Extreme-pressure metalworking liquid and its preparation method
A metalworking fluid, extreme pressure technology, applied in the petroleum industry, lubricating compositions, etc., can solve the problems of difficult to meet the high-strength machining environment, short service life, poor lubricity, etc., and meet the requirements of low preparation conditions, The effect of improving the service life and the simple preparation method
- Summary
- Abstract
- Description
- Claims
- Application Information
AI Technical Summary
Problems solved by technology
Method used
Image
Examples
Embodiment 1
[0013] Weigh 40g of recovered transformer oil, then add 15g of chlorinated paraffin, 1g of RC4801, 4g of heavy alkylbenzene sulfonic acid, 3g of superamide, 2g of tall oil, 3g of fatty alcohol polyoxyethylene ether MOA-6, at room temperature Stir for 30 minutes, then add 1g benzisothiazolinone, 1g 3-iodo-2-propynyl butyl carbamate, 7g monoethanolamine borate, 2g triazine amino acid ester, 0.5g mercaptobenzothiazole, After stirring evenly, it becomes uniformly milky, then add 1g octadecanal fatty alcohol, 3g diethylene glycol butyl ether, stir for another 20 minutes, heat up to 50-60°C, add 5g triethanolamine, stir for about 30 minutes, and finally add 0.2% EDTA and 0.1g of organic silicon, the appearance of brown yellow transparent liquid, 3% cast iron rust prevention: 0 grade, pH = 9.47, pass the rust prevention of ferrous metals, no corrosion to copper parts, slight corrosion of national standard aluminum, put it for 3 days layered.
Embodiment 2
[0015] Weigh 35g of recovered transformer oil, then add 20g of chlorinated paraffin, 1g of RC4801, 3g of heavy alkylbenzenesulfonic acid, 3g of superamide, 2g of tall oil, 2.5g of fatty alcohol polyoxyethylene ether MOA-6, at room temperature Stir for 30 minutes, then add 1g benzisothiazolinone, 1g 3-iodo-2-propynyl butyl carbamate, 8g monoethanolamine borate, 2g triazine amino acid ester, 0.5g mercaptobenzothiazole After stirring evenly, it becomes uniform milky, then add 1.5g octadecyl fatty alcohol, 3g ethylene glycol monobutyl ether, stir for 20 minutes, raise the temperature to 50-60°C, add 3.5g triethanolamine, stir for about 30 minutes, and finally Add 0.2% EDTA and 0.1g organic silicon, the appearance is brownish-yellow transparent liquid, 3% cast iron scrap anti-rust: 0 grade, pH=9.32, pass the rust prevention for ferrous metals, no corrosion for copper parts, slight corrosion for national standard aluminum, Leave for 1 day to stratify.
Embodiment 3
[0017] Weigh 45.5g of recovered transformer oil, then add 20g of chlorinated paraffin, 1g of RC4801, 3g of heavy alkylbenzenesulfonic acid, 4g of superamide, 2g of tall oil, 5g of fatty alcohol polyoxyethylene ether MOA-6, at room temperature Stir for 30 minutes, then add 1g benzisothiazolinone, 1g 3-iodo-2-propynyl butyl carbamate, 9g monoethanolamine borate, 1.5g triazine amino acid ester, 1.0g mercaptobenzene Thiazole, after stirring evenly, it becomes uniform milk, then add 1.5g octadecyl fatty alcohol, 3g diethylene glycol butyl ether, stir for another 20 minutes, raise the temperature to 50-60°C, add 3.5g triethanolamine, stir for about 30 minutes, Finally, add 0.2% EDTA and 0.1g organic silicon, the appearance is brownish-yellow transparent liquid, 2.5% cast iron shavings Antirust: 0 grade, pH=9.51, pass the rust prevention for ferrous metals, no corrosion for copper parts, slight corrosion for national standard aluminum , placed for 3 days without delamination.
PUM
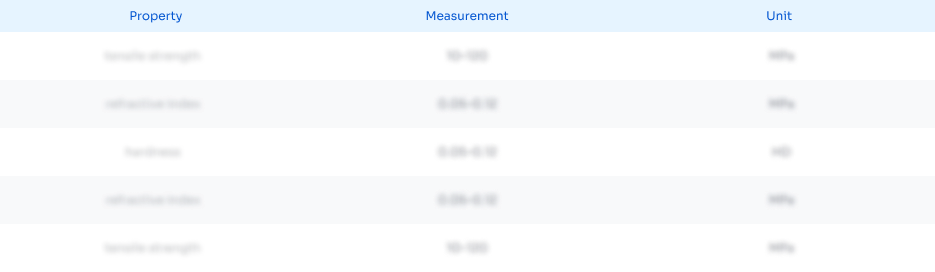
Abstract
Description
Claims
Application Information

- R&D
- Intellectual Property
- Life Sciences
- Materials
- Tech Scout
- Unparalleled Data Quality
- Higher Quality Content
- 60% Fewer Hallucinations
Browse by: Latest US Patents, China's latest patents, Technical Efficacy Thesaurus, Application Domain, Technology Topic, Popular Technical Reports.
© 2025 PatSnap. All rights reserved.Legal|Privacy policy|Modern Slavery Act Transparency Statement|Sitemap|About US| Contact US: help@patsnap.com