 2 , the positive and negative pulse time ratio is 3.0:1.0, and the total pulse electrodeposition time of the sample is 45min. The bath composition is CuSO 4 (0.10mol / L), HBO 3 (0.64mol / L), CoSO 4 (1.20mol / L), C 12 h 25 NaO 4 S (0.03mol / L), the pH value of the plating solution was adjusted to pH=3.0 by dilute sulfuric acid (4mol / L). The bath temperature was 70°C. Put the electroplated 430 stainless steel into a tube furnace, raise the temperature to 930°C in the air, and keep it warm for 0.5h to get CuCo with spinel structure on the surface. 2 o 4 Coated surface-modified iron-based alloy interconnects for solid oxide fuel cells.
Embodiment 3
[0023]Crofer22AU (containing Cr22%) stainless steel is made the sample of embodiment 1, and cleaning process is the same as embodiment 1; The negative current density of activation process is 3A / dm 2 , the forward current density is 1A / dm 2 , The positive and negative pulse times are 0.2ms and 0.3ms respectively, and the total activation time is 25min. After the sample has been surface activated, the sample is then subjected to pulse electrodeposition of a Co metal layer with a forward current density of 1A / dm 2 The negative current density is 1A / dm 2 , the ratio of positive pulse time to negative pulse time is 3.0:1.0, and the pulse electrodeposition time of the sample is 30min. The bath composition is CoSO 4 (0.80mol / L), HBO 3 (0.02mol / L), C 12 h 25 NaO 4 S (0.2mol / L), the pH value of the plating solution was adjusted to pH=4.5 by dilute sulfuric acid (4mol / L). The bath temperature is 45°C. Put the electrodeposited Crofer22AU stainless steel into a box furnace, rais...
PUM
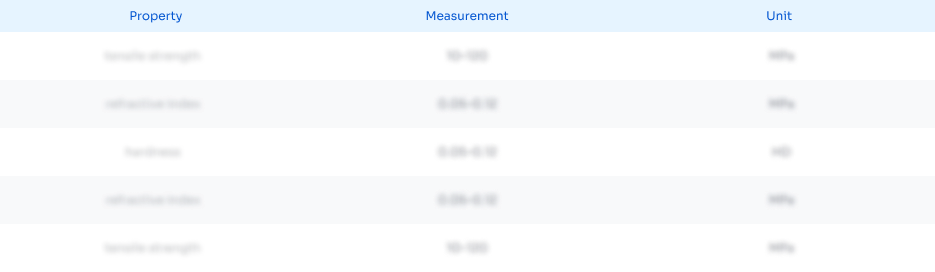
Abstract
Description
Claims
Application Information

- R&D
- Intellectual Property
- Life Sciences
- Materials
- Tech Scout
- Unparalleled Data Quality
- Higher Quality Content
- 60% Fewer Hallucinations
Browse by: Latest US Patents, China's latest patents, Technical Efficacy Thesaurus, Application Domain, Technology Topic, Popular Technical Reports.
© 2025 PatSnap. All rights reserved.Legal|Privacy policy|Modern Slavery Act Transparency Statement|Sitemap|About US| Contact US: help@patsnap.com