Multihole ceramic bearing and manufacturing method thereof
A technology of porous ceramics and a manufacturing method, applied in the field of porous ceramic materials, can solve the problems of low temperature aging, aggravated bearing wear, low thermal conductivity, etc., and achieve the effect of solving low temperature aging and improving mechanical properties
- Summary
- Abstract
- Description
- Claims
- Application Information
AI Technical Summary
Problems solved by technology
Method used
Image
Examples
preparation example Construction
[0015] An embodiment of the present invention provides a method for manufacturing a porous ceramic bearing, and a porous ceramic bearing obtained by the method, wherein the process of the method includes the following steps:
[0016] S10, preparing enhanced zirconia composite ceramic powder;
[0017] S20, fully mixing the enhanced zirconia composite ceramic powder with the pore-forming agent and the binder to obtain a mixed slurry;
[0018] S30, drying the mixed slurry to obtain dry powder;
[0019] S40, molding the dry powder into a mold to obtain a green body;
[0020] S50, sintering the green body to obtain a bearing green body;
[0021] S60, vacuum immersing the bearing body in oil.
[0022] In the preparation method of the present invention, the enhanced zirconia composite ceramic powder is used to make bearings, wherein the partially stabilized zirconia after the technical means strengthens contains more reinforcing functional components, which improves the mechanical...
Embodiment 1
[0058] In this embodiment 1, 3Y-TZP with the best performance in the existing partially stabilized zirconia is used, and the specific steps are as follows:
[0059] S11, weigh 41 kg of 3Y-TZP powder and dissolve it in water to make 80g / L zirconia solution;
[0060] S12, adding 200 g of ammonium polyacrylate to the solution in step S11, and ultrasonically dispersing for 2 hours to prepare a zirconia suspension;
[0061] S13, taking 3.2 kg of α-alumina powder and adding it to the suspension obtained in step S12, stirring evenly, and ultrasonically dispersing for 2 hours to obtain a dispersion;
[0062] S14, vacuum filter the dispersion to remove most of the water to prevent delamination of the additive and the matrix, and then put it in an oven for drying at 60 degrees to obtain a reinforced zirconia composite ceramic powder block;
[0063] S15, put the block obtained in step S14 into an air furnace for sintering, wherein during the sintering process, the temperature can be rai...
Embodiment 2
[0076] This embodiment 2 is carried out using the same method steps as in embodiment 1, except that the second reinforcement phase alumina grains in step S40 of embodiment 1 are replaced by a particle mixture of whiskers and nano-zirconia; at the same time in step S21 The amount of pore-forming agent added is increased to a ratio of 4:6 to the reinforced zirconia; and step S40 changes the dry pressing molding method to the following injection molding method:
[0077] S40, mix the spray-dried porous ceramic powder with paraffin, polyethylene, polypropylene, and oleic acid evenly, and then put it into a mixer, set the mixing temperature to 180° C., and the mixing time to 3 hours. Make an injection molding metal mold according to the shrinkage rate of the feed material and the drawing size of the bearing, and then crush the mixed feed material and put it into the injection molding machine to form a green body with a qualified appearance size.
[0078]After the completion, the oil...
PUM
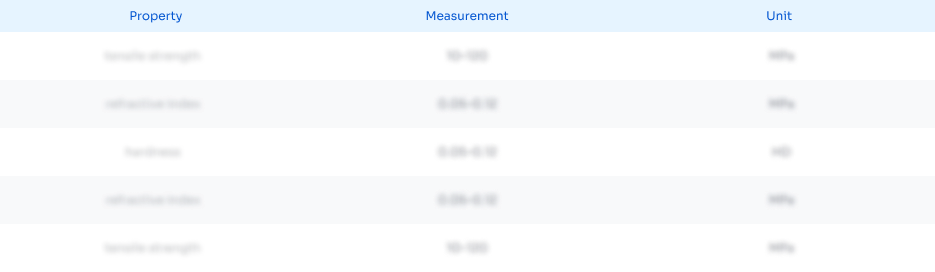
Abstract
Description
Claims
Application Information

- R&D
- Intellectual Property
- Life Sciences
- Materials
- Tech Scout
- Unparalleled Data Quality
- Higher Quality Content
- 60% Fewer Hallucinations
Browse by: Latest US Patents, China's latest patents, Technical Efficacy Thesaurus, Application Domain, Technology Topic, Popular Technical Reports.
© 2025 PatSnap. All rights reserved.Legal|Privacy policy|Modern Slavery Act Transparency Statement|Sitemap|About US| Contact US: help@patsnap.com