Synthesis method for low-viscosity high-temperature-resistant modified epoxy resin
An epoxy resin and a synthesis method technology, applied in the field of polymer materials and composite materials, can solve the problems of low reaction rate, reduced catalyst activity, low catalytic efficiency, etc., and achieve the effects of low viscosity and cost reduction.
- Summary
- Abstract
- Description
- Claims
- Application Information
AI Technical Summary
Problems solved by technology
Method used
Image
Examples
Embodiment 1
[0026] Put 200g of 4,4'-diaminodiphenylmethane epoxy resin into a 500ml three-necked flask equipped with a thermometer, stirrer, nitrogen inlet tube and condenser, gradually heat and stir; when the temperature rises to 80°C, start to add acrylic acid dropwise 49g, and add 2g of tetramethylammonium chloride, 1g of chromium triacetylacetonate, 1g of methyl hydroquinone, and 1g of p-hydroxyanisole, control the reaction temperature between 80 and 120°C, and measure the acid concentration every hour value until the acid value drops below 15mgKOH / g as the end of the reaction. Cool the reaction product, add 67g of trimethylolpropane triacrylate, control the temperature below 60-80°C and stir evenly to obtain a high-temperature-resistant modified epoxy resin.
Embodiment 2
[0028] Put 200g of 4,4'-diaminodiphenylmethane epoxy resin into a 500ml three-necked flask equipped with a thermometer, stirrer, nitrogen inlet tube and condenser, gradually heat and stir; when the temperature rises to 80°C, start to add acrylic acid dropwise 74g, and added benzyltriethylammonium chloride 2g, chromium salicylate 1g, hydroquinone 1g, 1-oxygen-2,2,6,6-tetramethylpiperidin-4-alcohol (TEMPOL ) 1g, control the reaction temperature between 80-120°C, measure the acid value every hour, until the acid value drops below 15mgKOH / g as the end point of the reaction. Cool the reaction product, add 126g of diallyl phthalate, control the temperature below 60-80°C and stir evenly to obtain a high-temperature-resistant modified epoxy resin.
Embodiment 3
[0030] Put 200g of p-aminophenol epoxy resin into a 500ml three-necked flask equipped with a thermometer, stirrer, nitrogen inlet tube and condenser, gradually heat and stir; when the temperature rises to 80°C, start to drop 44g of methacrylic acid, and add benzyl Trimethylammonium chloride 2g, chromium triacetylacetonate 2g, trimethylhydroquinone 1g, 1-oxyl-2,2,6,6-tetramethylpiperidin-4-ol (TEMPOL) 1g, control The reaction temperature is between 80°C and 120°C, and the acid value is measured every hour until the acid value drops below 15mgKOH / g, which is the end point of the reaction. Cool the reaction product, add 42g of triallyl isocyanurate, control the temperature below 60-80°C and stir evenly to obtain a high-temperature-resistant modified epoxy resin.
PUM
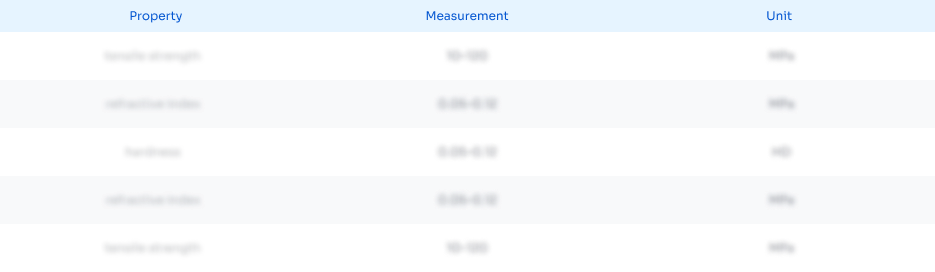
Abstract
Description
Claims
Application Information

- Generate Ideas
- Intellectual Property
- Life Sciences
- Materials
- Tech Scout
- Unparalleled Data Quality
- Higher Quality Content
- 60% Fewer Hallucinations
Browse by: Latest US Patents, China's latest patents, Technical Efficacy Thesaurus, Application Domain, Technology Topic, Popular Technical Reports.
© 2025 PatSnap. All rights reserved.Legal|Privacy policy|Modern Slavery Act Transparency Statement|Sitemap|About US| Contact US: help@patsnap.com