Zinc layer surface conversion film forming liquid, and application method thereof
A technology of converting into and film liquid, applied in the direction of metal material coating process, etc., to achieve the effect of stable performance, wide industrial application value, and excellent corrosion resistance
- Summary
- Abstract
- Description
- Claims
- Application Information
AI Technical Summary
Problems solved by technology
Method used
Examples
Embodiment 1
[0039] Preprocessing steps:
[0040] First, immerse the galvanized material in a NaOH solution with a temperature of 20°C and a mass content of 3% for 10 seconds to complete the alkali cleaning treatment to remove oxides on the surface of the galvanized layer;
[0041] Then, after the alkali-washed galvanized material is washed with water, it is immersed in a 3% nitric acid solution at room temperature for 3 to 5 seconds, and then rinsed with deionized water;
[0042] Preparation of zinc layer surface conversion film-forming solution:
[0043] Take 5.0 mmol of ceric sulfate, 40 mmol of sodium iodide, 9.0 mmol of trisodium phosphate, 0.5 mmol of sodium metavanadate, 250 mmol of sodium silicate, and 12 mmol of sodium fluorosilicate, respectively, and place them in 1000 ml of water, and adjust them with sulfuric acid to make them The pH of the film-forming solution on the surface of the zinc layer is 1.5, and the concentration of cerium ions is 5.0 mmol / L, the concentration of i...
Embodiment 2
[0047] The pretreatment steps are the same as in Example 1. Alkaline washing treatment uses 1% NaOH solution by mass content, and light treatment uses nitric acid solution with 5% mass content.
[0048] Preparation of zinc layer surface conversion film-forming solution:
[0049] Take 4.5 mmol of cerium nitrate, 84 mmol of potassium bromide, 6 mmol of sodium hexametaphosphate, 20 mmol of ammonium metavanadate, 4 mmol of ammonium silicate, and 250 mmol of ammonium fluorosilicate in 1000 ml of water, and adjust the surface of the zinc layer with sulfuric acid. The pH of the film-forming solution is 1.5, the concentration of cerium nitrate is 4.5 mmol / L, the concentration of potassium bromide is 84 mmol / L, the concentration of sodium hexametaphosphate is 6 mmol / L, the concentration of ammonium metavanadate is 20mmol / L, and the concentration of ammonium silicate 4 mmol / L, ammonium fluorosilicate 250 mmol / L zinc layer surface into a film liquid;
[0050] Conversion into film s...
Embodiment 3
[0053] The pretreatment steps are the same as in Example 1. Alkaline washing treatment uses 5% NaOH solution by mass content, and light treatment uses 1% nitric acid solution by mass content.
[0054] Preparation of zinc layer surface conversion film-forming solution:
[0055] Take 2.5 mmol of ceric sulfate, 40 mmol of sodium iodide, 3.2 mmol / L of sodium hexametaphosphate, 50 mmol of potassium metavanadate, 4 mmol of potassium silicate, and 4 mmol of potassium fluorosilicate in 1000ml of water, and adjust with sulfuric acid. The pH of the film-forming solution on the surface of the zinc layer is 2.0, and the concentration of ceric sulfate is 2.5 mmol / L, the concentration of sodium iodide is 40 mmol / L, the concentration of sodium hexametaphosphate is 3.2 mmol / L, and the concentration of potassium metavanadate is 50 mmol / L, potassium silicate 4 mmol / L, potassium fluorosilicate 4 mmol / L, the surface of the zinc layer is transformed into a film liquid;
[0056] Conversion into ...
PUM
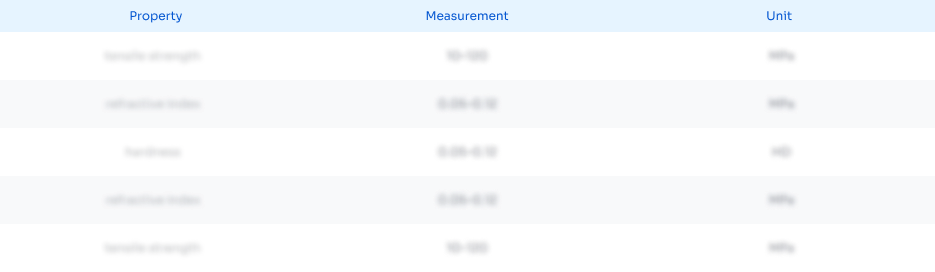
Abstract
Description
Claims
Application Information

- R&D
- Intellectual Property
- Life Sciences
- Materials
- Tech Scout
- Unparalleled Data Quality
- Higher Quality Content
- 60% Fewer Hallucinations
Browse by: Latest US Patents, China's latest patents, Technical Efficacy Thesaurus, Application Domain, Technology Topic, Popular Technical Reports.
© 2025 PatSnap. All rights reserved.Legal|Privacy policy|Modern Slavery Act Transparency Statement|Sitemap|About US| Contact US: help@patsnap.com