Rare-earth/rubber composite material easily subjected to laser engraving
A technology for laser engraving and composite materials, applied in the field of rare earth/rubber composite materials, can solve the problems of reducing the degree of carbonization of the engraving surface, increasing the cost of rubber composite materials, and increasing the cost.
- Summary
- Abstract
- Description
- Claims
- Application Information
AI Technical Summary
Problems solved by technology
Method used
Image
Examples
Embodiment 1
[0027] At room temperature, wrap 100 parts of natural rubber on double rollers on the rubber mixer, then add 5 parts of zinc oxide and 2 parts of stearic acid in sequence, and mix for 0.5 minutes; then add 0.5 parts of anti-aging agent RD, and add anti-aging agent 4010NA to 0.5 1 part, mixed for 2 minutes; then add 1 part of VN3 white carbon black, 1 part of N220 carbon black and 0.5 part of Si69 in batches, then mix for 5 minutes, then add 1 part of chlorinated paraffin, mix for 0.5 minutes, then add 1 part of nano-lanthanum oxide, and then knead for 0.5 minutes, and finally add 1.5 parts of accelerator CZ and 3 parts of sulfur into the open mill, thin pass 5 times, and then stop for 4 hours, then re-mill for 5 minutes and vulcanize molding get composites.
[0028] The accelerator CZ is N-cyclohexyl-2-benzothiazole sulfenamide; Si69 is bis(triethoxysilylpropyl) tetrasulfide; antioxidant RD is 2,2,4-trimethyl -1,2-dihydroquinoline polymer (belongs to ketone-amine reaction pro...
Embodiment 2
[0030]At room temperature, wrap 100 parts of natural rubber on double rollers on the rubber mixer, then add 5 parts of zinc oxide and 2 parts of stearic acid in sequence, and mix for 0.5 minutes; then add 4 parts of anti-aging agent RD, add anti-aging agent 4010NA to 5 and 1 part of protective wax, mixed for 5 minutes; then add 10 parts of VN3 silica, 10 parts of carbon nanotubes and 10 parts of N234 carbon black and 4 parts of Si69, and then add 10 parts of brominated epoxy resin , 10 parts of alumina and 5 parts of red phosphorus, then mixed for 10 minutes, added 10 parts of nano-cerium oxide, and mixed for 2 minutes, and finally added 1.5 parts of accelerator CZ, 0.2 parts of accelerator TT and Sulfur 3 parts, thin pass 5 times, and then park for 4 hours, then re-mill for 5 minutes and vulcanize to obtain a composite material.
[0031] The accelerator TT is tetramethylthiuram disulfide; the protective wax is a kind of anti-aging agent, which plays the role of anti-ozone agi...
Embodiment 3
[0033] At room temperature, wrap 100 parts of natural rubber on double rollers on the rubber mixer, then add 4 parts of zinc oxide and 1 part of stearic acid in sequence, and mix for 0.5 minutes; then add 4 parts of antioxidant MB, and add antioxidant 445 to make 5 and 4 parts of protective wax, mix for 5 minutes; then add 50 parts of T383 white carbon black, 5 parts of nylon staple fiber and 4 parts of Si75 in batches, then mix for 10 minutes, then add 20 parts of hydrotalcite and 2 parts Then add 5 parts of nano-cerium oxide, 5 parts of nano-neodymium oxide, 10 parts of nano-gadolinium carbonate, 10 parts of nano-lanthanum hydroxide and 20 parts of nano-samarium nitrate, mix for 5 minutes, and then add 5 parts 1 part of paraffin oil, kneaded for 10 minutes, finally added 1.5 parts of accelerator DM, 3 parts of accelerator DTDM and 2 parts of sulfur in the open mill, thinly passed 5 times of sheeting, then parked for 4 hours, and then re-milled for 5 Minutes and vulcanization...
PUM
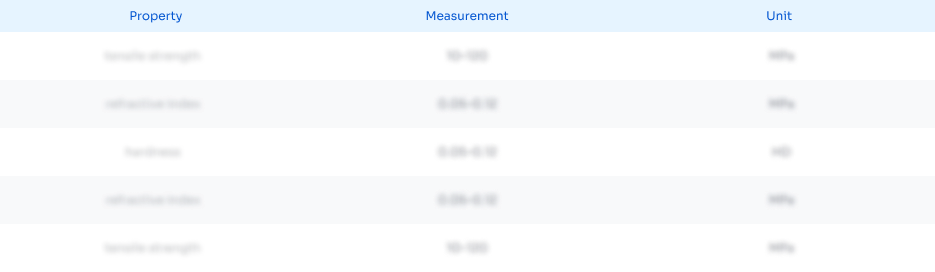
Abstract
Description
Claims
Application Information

- Generate Ideas
- Intellectual Property
- Life Sciences
- Materials
- Tech Scout
- Unparalleled Data Quality
- Higher Quality Content
- 60% Fewer Hallucinations
Browse by: Latest US Patents, China's latest patents, Technical Efficacy Thesaurus, Application Domain, Technology Topic, Popular Technical Reports.
© 2025 PatSnap. All rights reserved.Legal|Privacy policy|Modern Slavery Act Transparency Statement|Sitemap|About US| Contact US: help@patsnap.com