A multi-layer composite film passivation structure and preparation process for mesa high-power semiconductor devices
A multi-layer composite film and semiconductor technology, applied in the fields of semiconductor/solid-state device manufacturing, semiconductor devices, semiconductor/solid-state device components, etc., can solve the problems of inconsistent thermal expansion coefficient, device surface composite enhancement, high surface state density, etc. The effect of reducing lattice defects, repairing lattice damage, alleviating lattice stress and thermal stress
- Summary
- Abstract
- Description
- Claims
- Application Information
AI Technical Summary
Problems solved by technology
Method used
Image
Examples
Embodiment 1
[0024] A preparation process for a multilayer composite film passivation structure of a mesa high-power semiconductor device includes the following process steps in sequence:
[0025] a. Deposit α-polysilicon by LPCVD at a temperature of 570°C and a pressure of 0.3Torr, SiH 4 Flow rate 40cc / min, deposition time 4min;
[0026] b. Deposit semi-insulating polysilicon, using LPCVD deposition, the temperature is 650°C, the pressure is 0.3Torr, SiH 4 Flow 250cc / min, N 2 O flow rate 40cc / min, deposition time 40min;
[0027] c. Deposit a low-temperature thermal oxide layer, using LPCVD deposition, the temperature is 420 ° C, the pressure is 0.3 Torr, SiH 4 Flow 150cc / min, O 2 Flow rate 40cc / min, deposition time 20min;
[0028] d. Deposit Si 3 N 4 , using LPCVD deposition, the temperature is 750 ℃, the pressure is 0.3Torr, SiH 2 Cl 2 Flow 150cc / min, NH 3 Flow rate 400cc / min, deposition time 20min;
[0029] e. Glass passivation, apply lead aluminosilicate glass by scraping me...
Embodiment 2
[0032] A preparation process for a multilayer composite film passivation structure of a mesa high-power semiconductor device includes the following process steps in sequence:
[0033] a. Deposit α-polysilicon, using LPCVD deposition, the temperature is 575°C, the pressure is 0.35Torr, SiH 4 Flow rate 40cc / min, deposition time 4.5min;
[0034] b. Deposit semi-insulating polysilicon, using LPCVD deposition, the temperature is 660°C, the pressure is 0.3Torr, SiH 4 Flow 250cc / min, N 2O flow rate 40cc / min, deposition time 45min;
[0035] c. Deposit a low-temperature thermal oxide layer, using LPCVD deposition, the temperature is 435 ° C, the pressure is 0.3 Torr, SiH 4 Flow 150cc / min, O 2 Flow rate 40cc / min, deposition time 25min;
[0036] d. Deposit Si 3 N 4 , using LPCVD deposition, the temperature is 770 ℃, the pressure is 0.4Torr, SiH 2 Cl 2 Flow 150cc / min, NH 3 Flow rate 400cc / min, deposition time 25min;
[0037] e. Glass passivation, use the method of scraping to c...
Embodiment 3
[0040] A preparation process for a multilayer composite film passivation structure of a mesa high-power semiconductor device includes the following process steps in sequence:
[0041] a. Deposit α-polycrystalline silicon by LPCVD at a temperature of 580°C and a pressure of 0.4Torr, SiH 4 Flow rate 40cc / min, deposition time 5min;
[0042] b. Deposit semi-insulating polysilicon, using LPCVD deposition, the temperature is 670°C, the pressure is 0.3Torr, SiH 4 Flow 250cc / min, N 2 O flow rate 40cc / min, deposition time 50min;
[0043] c. Deposit a low-temperature thermal oxide layer by LPCVD at a temperature of 450°C and a pressure of 0.3Torr, SiH 4 Flow 150cc / min, O 2 Flow rate 40cc / min, deposition time 30min;
[0044] d. Deposit Si 3 N 4 , using LPCVD deposition, the temperature is 800 ℃, the pressure is 0.5Torr, SiH 2 Cl 2 Flow 150cc / min, NH 3 Flow rate 400cc / min, deposition time 30min;
[0045] e. Glass passivation, use the method of scraping to coat lead aluminosilic...
PUM
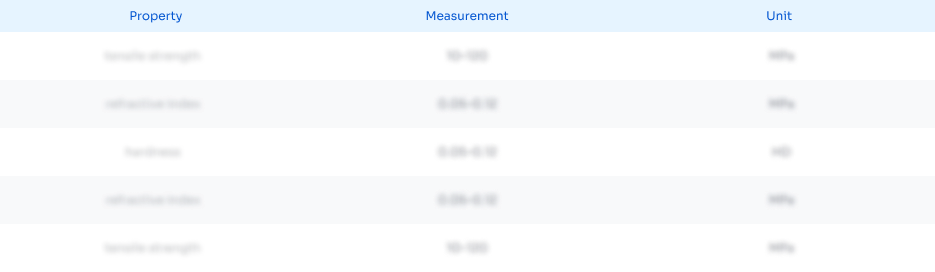
Abstract
Description
Claims
Application Information

- R&D Engineer
- R&D Manager
- IP Professional
- Industry Leading Data Capabilities
- Powerful AI technology
- Patent DNA Extraction
Browse by: Latest US Patents, China's latest patents, Technical Efficacy Thesaurus, Application Domain, Technology Topic, Popular Technical Reports.
© 2024 PatSnap. All rights reserved.Legal|Privacy policy|Modern Slavery Act Transparency Statement|Sitemap|About US| Contact US: help@patsnap.com