Method for producing trichlorosilane by utilizing photovoltaic crystalline silicon processing waste mortar
A photovoltaic crystalline silicon and trichlorosilane technology, applied in the directions of halogenated silanes, halogenated silicon compounds, etc., can solve the problems of waste of resources and pollution of the environment, and achieve the effect of realizing resource recycling, simplifying processing technology and reducing costs.
- Summary
- Abstract
- Description
- Claims
- Application Information
AI Technical Summary
Problems solved by technology
Method used
Image
Examples
Embodiment 1
[0018] As shown in the flow chart of the production of trichlorosilane by processing waste sand from photovoltaic crystal silicon: mixed with 10-40% PEG (polyethylene glycol), 15-30% SiC (cutting abrasive), and 10-1% iron Powder (cutting tool material), quaternary mixture system of 65-29% Si micropowder (crystalline silicon cutting debris)—waste mortar, in process 1 according to application number 201110101064.7 "New method for comprehensive treatment of waste mortar for processing crystalline silicon for photovoltaic cells 》Separate and recycle PEG and iron in waste mortar to obtain binary sand containing Si and SiC, with a mass content of SiC15%, particle size≤30um; Si84%, particle size≤10um; Fe≤0.3%, others≤0.7%, particle size ≤50um; the comprehensive particle size range is 1000-3000 mesh; fully dried after process 2 for later use.
[0019] Potassium chloride KCl and concentrated sulfuric acid H 2 SO 4 Put into the Mannheim reactor, carry out the 2KCl+H of step 3 2 SO 4...
Embodiment 2
[0023] As shown in the process flow chart of using photovoltaic crystal silicon to process waste sand to produce trichlorosilane: a quaternary mixture system mixed with PEG, iron powder, SiC micropowder, and Si micropowder—waste mortar, in process 1 according to the application number 201110101064.7 " New Method for Comprehensive Treatment of Waste Mortar from Crystalline Silicon Processing of Photovoltaic Cells "Separate and recycle PEG and iron in it to obtain a mass ratio of SiC 30%, particle size ≤ 30um; Si 69.4%, particle size ≤ 10um; Fe ≤ 0.3%, others ≤ 0.7% Particle size ≤ 50um; comprehensive particle size range 1000-3000 mesh; fully dried after process 2 for use.
[0024] Potassium chloride KCl and concentrated sulfuric acid H 2 SO 4 Put into the Mannheim reactor, carry out the 2KCl+H of step 3 2 SO 4 == K 2 SO 4 +2HCl↑reaction to generate potassium sulfate K2 SO 4 , to prepare potassium sulfate compound fertilizer; the by-product HCl↑ undergoes process 4 freezin...
PUM
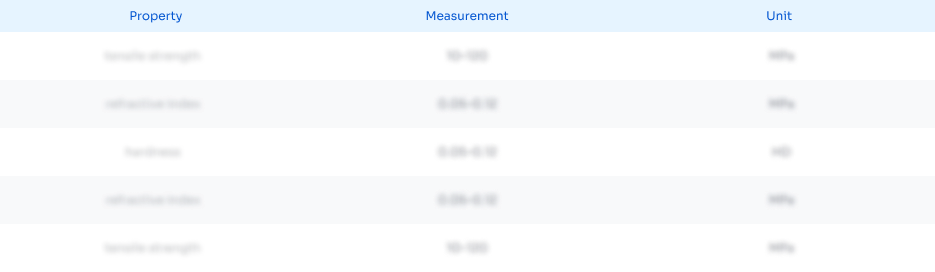
Abstract
Description
Claims
Application Information

- Generate Ideas
- Intellectual Property
- Life Sciences
- Materials
- Tech Scout
- Unparalleled Data Quality
- Higher Quality Content
- 60% Fewer Hallucinations
Browse by: Latest US Patents, China's latest patents, Technical Efficacy Thesaurus, Application Domain, Technology Topic, Popular Technical Reports.
© 2025 PatSnap. All rights reserved.Legal|Privacy policy|Modern Slavery Act Transparency Statement|Sitemap|About US| Contact US: help@patsnap.com