Polymeric functional additive used in coal combustion and preparation method thereof
A technology of functional additives and polymers, which is applied in the field of polymer functional additives and its preparation, can solve the problems of backward combustion technology, incomplete combustion, and low combustion efficiency, and achieve low cost of use, sufficient coal combustion, and reduced NOx emissions. Effect
- Summary
- Abstract
- Description
- Claims
- Application Information
AI Technical Summary
Problems solved by technology
Method used
Image
Examples
specific Embodiment 1
[0023] Functional polymer materials used in this example: polyethylene glycol monomethyl ether (EO=4~75): 30g, nonylphenol polyoxyethylene ether (EO=8~10): 10g, fatty alcohol polyoxyethylene Ether (EO=4~23): 10g; dispersion stabilizer: N-β-(aminoethyl)aminopropyltrimethoxysilane: 8 g; put it in the reaction kettle, raise the temperature to 70°C, slowly add the catalyst iso Cobalt octoate: 5g, lanthanum oxide: 5g, react for 3 hours while stirring; after grinding, homogenizing, filtering and separating processes, control the particle size of the emulsion below 0.1 micron, add co-surfactant dioctyl phthalate 17g, 15g p-nitrophenol, stirred to a homogeneous liquid, cooled to obtain a solution that is a polymer functional additive for coal combustion. This functional polymer additive is suitable for coals with a sulfur content of 0.5-1.5%, a volatile fraction of 20-35%, and a calorific value of 4500-5500Kcal / kg. Use a metering pump to spray 600ppm of coal weight on the surface of ...
specific Embodiment 2
[0025] The functional polymer materials used in this example: allyl polyoxyethylene ether (EO=6-23): 10g, fatty alcohol (4-16 carbon atoms) polyoxyethylene oxypropylene ether (EO=25-45, PO=8~17): 25g; dispersion stabilizer: 3-aminopropyltriethoxysilane: 15g; put in the reaction kettle, heat up to 100°C, slowly add catalyst aluminum acetylacetonate: 3g, nickel naphthenate : 5g, 7g of titanium dioxide, reacted for 2.5 hours while stirring; then through grinding, homogenization, filtration and separation process, control the particle size of the emulsion below 0.05 microns, and then add co-surfactant: methoxypolyethylene glycol: 15g , dibutyl phthalate: 5g, propylene glycol: 15g, stir evenly, and cool to obtain a solution that is a polymer functional additive for coal combustion. This functional polymer additive is suitable for coals with a sulfur content of 1.0-2.0%, a volatile fraction of 32-40%, and a calorific value of 3800-4200Kcal / kg. Use a metering pump to spray on the su...
specific Embodiment 3
[0026] The functional polymer material used in this example: polyethylene glycol monomethyl ether (EO=4~45): 55g; dispersion stabilizer: γ-methacryloxypropyltriethoxysilane: 10g, put In the reaction kettle, heat up to 120°C, slowly add the catalyst manganese naphthenate: 7g, titanium dioxide: 1g, tungsten oxide: 2g, and react for 5 hours while stirring; then go through grinding, homogenization, filtration and separation processes to control the emulsion The particle size is below 0.5 microns, and finally add co-surfactant: propylene glycol: 5g, dioctyl phthalate: 15g, p-nitrophenol: 5g, stir evenly, and cool to obtain a solution that is a polymer functional additive for coal combustion . This functional polymer additive is suitable for coals with a sulfur content of 1.0-2.0%, a volatile fraction of 5-12%, and a calorific value of 5000-6000Kcal / kg. Use a metering pump to drop 600ppm of the coal mass on the surface of the coal particles, grind it through a coal powder ball mill...
PUM
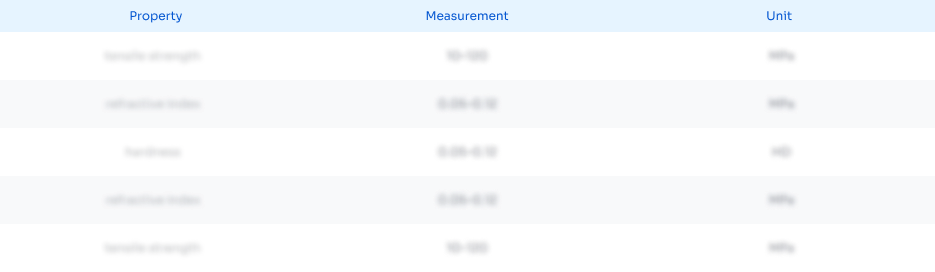
Abstract
Description
Claims
Application Information

- R&D
- Intellectual Property
- Life Sciences
- Materials
- Tech Scout
- Unparalleled Data Quality
- Higher Quality Content
- 60% Fewer Hallucinations
Browse by: Latest US Patents, China's latest patents, Technical Efficacy Thesaurus, Application Domain, Technology Topic, Popular Technical Reports.
© 2025 PatSnap. All rights reserved.Legal|Privacy policy|Modern Slavery Act Transparency Statement|Sitemap|About US| Contact US: help@patsnap.com