Method for efficiently recycling bismuth from monomer bismuth ore
A high-efficiency, monomeric technology, applied to the improvement of process efficiency, photography process, instruments, etc., to achieve the effects of easy operation, low operating cost, and wide concentration adaptability
- Summary
- Abstract
- Description
- Claims
- Application Information
AI Technical Summary
Problems solved by technology
Method used
Examples
Embodiment 1
[0026] Select high-grade bismuth ore from Huaiji, Guangdong, and dry and sample to analyze the main metal element content as follows:
[0027] element Bi Ag Fe Zn co Mg % 0.89 0.60 37.1 0.052 0.03 0.073
[0028] 1) Weigh 1000g of the above bismuth ore and crush it into a 5L beaker, add water at a liquid-solid ratio of 4:1 (ml / l), stir and slurry, add 2.5g of sodium chlorate, and slowly add 70g / L of Leach with hydrochloric acid, control the pH value of the end point to be about 0, and react for 2 hours to obtain a bismuth-containing leachate;
[0029] 2) Filter the bismuth-containing leachate with a precision filter (ceramic membrane precision filter, etc.) to remove solid particle impurities. The filtrate contains bismuth: 2.08g / L, iron: 3.96g / L;
[0030] 3) Inject the leaching solution into the electrowinning circulation tank for swirl electrowinning with a current density of 300A / m 2 , the circulation flow rate is 300 L / h, the electrodep...
Embodiment 2
[0033] Repeat the example 1 leaching operation process to carry out the bismuth ore leaching, the leachate returns and continues to be used for leaching, the acid and the oxidant are still added according to the above-mentioned ratio, and the accumulative enrichment is repeatedly enriched 10 times, and finally obtains a high-concentration bismuth leachate, and the solution contains bismuth: 18.13g / L. Iron content: 24.02g / L; inject the leaching solution into the electrowinning circulation tank for swirl electrowinning. The current density during electrolysis is 500A / m 2 , the circulation flow rate is 600L / h, after continuous electrowinning for 2 hours, the concentration of bismuth in the electrolyte is 5.12g / L, a standard cathode bismuth plate is obtained on the cathode starting plate, and the cumulative recovery rate of bismuth is 97%.
[0034] Current density adopts 550A / m in embodiment 2 2 、600A / m 2 or 700A / m 2 , the circulation flow adopts 500L / h, 550L / h or 580L / h, and ...
PUM
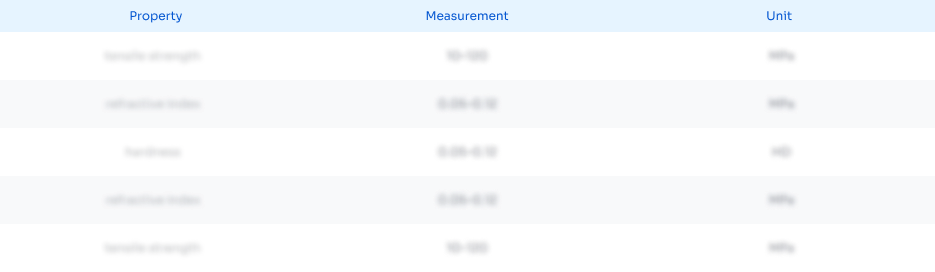
Abstract
Description
Claims
Application Information

- R&D Engineer
- R&D Manager
- IP Professional
- Industry Leading Data Capabilities
- Powerful AI technology
- Patent DNA Extraction
Browse by: Latest US Patents, China's latest patents, Technical Efficacy Thesaurus, Application Domain, Technology Topic, Popular Technical Reports.
© 2024 PatSnap. All rights reserved.Legal|Privacy policy|Modern Slavery Act Transparency Statement|Sitemap|About US| Contact US: help@patsnap.com