Spring steel and manufacturing and thermal treatment method thereof
A heat treatment method and spring steel technology, applied in temperature control, electric furnace, furnace, etc., can solve the problems of increased process and energy consumption, large thermal stress, low production efficiency, etc., achieve reduced process and energy consumption, and strong cold forming ability , the effect of high production efficiency
- Summary
- Abstract
- Description
- Claims
- Application Information
AI Technical Summary
Problems solved by technology
Method used
Image
Examples
Embodiment Construction
[0045] The present invention will be described in the following examples. It should be noted that these examples are only exemplary and do not constitute any limitation to the present invention.
[0046] Preparation of spring steel
[0047] The chemical components of the examples and comparative examples are shown in Table 1. The preparation process is as follows:
[0048] The first step is electric arc furnace smelting-ladle refining-continuous casting pouring
[0049] Initial smelting of molten steel in a 60-ton electric arc furnace; 60-ton ladle refining; continuous casting and pouring; 90×90mm produced 2 ~360×360mm 2 Qualified continuous casting slab with cross-section size:
[0050] (1) Primary smelting: low P, S scrap steel, cut ends and high-quality pig iron are used for the charge; low-carbon chromium, low-carbon manganese, etc. should be prepared for the alloy; reducing agent: calcium carbide, carbon powder, crystalline silicon, etc.; oxidation period: dilute slag To remove P,...
PUM
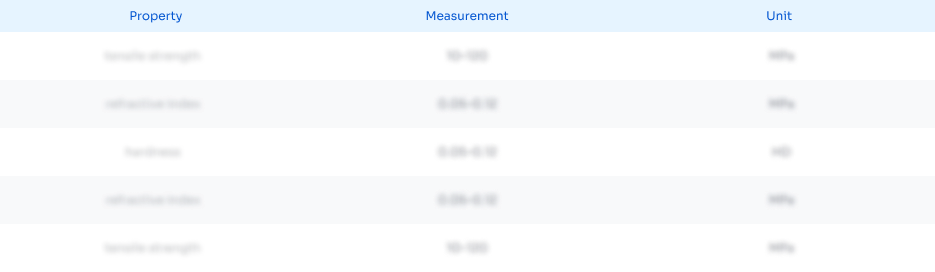
Abstract
Description
Claims
Application Information

- R&D
- Intellectual Property
- Life Sciences
- Materials
- Tech Scout
- Unparalleled Data Quality
- Higher Quality Content
- 60% Fewer Hallucinations
Browse by: Latest US Patents, China's latest patents, Technical Efficacy Thesaurus, Application Domain, Technology Topic, Popular Technical Reports.
© 2025 PatSnap. All rights reserved.Legal|Privacy policy|Modern Slavery Act Transparency Statement|Sitemap|About US| Contact US: help@patsnap.com