Iron-cobalt alloy and preparation method of magnetizing pole head of iron-cobalt alloy
An iron-cobalt alloy, magnetizing pole technology, applied in the direction of manufacturing tools, magnetic objects, heat treatment equipment, etc., can solve the problems of low saturation magnetic induction intensity of pure iron materials, increased material coercivity, and increased use costs, etc. Inexpensive cost, low coercivity, and the effect of mass production
- Summary
- Abstract
- Description
- Claims
- Application Information
AI Technical Summary
Problems solved by technology
Method used
Examples
Embodiment 1
[0023] 1. The iron-cobalt alloy composition (percentage by weight) of Example 1 of the present invention is Co 29.12%, Nb 0.29%, Zr 0.11%, La 0.06%, and the balance is Fe.
[0024] 2. Its preparation method is;
[0025] ①. Raw materials such as electrolytic cobalt, high-purity iron, niobium bar, zirconium bar, and rare earth lanthanum are vacuum smelted and cast into alloy ingots;
[0026] ②. After cleaning the sundries and defects on the surface of the alloy ingot, heat the alloy to 1180°C and keep it warm for forging. After forging the pole head blank, cool the forging to a temperature of 810°C, and put it directly into the room where the temperature is maintained at -8°C to -15°C. Quenching in a mixed solution of dry ice and water;
[0027] ③ After quenching and heat treatment, the material is machined into a magnetized pole head;
[0028] ④. Heat the magnetized pole head to 550°C in a hydrogen protective atmosphere, keep it warm for 2 hours, cool it in the furnace to bel...
Embodiment 2
[0033] 1. The composition (percentage by weight) of the iron-cobalt alloy in Example 2 of the present invention is Co 31.91%, Nb 0.25%, Zr 0.15%, La 0.09%, and the balance is Fe.
[0034] 2. Its preparation method is:
[0035] ①. Raw materials such as electrolytic cobalt, high-purity iron, niobium bar, zirconium bar, and rare earth lanthanum are vacuum smelted and cast into alloy ingots;
[0036] ②. After cleaning the sundries and defects on the surface of the alloy ingot, heat the alloy to 1180°C and keep it warm for forging. After forging the pole head blank, cool the forging to a temperature of 850°C, and put it directly into the room where the temperature is maintained at -8°C to -15°C. Quenching in a mixed solution of dry ice and water;
[0037] ③ After quenching and heat treatment, the material is machined into a magnetized pole head;
[0038] ④. Heat the magnetized pole head to 600°C in a hydrogen protective atmosphere, keep it warm for 1 hour, and cool it in the furn...
Embodiment 3
[0043] 1. The iron-cobalt alloy composition (percentage by weight) of Example 3 of the present invention is Co 30.75%, Nb 0.26%, Zr 0.21%, La 0.05%, and the balance is Fe.
[0044] 2. Its preparation method is:
[0045] ①. Raw materials such as electrolytic cobalt, high-purity iron, niobium bar, zirconium bar, and rare earth lanthanum are vacuum smelted and cast into alloy ingots;
[0046] ②. After cleaning the sundries and defects on the surface of the alloy ingot, heat the alloy to 1180°C and keep it warm for forging. After forging the pole head blank, cool the forging to 820°C, and put it directly into the room where the temperature is maintained at -8°C to -15°C. Quenching in a mixed solution of dry ice and water;
[0047] ③ After quenching and heat treatment, the material is machined into a magnetized pole head;
[0048] ④. Heat the magnetized pole head to 570°C in a hydrogen protective atmosphere, keep it warm for 1.5 hours, cool it in the furnace to below 100°C, and t...
PUM
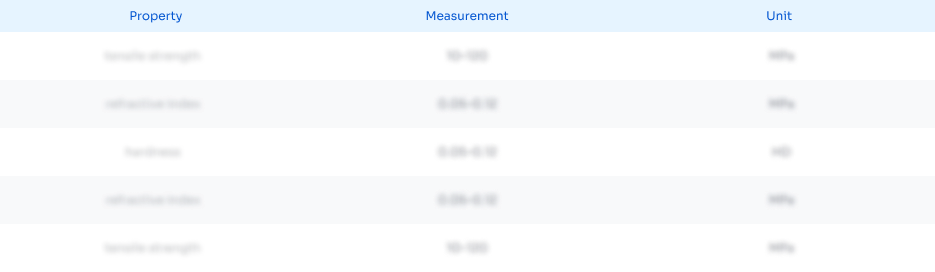
Abstract
Description
Claims
Application Information

- R&D Engineer
- R&D Manager
- IP Professional
- Industry Leading Data Capabilities
- Powerful AI technology
- Patent DNA Extraction
Browse by: Latest US Patents, China's latest patents, Technical Efficacy Thesaurus, Application Domain, Technology Topic, Popular Technical Reports.
© 2024 PatSnap. All rights reserved.Legal|Privacy policy|Modern Slavery Act Transparency Statement|Sitemap|About US| Contact US: help@patsnap.com