Method for preparing bismuth electrolyte with bismuth oxide slag
A technology of bismuth oxide slag and bismuth electrolyte, which is applied in the direction of process efficiency improvement, photographic technology, instruments, etc., can solve the problems of low metal recovery rate, low metal recovery rate, and low processing capacity, and achieve less backlog and metal recovery The effect of high rate and short processing time
- Summary
- Abstract
- Description
- Claims
- Application Information
AI Technical Summary
Problems solved by technology
Method used
Image
Examples
Embodiment 1
[0029] The blocky bismuth oxide slag is crushed and finely ground to a particle size of 100% through a sieve with an aperture of 150um. The main components are (%) by weight: Bi33.0, Pb12.0, Cu2.8, Ag0.85 and Sb1.2, the rest is O; fluosilicic acid is an industrial grade reagent, the content of fluosilicic acid is 40%, lead powder and sulfuric acid are both industrial grade reagents.
[0030] Prepare 1800ml of fluosilicic acid solution with a concentration of 280g / L, add 600g of bismuth oxide powder with the above ingredients, keep the temperature at 60°C and the stirring speed at 200r / min, react for 3h and filter, the volume of the leachate is 1750ml, and its main component is (g / L ): Bi118.2, Pb40.8, Cu9.72 and Sb4.28, the leached slag weighs 60.5g after washing with water.
[0031] Add lead powder to the fluosilicic acid leaching solution to replace copper, keep the solution temperature at 60°C and 250r / min, add 60g of lead powder and react for 2 hours, then filter, wash the...
Embodiment 2
[0033] The massive bismuth oxide slag was crushed and finely ground to a particle size of 100% and passed through a sieve with an aperture of 44um. Prepare 3600ml of fluosilicic acid solution with a concentration of 400g / L, add 600g of bismuth oxide powder with the above ingredients, keep the temperature at 80°C and stirring speed at 250r / min, react for 6h and then filter to obtain fluosilicic acid leachate. Add lead powder with a copper mass content of 3.3 times to the fluosilicic acid leaching solution to replace copper, keep the solution temperature at 80°C and 250r / min, react for 1 hour, filter, and wash the replacement slag with water and then dry it. After removing copper, add sulfuric acid with a mass content of 1.60 times the lead, react for 1 hour and then filter, keep the solution temperature at 75°C and 150r / min, add 50ml of sulfuric acid and react for 2 hours, then filter to obtain a bismuth electrolyte.
Embodiment 3
[0035] The massive bismuth oxide slag was crushed and finely ground to a particle size of 100% and passed through a sieve with an aperture of 220um. Prepare 1800ml of fluosilicic acid solution with a concentration of 560g / L, add 600g of bismuth oxide powder with the above ingredients, keep the temperature at 40°C and stirring speed at 200r / min, react for 1h and filter to obtain fluosilicic acid leachate. Add lead powder with a copper mass content of 3.5 times to the fluorosilicate leaching solution to replace copper, keep the solution temperature at 40°C and 150r / min, react for 2 hours, filter, and wash the replacement slag with water and then dry it. After removing copper, add sulfuric acid with a mass content of 0.60 times the lead, react for 1 hour and then filter, keep the solution temperature at 40°C and 250r / min, add 50ml of sulfuric acid and react for 1 hour, then filter to obtain a bismuth electrolyte.
PUM
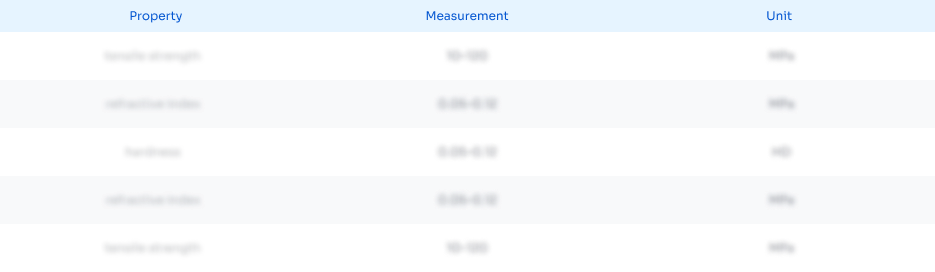
Abstract
Description
Claims
Application Information

- R&D
- Intellectual Property
- Life Sciences
- Materials
- Tech Scout
- Unparalleled Data Quality
- Higher Quality Content
- 60% Fewer Hallucinations
Browse by: Latest US Patents, China's latest patents, Technical Efficacy Thesaurus, Application Domain, Technology Topic, Popular Technical Reports.
© 2025 PatSnap. All rights reserved.Legal|Privacy policy|Modern Slavery Act Transparency Statement|Sitemap|About US| Contact US: help@patsnap.com