Copper-aluminum abutting and lap joint type conducting bar
A technology of conductive strips and aluminum strips, applied in conductive connection, welding/welding/cutting items, conductors, etc., can solve the problems that the connection parts cannot reach the conductivity of aluminum strips, safety risks, and reduce the current of conductive strips. Overcome the limitations of cross-sectional shape selection, solve reliable connections, and overcome the effect of interface oxidation
- Summary
- Abstract
- Description
- Claims
- Application Information
AI Technical Summary
Problems solved by technology
Method used
Image
Examples
Embodiment 1
[0017] Embodiment 1: The two ends of the aluminum bar 1 are butted with the copper bar 2, and the butt joint 3 is welded together by mechanical friction stir welding to form a copper-aluminum butt-connected conductive bar.
Embodiment 2
[0018] Embodiment 2: The two ends of the aluminum row 1 are docked with the copper row 2, and at the same time, an aluminum row 4 is superimposed on one side of the conductive row. For the butt joint part 41 of the copper bar, the butt welding and superimposition welding are performed on the butt joint part 3 at one time through the method of mechanical friction stir welding, so that the aluminum bar, the copper bar, and the superimposed aluminum bar become a butt joint and superimposed conductive bar.
PUM
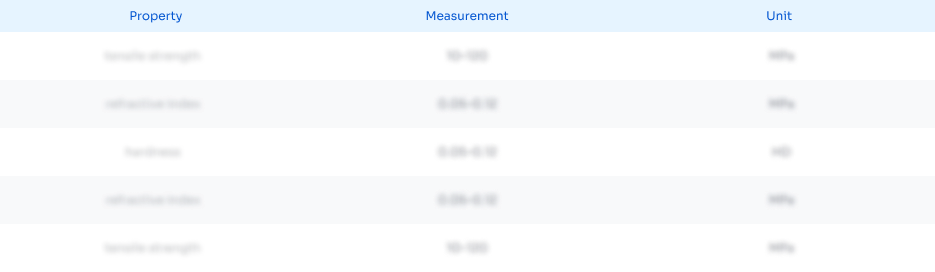
Abstract
Description
Claims
Application Information

- R&D Engineer
- R&D Manager
- IP Professional
- Industry Leading Data Capabilities
- Powerful AI technology
- Patent DNA Extraction
Browse by: Latest US Patents, China's latest patents, Technical Efficacy Thesaurus, Application Domain, Technology Topic, Popular Technical Reports.
© 2024 PatSnap. All rights reserved.Legal|Privacy policy|Modern Slavery Act Transparency Statement|Sitemap|About US| Contact US: help@patsnap.com