Novel method for preparing battery grade lithium carbonate by using tantalum niobium tailings lithium mica
A technology of tantalum-niobium tailings and lithium carbonate, which is applied in the direction of lithium carbonate;/acid carbonate, battery electrodes, circuits, etc., can solve the problems of incomplete utilization of resources, large energy waste, and high product cost. To achieve the effect of improving comprehensive utilization efficiency, improving recycling rate, and high equipment utilization rate
- Summary
- Abstract
- Description
- Claims
- Application Information
AI Technical Summary
Problems solved by technology
Method used
Examples
Embodiment 1
[0035] The concentration involved in the embodiments is the mass concentration. Now the process of extracting lithium or potassium carbonate from lepidolite is used to illustrate the new method for preparing battery-grade lithium carbonate from lepidolite.
[0036] The lepidolite ore selected in this embodiment adopts the tantalum-niobium-lithium ore produced in Yichun, and the main chemical components in the lepidolite powder are as follows:
[0037] Li 2 o
K 2 O+Na 2 o
Al 2 o 3
Si 2 o
Fe 2 o 3
Rb 2 o
Cs 2 o
F
4.2%
8.6%
22.9%
53.8%
0.2%
1.3%
0.2%
4.1%
[0038] The process steps of the present invention are as follows: filler leaching→evaporative fluorine removal→separation 1→slag removal→variable temperature separation 2→variable temperature separation 3→neutralization→separation 4→concentration→filtration→lithium separation.
[0039] Filler leaching: pulverize lepidoli...
PUM
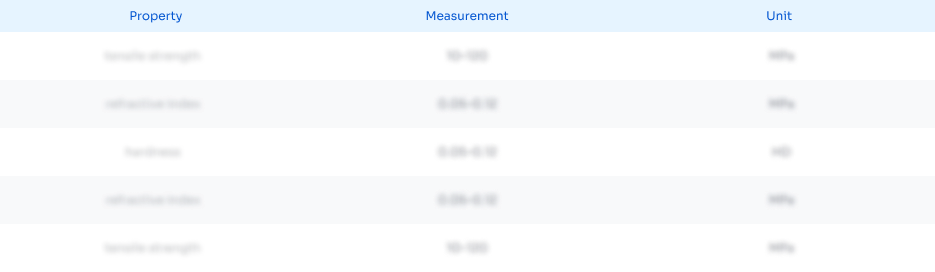
Abstract
Description
Claims
Application Information

- R&D
- Intellectual Property
- Life Sciences
- Materials
- Tech Scout
- Unparalleled Data Quality
- Higher Quality Content
- 60% Fewer Hallucinations
Browse by: Latest US Patents, China's latest patents, Technical Efficacy Thesaurus, Application Domain, Technology Topic, Popular Technical Reports.
© 2025 PatSnap. All rights reserved.Legal|Privacy policy|Modern Slavery Act Transparency Statement|Sitemap|About US| Contact US: help@patsnap.com