Acid leaching technology for eroding silicon, preserving iron and removing phosphorus in high phosphorus oolitic hematite
A technology of hematite and high-phosphorus oolites is applied in the field of iron ore dephosphorization, which can solve the problems of unqualified iron ore concentrate use, inability to guarantee iron recovery rate, and excessive phosphorus content in concentrate, etc., and achieves control of acid leaching time, The effect of low production cost and strong ore adaptability
- Summary
- Abstract
- Description
- Claims
- Application Information
AI Technical Summary
Problems solved by technology
Method used
Image
Examples
Embodiment 1
[0029] refer to figure 1 Schematic diagram of the process flow for acid leaching of high phosphorus oolitic hematite, the specific process is as follows:
[0030] Step 1, to 100kg iron grade is 46.67%, P 2 o 5 The high-phosphorus oolitic hematite with a mass percentage of 0.87% was successively crushed, wet coarse grinding, spiral chute gravity separation, wet fine grinding, strong magnetic separation and flotation according to the conventional beneficiation process to obtain a mass percentage concentration of 23.2 % iron coarse concentrate pulp, the pulp contains 71.82kg iron coarse concentrate (iron grade is 57.76%, P 2 o 5 The mass percent content is 0.79%); using a cyclone to concentrate the ore slurry to a concentration of 60% in the mass percent of the iron coarse concentrate in the ore slurry;
[0031] Step 2. Put the thickened ore slurry in step 1 into a horizontal mixer (such as lime kiln, rotary kiln and other equipment with similar design principles), and then a...
Embodiment 2
[0034] The present embodiment is the same as embodiment 1, wherein the difference is that the iron retaining agent is ferric sulfate, ferric nitrate, ammonium ferrous sulfate, ferrous sulfate, ferrous nitrate or ferrous chloride, or ferric sulfate, Two or more of ferric chloride, ferric nitrate, ferrous ammonium sulfate, ferrous sulfate, ferrous nitrate and ferrous chloride, the silicon etching agent is hydrofluoric acid, ammonium fluoride, potassium fluoride or fluorine Silver chloride, or two or more of hydrofluoric acid, sodium fluoride, ammonium fluoride, potassium fluoride and silver fluoride.
Embodiment 3
[0036] refer to figure 1 Schematic diagram of the process flow for acid leaching of high phosphorus oolitic hematite, the specific process is as follows:
[0037] Step 1, to 100kg iron grade is 46.67%, P 2 o 5 The high-phosphorus oolitic hematite with a mass percentage of 0.87% was successively crushed, wet coarse grinding, spiral chute gravity separation, wet fine grinding, strong magnetic separation and flotation according to the conventional beneficiation process to obtain a mass percentage concentration of 23.2 % iron coarse concentrate pulp, the pulp contains 71.53kg iron coarse concentrate (iron grade is 58%, P 2 o 5 The mass percent content is 0.6%); using a cyclone to concentrate the ore pulp to a concentration of 70% by mass percentage of iron coarse concentrate in the ore pulp;
[0038] Step 2. Put the thickened ore slurry in step 1 into a horizontal mixer (such as lime kiln, rotary kiln and other equipment with similar design principles), and then add industrial...
PUM
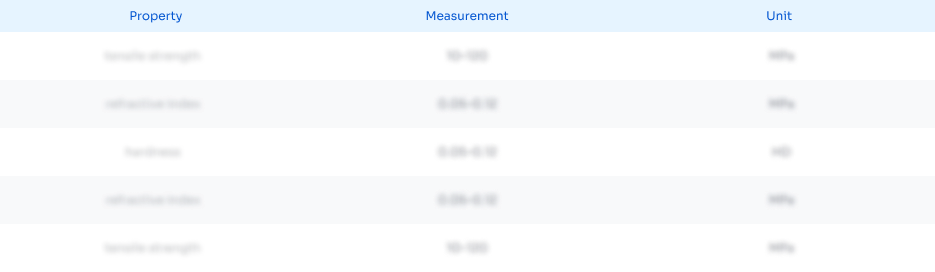
Abstract
Description
Claims
Application Information

- R&D Engineer
- R&D Manager
- IP Professional
- Industry Leading Data Capabilities
- Powerful AI technology
- Patent DNA Extraction
Browse by: Latest US Patents, China's latest patents, Technical Efficacy Thesaurus, Application Domain, Technology Topic, Popular Technical Reports.
© 2024 PatSnap. All rights reserved.Legal|Privacy policy|Modern Slavery Act Transparency Statement|Sitemap|About US| Contact US: help@patsnap.com