Oxygen-free cooling and residual heat recovering method for magnetizing-roasted iron ore product
A magnetization roasting and waste heat recovery technology, applied in the field of metallurgy, can solve the problems of complex equipment composition, low theoretical combustion temperature, waste heat loss of materials, etc., so as to reduce production water consumption and environmental pollution, improve product quality, and realize the effect of waste heat recovery.
- Summary
- Abstract
- Description
- Claims
- Application Information
AI Technical Summary
Problems solved by technology
Method used
Examples
Embodiment 1
[0019] (1) Material selection, the high-temperature material with a temperature of 800 ° C after magnetization and roasting and a particle size of 8 mm is loaded from the upper part of the vertical cooler;
[0020] (2) Choice of cooling medium, choose CO or H 2 Blast furnace gas with a volume content of 10% is introduced from the lower part of the vertical cooler, and the blast furnace gas flow rate is controlled to be 0.8 m / s;
[0021] (3) Heat exchange between materials and blast furnace gas. The high-temperature materials and blast furnace gas are exchanged in the process of countercurrent flow in the vertical cooler. The temperature of high-temperature materials is reduced to 200 ° C, and the temperature of blast furnace gas is raised to 700 ° C. After heat exchange The blast furnace gas is discharged from the upper part of the vertical cooler, and the cooled material is discharged from the lower part of the vertical cooler.
[0022] Compared with the traditional magnetiz...
Embodiment 2
[0024] A. Material selection, the high-temperature material with a temperature of 830°C after magnetization and roasting and a particle size of 15 mm is loaded from the upper part of the vertical cooler;
[0025] B. The choice of cooling medium, choose CO or H 2 Blast furnace gas with a volume content of 20% is introduced from the lower part of the vertical cooler, and the blast furnace gas flow rate is controlled to be 1.2 m / s;
[0026] C. Heat exchange between materials and blast furnace gas. High temperature materials and blast furnace gas flow countercurrently in the vertical cooler for heat exchange. The temperature of high temperature materials decreases below 150°C, while the temperature of blast furnace gas rises to 730°C. After heat exchange The blast furnace gas is discharged from the upper part of the vertical cooler, and the cooled material is discharged from the lower part of the vertical cooler.
[0027] Compared with the traditional magnetization roasting and c...
Embodiment 3
[0029] A. Material selection, the high-temperature material with a temperature of 850°C after magnetization and roasting and a particle size of 25 mm is loaded from the upper part of the vertical cooler;
[0030] B. The choice of cooling medium, choose CO or H 2 Blast furnace gas with a volume content of 30% is introduced from the lower part of the vertical cooler, and the blast furnace gas flow rate is controlled to be 1.5 m / s;
[0031] C. Heat exchange between materials and blast furnace gas. High temperature materials and blast furnace gas flow countercurrently in the vertical cooler for heat exchange. The temperature of high temperature materials decreases to 100°C, while the temperature of blast furnace gas rises to 750°C. After heat exchange The blast furnace gas is discharged from the upper part of the vertical cooler, and the cooled material is discharged from the lower part of the vertical cooler.
[0032] Compared with the traditional magnetization roasting and cool...
PUM
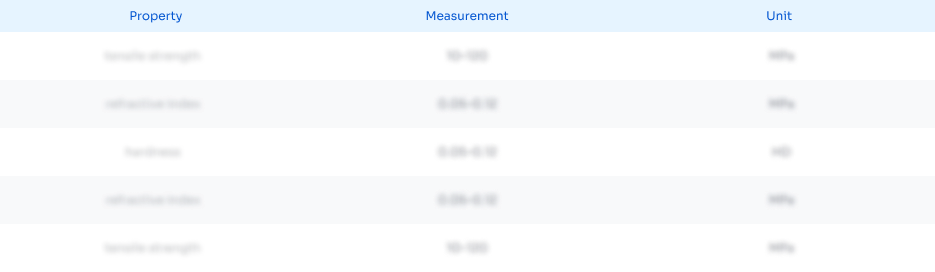
Abstract
Description
Claims
Application Information

- R&D Engineer
- R&D Manager
- IP Professional
- Industry Leading Data Capabilities
- Powerful AI technology
- Patent DNA Extraction
Browse by: Latest US Patents, China's latest patents, Technical Efficacy Thesaurus, Application Domain, Technology Topic, Popular Technical Reports.
© 2024 PatSnap. All rights reserved.Legal|Privacy policy|Modern Slavery Act Transparency Statement|Sitemap|About US| Contact US: help@patsnap.com