Zinc powder pigment and manufacturing method by dry milling
A manufacturing method and technology of zinc powder, applied in the direction of fibrous filler, dyeing physical treatment, etc., can solve the problems of increasing the penetration of water and corrosive media through the coating, changing the physical properties of zinc powder, and the shape cannot be formed into flakes, etc., to achieve improvement Particle uniformity, solving the problem of easy oxidation of the surface, and reducing the effect of temperature rise
- Summary
- Abstract
- Description
- Claims
- Application Information
AI Technical Summary
Problems solved by technology
Method used
Examples
Embodiment Construction
[0019] The present invention is specifically described below with examples, and the scope of the present invention is not limited by the examples.
[0020] A kind of zinc powder pigment of the present invention can be mixed by following component and weight proportion, and its corresponding embodiment 1-3 proportioning is as follows:
[0021] Zinc powder stearic acid coupling agent Dispersant Example 1 97% 2% 0.7% 0.3% Example 2 98.5% 1% 0.4% 0.1% Example 3 98% 1.35% 0.5% 0.15%
[0022] Wherein, in the best implementation mode, the coupling agent is a phthalate coupling agent.
[0023] The dry grinding manufacture method of zinc powder pigment comprises the following steps:
[0024] (1) Ball mill: In a horizontal ball mill, glass balls or zirconia balls or fluorocarbon steel balls with a diameter of 1mm-9mm are used as ball mills, and zinc powder is put into the raw material hopper, and the weight percentage of zinc powder is ...
PUM
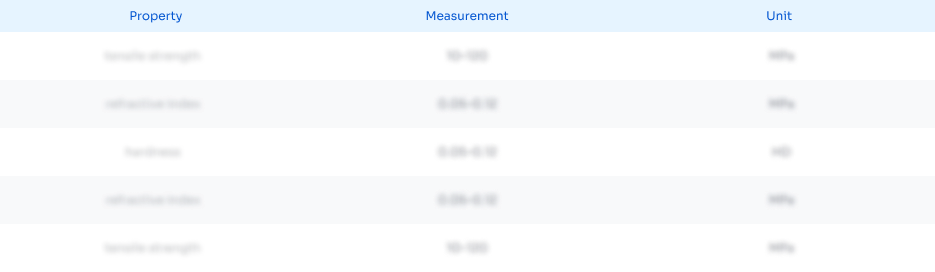
Abstract
Description
Claims
Application Information

- Generate Ideas
- Intellectual Property
- Life Sciences
- Materials
- Tech Scout
- Unparalleled Data Quality
- Higher Quality Content
- 60% Fewer Hallucinations
Browse by: Latest US Patents, China's latest patents, Technical Efficacy Thesaurus, Application Domain, Technology Topic, Popular Technical Reports.
© 2025 PatSnap. All rights reserved.Legal|Privacy policy|Modern Slavery Act Transparency Statement|Sitemap|About US| Contact US: help@patsnap.com