Processing method of heavy oil
A processing method and heavy oil technology, applied in the petroleum industry, chemical instruments and methods, inorganic chemistry, etc., can solve the problems of large bed pressure drop, poor thermal conductivity, large agglomerates and fine coke powder, etc., to reduce emissions, reduce Effect of gasification temperature and process cost reduction
- Summary
- Abstract
- Description
- Claims
- Application Information
AI Technical Summary
Problems solved by technology
Method used
Image
Examples
Embodiment 1
[0046] The catalytic cracking catalyst with the trade name of CRC-1 and heavy oil with a residual carbon value of 15.10% by weight, a metal content of 50 μg / g, and a sulfur content of 1.12% (mass) are subjected to a contact cracking reaction in a contact cracking unit. The contact cracking reaction process The conditions are: cracking temperature 460°C, space velocity 10h -1 , the agent-oil ratio is 10, the water-oil ratio is 0.1, and the coke content of the resulting spent agent is 1.8% by weight.
[0047] The spent agent is stripped with steam for 30 minutes, and the stripped spent agent is mixed with the regenerated contact agent from the regenerator to exchange heat. The temperature of the spent agent reaches 610°C, and the oxygen 15% is introduced in terms of mole fraction. , water 85% gasification agent, gasification reaction occurs, and the obtained target product CO+H 2 The volume fraction (dry basis) is 71.5%.
[0048] The target product CO+H obtained from the gasif...
Embodiment 2
[0050] The catalytic cracking catalyst whose trade name is CRC-1 is mechanically mixed with the gasification catalyst GC-1, the mass ratio of the two is 9:1, and then the residual carbon value is 18.10% by weight, the metal is 200 μg / g, and the sulfur content is 1.12% (mass) heavy oil undergoes a contact cracking reaction in the contact cracking unit, and the process conditions of the contact cracking reaction are: cracking temperature 500°C, space velocity 20h -1 , the agent-oil ratio is 7, the water-oil ratio is 0.2, and the coke content of the resulting spent agent is 2.5% by weight.
[0051] The spent agent is stripped with steam for 30 minutes, and the stripped spent agent is mixed with the regenerated contact agent from the regenerator to exchange heat. The temperature of the spent agent reaches 700°C, and the oxygen 10% is introduced in terms of mole fraction. , water 80%, part of CO from the conversion unit 2 10% gasification agent, gasification reaction occurs, and t...
Embodiment 3
[0054] The silicon-aluminum material MFC-1 and heavy oil with a residual carbon value of 35.0% by weight, a metal content of 425 μg / g, and a sulfur content of 3.12% (mass) undergo a contact cracking reaction in a contact cracking unit. The process conditions for the contact cracking reaction are: cracking temperature 520℃, space velocity 50h -1, the agent-to-oil ratio is 20, the water-to-oil ratio is 0.5, and the coke content of the resulting spent agent is 2.8% by weight.
[0055] The spent agent was stripped with water steam for 30 minutes, and the stripped spent agent was mixed with the regenerated contact agent from the regenerator to exchange heat. The temperature of the spent agent reached 800°C, and 5% oxygen was introduced in terms of mole fraction. , water 95% gasification agent, gasification reaction occurs, and the target product CO+H is obtained 2 The volume fraction (dry basis) is 83.5%.
[0056] The target product CO+H obtained from the gasification unit 2 The...
PUM
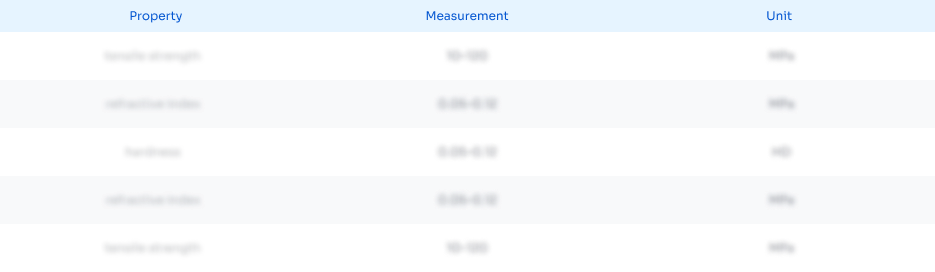
Abstract
Description
Claims
Application Information

- R&D
- Intellectual Property
- Life Sciences
- Materials
- Tech Scout
- Unparalleled Data Quality
- Higher Quality Content
- 60% Fewer Hallucinations
Browse by: Latest US Patents, China's latest patents, Technical Efficacy Thesaurus, Application Domain, Technology Topic, Popular Technical Reports.
© 2025 PatSnap. All rights reserved.Legal|Privacy policy|Modern Slavery Act Transparency Statement|Sitemap|About US| Contact US: help@patsnap.com