Reinforced wear-resistant automobile brake composite material and preparation method thereof
A composite material, automobile braking technology, applied in chemical instruments and methods, mechanical equipment, other chemical processes, etc., can solve the problems of high price, low wear rate, limited application, etc., to achieve low cost, low wear rate, anti- The effect of high thermal decay
- Summary
- Abstract
- Description
- Claims
- Application Information
AI Technical Summary
Problems solved by technology
Method used
Image
Examples
Embodiment 1
[0038] Weigh each raw material according to the weight of the formula, first add 90 parts of silicone modified phenolic resin into the kneader, heat to 60-70°C, and gradually add composite reinforcing fibers (55 parts of steel fiber and 55 parts of aramid fiber), Filler (55 parts of barite and 37 parts of graphite), 28 parts of nitrile rubber, 7.5 parts of hexamethylenetetramine, 4.8 parts of magnesium oxide, friction modifier (30 parts of rubber powder and 15 parts of copper powder), reducing Noise agent (synthetic calcium hydrosilicate and graphite formed particles) 32 parts and stearic acid 4.8 parts, and keep stirring, keep the mixing temperature at 50-60 ℃, stirring time 40-50 min, speed 280-300 r / min; then the above kneaded material is sent to a double-roller rolling machine for heating and kneading, the purpose is to further mix the material, the speed ratio of the two rolling rolls is 1:1.5, the front roll is 16 r / min, and the rear roll is 24 r / min, the temperature of...
Embodiment 2
[0040] Weigh each raw material according to the weight of the formula, first add 86 parts of silicone modified phenolic resin into the kneader, heat to 60-70°C, and gradually add composite reinforcing fiber (50 parts of steel fiber and 50 parts of carbon fiber), filler ( 50 parts of pyrophyllite and 30 parts of graphite), 30 parts of nitrile rubber, 6.2 parts of benzenesulfonyl chloride, 4.2 parts of calcium hydroxide, friction performance modifier (20 parts of tire powder and 10 parts of copper powder), noise reduction agent (synthetic silicon hydride Calcium acid and coke formed particles) 30 parts and 4.5 parts of zinc stearate, and keep stirring, keep the mixing temperature at 50-60 ° C, stirring time 30-40 min, rotating speed 290-310 r / min; then the above The kneaded material is sent to the double-roller rolling machine for heating and kneading, the purpose is to further mix the material, the speed ratio of the two rolling rolls is 1:1.4, the front roll is 15 r / min, the re...
Embodiment 3
[0042]Weigh each raw material according to the weight of the formula, first add 100 parts of silicone modified phenolic resin into the kneader, heat to 60-70°C, and gradually add composite reinforcing fibers (62 parts of steel fiber and 62 parts of aramid fiber), Filler (63 parts of talc and 42 parts of graphite), 25 parts of polyvinyl acetal, 8.5 parts of hexamethylenetetramine, 5.2 parts of magnesium oxide, friction modifier (50 parts of rubber powder and 25 parts of iron powder), Noise agent (synthetic calcium hydrosilicate and graphite formed particles) 35 parts and magnesium stearate 5.4 parts, and keep stirring, keep the mixing temperature at 50-60 ℃, stirring time 40-50 min, rotating speed 250-270 r / min; then the above-mentioned kneaded material is sent to a double-roller rolling machine for heating and kneading, the purpose is to further mix the material, the speed ratio of the two rolling rolls is 1:1.2, the front roll is 20 r / min, and the rear roll 24 r / min, the tem...
PUM
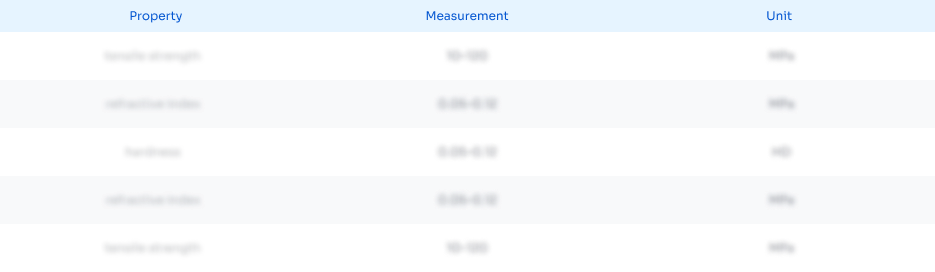
Abstract
Description
Claims
Application Information

- R&D
- Intellectual Property
- Life Sciences
- Materials
- Tech Scout
- Unparalleled Data Quality
- Higher Quality Content
- 60% Fewer Hallucinations
Browse by: Latest US Patents, China's latest patents, Technical Efficacy Thesaurus, Application Domain, Technology Topic, Popular Technical Reports.
© 2025 PatSnap. All rights reserved.Legal|Privacy policy|Modern Slavery Act Transparency Statement|Sitemap|About US| Contact US: help@patsnap.com