Laser doping technique used for improving adhesive force between metal electrode and crystalline silicon
A technology of laser doping and metal electrodes, which is applied in the field of laser doping technology, can solve problems affecting doping uniformity, battery performance, laser damage, etc., to meet industrial mass production, improve performance and stability, and improve The effect of conversion efficiency
- Summary
- Abstract
- Description
- Claims
- Application Information
AI Technical Summary
Problems solved by technology
Method used
Image
Examples
Embodiment 1
[0023] Such as figure 1 As shown, a laser doping process for improving the adhesion between metal electrodes and crystalline silicon includes the following steps:
[0024] (1) Silicon wafer texturing: selection, p-type monocrystalline silicon wafer as the base material and texturing;
[0025] (2) Boron diffusion: After the silicon wafer is cleaned, put the silicon wafer face to face into the diffusion furnace for boron diffusion;
[0026] (3) Growth mask: SiNx and SiOx laminated anti-reflection passivation film is used on the front of the silicon wafer, and aluminum paste is printed on the back of the silicon wafer and sintered;
[0027] (4) spin-coated phosphoric acid;
[0028] (5) Laser doping: The processing of silicon wafers is completed by using a focused linear spot optical system combined with a shaped pulse wave. The focused linear optical system includes a laser 1, an optical shaping system 2, a mirror 3, and a focusing lens 4. platform 7, the laser 1 is connected...
Embodiment 2
[0031] Such as figure 1 The focusing linear spot optical system used in the shown laser doping, the focusing linear optical system includes a laser 1, an optical shaping system 2, a mirror 3, a focusing lens 4, a workbench 7, and the laser 1 and Described optical shaping system 2 is connected, and described mirror 3 is arranged before described optical shaping system 2 and described focusing lens 4, and described workbench 7 is arranged at the below of focusing lens 4, and described The laser 1 emits the reshaped focused linear spot 5 through the optical shaping system 2, and the focused linear spot 5 is projected onto the focusing lens 4 through the mirror 3, and the focused linear spot 5 of the focusing lens 4 is placed on the workbench The silicon wafer 6 on 7 is processed, and the silicon wafer 6 moves with the workbench 7, and the focused linear light spot 5 acts on the surface of the silicon wafer 6. The ratio of the short axis and the long axis of the focused linear li...
PUM
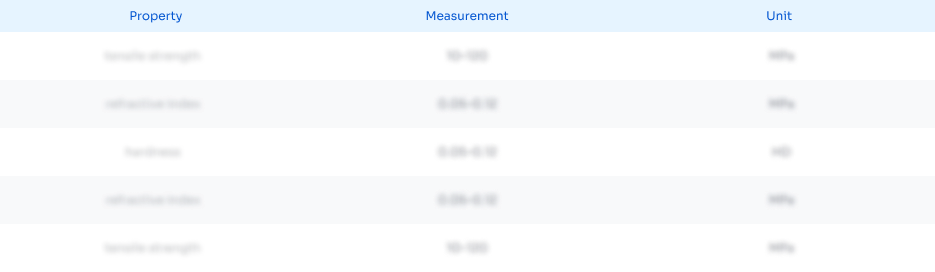
Abstract
Description
Claims
Application Information

- Generate Ideas
- Intellectual Property
- Life Sciences
- Materials
- Tech Scout
- Unparalleled Data Quality
- Higher Quality Content
- 60% Fewer Hallucinations
Browse by: Latest US Patents, China's latest patents, Technical Efficacy Thesaurus, Application Domain, Technology Topic, Popular Technical Reports.
© 2025 PatSnap. All rights reserved.Legal|Privacy policy|Modern Slavery Act Transparency Statement|Sitemap|About US| Contact US: help@patsnap.com