Method for recovering bismuth from bismuth slag
A bismuth slag, medium-high temperature technology is applied in the field of recycling bismuth to achieve the effects of reducing input, reducing operating procedures and avoiding hydrolysis
- Summary
- Abstract
- Description
- Claims
- Application Information
AI Technical Summary
Problems solved by technology
Method used
Image
Examples
example 1
[0062] Put in 1.058t of high silver and high bismuth anode slime (metal content: Bi: 637.76kg, Ag: 59.88kg, Pb: 163.88kg), liquid-solid ratio 5:1, industrial hydrochloric acid 2m 3 , keep the temperature at 60°C, stir and react for 3 hours, press filter to get the leach solution containing metal Bi: 609.85kg, Ag: 0.329kg, Pb: 1.67kg. The leached slag is 375.34kg, of which metal content: Bi: 26.93kg, Ag: 58.96kg, Pb: 162.73kg. Leaching rate: Bi: 95.62%, Ag: 0.55%, Pb: 1.02%;
[0063] The high bismuth leaching solution was replaced, the amount of reduced iron powder was 248kg, stirred at room temperature for 1 hour and filtered to obtain 639.23kg of bismuth sponge, of which the metal content: Bi: 599.24kg, Ag: 0.327kg, Pb: trace amount. Indicator replacement rate: Bi: 98.26%
[0064] Add 1000g of bismuth sponge, 100g of reduced coal, 30g of caustic soda, and 20g of silica, mix well and put them into a graphite crucible, keep the temperature in the crucible resistance furnace a...
example 2
[0066] Put in 10.5t of high-silver and high-bismuth anode slime. The control conditions for leaching are: liquid-solid ratio of 3:1, temperature control of 60-70°C, stirring and leaching time of 3 hours, and concentration of hydrochloric acid in the leaching solution of 6N. The bismuth leaching filtrate is extracted and replaced, and the amount of iron powder added is 45-50% of the total amount of bismuth in the leaching filtrate. The residual leaching liquid contained 2.62t of bismuth, the leaching slag contained 0.305t of bismuth, and 7.04t of bismuth sponge was produced, totaling 9.965t of bismuth metal. The leaching rate of Bi is 95%, the leaching rate of Ag is <1%, and the yield of leaching residue is 45%.
PUM
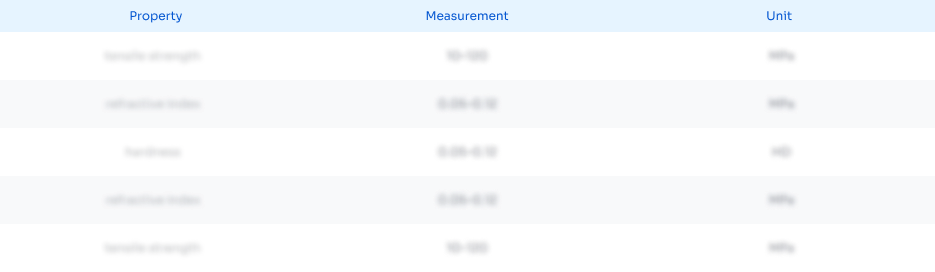
Abstract
Description
Claims
Application Information

- Generate Ideas
- Intellectual Property
- Life Sciences
- Materials
- Tech Scout
- Unparalleled Data Quality
- Higher Quality Content
- 60% Fewer Hallucinations
Browse by: Latest US Patents, China's latest patents, Technical Efficacy Thesaurus, Application Domain, Technology Topic, Popular Technical Reports.
© 2025 PatSnap. All rights reserved.Legal|Privacy policy|Modern Slavery Act Transparency Statement|Sitemap|About US| Contact US: help@patsnap.com