Optical-scale polyester film and preparation method thereof
A polyester film, optical-grade technology, applied in the field of optical base film for liquid crystal display, can solve the problems of inconvenient processing, increased fogging of polyester film, large friction coefficient of polyester film, etc. The effect of improving surface friction coefficient and light transmittance
- Summary
- Abstract
- Description
- Claims
- Application Information
AI Technical Summary
Problems solved by technology
Method used
Image
Examples
Embodiment 1
[0023] According to mass percentage, after adding 0.04% cross-linked polystyrene microspheres into 0.1% solvent and fully dissolving them, the cross-linked polystyrene microspheres are cross-linked polystyrene microspheres or cross-linked polystyrene microspheres. Type polymethylstyrene microspheres, the solvent is tetrahydrofuran or carbon tetrachloride, the particle size of cross-linked polystyrene microspheres is controlled at 5-8μm, and then add 3% polyacrylate resin and 0.5% Melamine and 0.05% colloidal silicon dioxide, colloidal silicon dioxide with a particle size of 50nm colloidal silicon dioxide and 100nm colloidal silicon dioxide, of which 50nm colloidal silicon dioxide and 100nm colloidal silicon dioxide are half each, stir well and then add Dilute with 96.31% deionized water to prepare a primer coating solution with a solid content of 3.59% for later use.
[0024]The present invention selects polyester chips with an intrinsic viscosity of 0.4-0.7dL / g, and the polye...
Embodiment 2
[0031] According to mass percentage, add 0.06% cross-linked polystyrene microspheres into 0.4% solvent to fully dissolve, and the cross-linked polystyrene microspheres are cross-linked polyethylstyrene microspheres or cross-linked polystyrene microspheres. Linked polypropylstyrene microspheres, the ratio of the two is not limited, the solvent is chloroform or dichloromethane, the particle size of cross-linked polystyrene microspheres is controlled at 6-10μm, and then 5% polyurethane is added Resin and melamine of 0.8% and colloidal silicon dioxide of 0.1%, colloidal silicon dioxide adopts particle diameter at 80nm colloidal silicon dioxide and 110nm colloidal silicon dioxide, wherein 80nm colloidal silicon dioxide and 110nm colloidal silicon dioxide are by mass parts The number ratio is 4:6, stir evenly and then add 93.64% deionized water to dilute to prepare a primer coating solution with a solid content of 5.96% for use.
[0032] The present invention selects polyester chips...
Embodiment 3
[0034] According to the mass percentage, add 0.08% cross-linked polystyrene microspheres to 0.2% solvent to fully dissolve, the cross-linked polystyrene microspheres are cross-linked polystyrene microspheres and cross-linked polystyrene microspheres A mixture of polypropylene styrene microspheres, the ratio of the two is not limited, the solvent is chloroform or dichloromethane, the particle size of the cross-linked polystyrene microspheres is controlled at 2-5 μm, and then 8% polystyrene is added Ester resin and 1.1% oxazoline and 0.12% colloidal silica, colloidal silica with a particle size of 60nm colloidal silica and 100nm colloidal silica, of which 60nm colloidal silica and 100nm colloidal silica According to the mass-number ratio of 6:4, stir evenly and then add 90.5% deionized water to dilute to prepare a primer coating solution with a solid content of 9.28% for use.
[0035] The present invention selects polyester chips with an intrinsic viscosity of 0.4-0.7dL / g, and t...
PUM
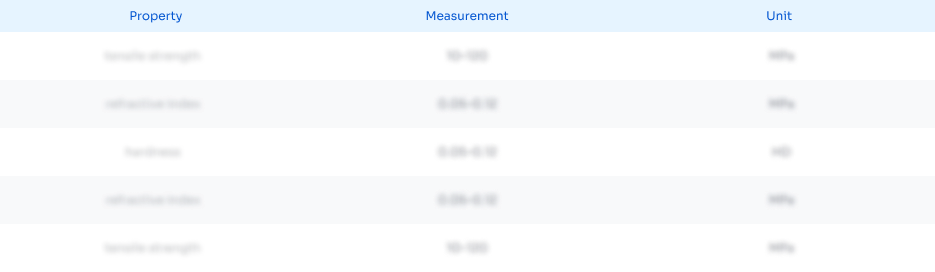
Abstract
Description
Claims
Application Information

- R&D
- Intellectual Property
- Life Sciences
- Materials
- Tech Scout
- Unparalleled Data Quality
- Higher Quality Content
- 60% Fewer Hallucinations
Browse by: Latest US Patents, China's latest patents, Technical Efficacy Thesaurus, Application Domain, Technology Topic, Popular Technical Reports.
© 2025 PatSnap. All rights reserved.Legal|Privacy policy|Modern Slavery Act Transparency Statement|Sitemap|About US| Contact US: help@patsnap.com