Selective emitter electrode solar battery manufacturing process combined with reactive ion etching (RIE)
A technology of reactive ion etching and solar cells, applied in sustainable manufacturing/processing, final product manufacturing, circuits, etc., can solve problems such as uneven diffusion, achieve increased light absorption, high photoelectric conversion efficiency, and improved short-wave response Effect
- Summary
- Abstract
- Description
- Claims
- Application Information
AI Technical Summary
Problems solved by technology
Method used
Image
Examples
Embodiment Construction
[0022] Such as figure 1 , 2 , 3, 4, 5 and 6, a reactive ion etching texturing combined with selective emitter solar cell manufacturing process, the method is: after surface pretreatment, the silicon wafer diffuses to form a diffusion layer 1, and then on the silicon wafer The surface is formed on the diffused layer 1 by reactive ion etching, the barrier layer 3 is printed, and the heavily doped region 4 and the lowly doped region 5 are formed after partial wet etching back, and finally the heavily doped region 4 The electrode 6 is printed and sintered to complete the preparation of the battery sheet.
[0023] Specific steps are as follows:
[0024] a) Surface damage layer treatment: using an acidic solution to remove the damage layer caused when slicing;
[0025] b) Diffusion junction: high doping concentration diffusion, diffusion square resistance <50 ohms;
[0026] c) Reactive ion etching: using a reactive ion etching system of fluoride ions, chloride ions and oxygen io...
PUM
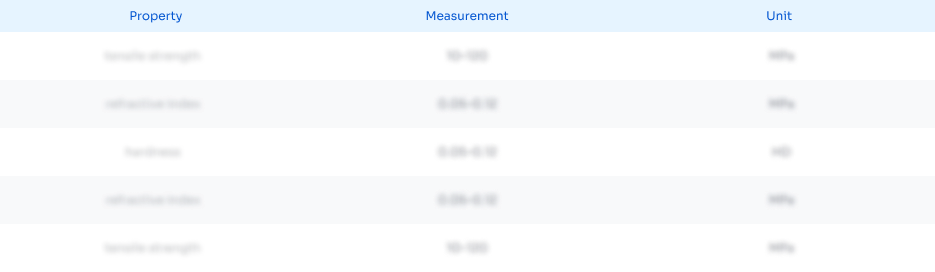
Abstract
Description
Claims
Application Information

- R&D
- Intellectual Property
- Life Sciences
- Materials
- Tech Scout
- Unparalleled Data Quality
- Higher Quality Content
- 60% Fewer Hallucinations
Browse by: Latest US Patents, China's latest patents, Technical Efficacy Thesaurus, Application Domain, Technology Topic, Popular Technical Reports.
© 2025 PatSnap. All rights reserved.Legal|Privacy policy|Modern Slavery Act Transparency Statement|Sitemap|About US| Contact US: help@patsnap.com