Method and system for molten slag granulation and sensible heat recovery
A sensible heat recovery and slag technology, applied in the direction of process efficiency improvement, etc., can solve the problems of high investment and operating costs, large water consumption, and reduce the effect of granulation, so as to reduce the volume and floor area, and achieve the level of The effect of short flight distance and reduced energy loss
- Summary
- Abstract
- Description
- Claims
- Application Information
AI Technical Summary
Problems solved by technology
Method used
Image
Examples
Embodiment Construction
[0038] The method for slag granulation and sensible heat recovery provided by the present invention and the slag granulation and sensible heat recovery system using the method will be described in detail below with reference to the accompanying drawings.
[0039] A method for slag granulation and sensible heat recovery provided by the invention comprises the following steps:
[0040] 1) Let the slag flow into the shell from the leakage bag to form multiple columnar slag flows, and the multiple columnar slag flows are arranged in at least one row, and the number of strands of each columnar slag flow is at least two;
[0041] 2) Install at least one nozzle in the shell with water cooling wall, pressurize the water to 1MPa ~ 400MPa with a high-pressure pump, and spray it from at least one nozzle to form a columnar high-speed water jet with a flow rate of at least 45m / s at the outlet of the nozzle;
[0042] 3) The high-speed water jet impacts the multiple columnar slag flows on th...
PUM
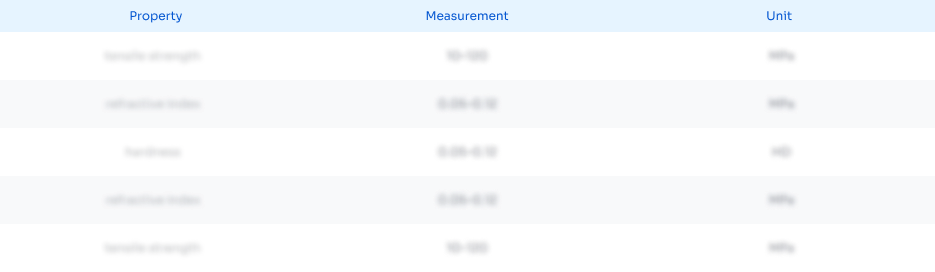
Abstract
Description
Claims
Application Information

- R&D
- Intellectual Property
- Life Sciences
- Materials
- Tech Scout
- Unparalleled Data Quality
- Higher Quality Content
- 60% Fewer Hallucinations
Browse by: Latest US Patents, China's latest patents, Technical Efficacy Thesaurus, Application Domain, Technology Topic, Popular Technical Reports.
© 2025 PatSnap. All rights reserved.Legal|Privacy policy|Modern Slavery Act Transparency Statement|Sitemap|About US| Contact US: help@patsnap.com