Process for reducing consumption of hydrochloric acid during chlorination distillation of germanium-containing raw material
A technology of chlorination distillation and process method, which is applied in the field of germanium recovery of germanium-containing raw materials, can solve the problems of increased consumption of quicklime, consumption of hydrochloric acid, and increased consumption of quicklime, and achieve the effect of reducing emissions and reducing consumption
- Summary
- Abstract
- Description
- Claims
- Application Information
AI Technical Summary
Problems solved by technology
Method used
Examples
Embodiment 1
[0030] Embodiment 1: in the pretreatment reactor of 500L, first add the water of 60L, then add 22.5kg sodium hydroxide, stir after sodium hydroxide is dissolved completely, drop into through being crushed to 15kg of germanium waste material more than 200 orders, The content of germanium is 92.51%, and the amount of germanium metal is 13.877kg. After stirring evenly, 90L of hydrogen peroxide with a mass fraction of 30% is introduced within 8 hours. After the oxidation reaction is 8 hours, the volume of the liquid is evaporated and concentrated to 50L; Transfer the final germanium raw material solution into a 500L distillation reactor, add 150kg of magnesium chloride, 250kg of industrial hydrochloric acid, open the steam and heat up to boiling, then carry out distillation. The distillation speed is 0.4-0.5L per minute, and the distillation time is 1.5h to obtain germanium tetrachloride. Metal 13.805kg, the yield from germanium waste to germanium tetrachloride is 99.49%. After th...
Embodiment 2
[0031]Embodiment 2: in the pretreatment reactor of 500L, first add the water of 120L, then add the sodium hydroxide of 24kg, after stirring makes sodium hydroxide dissolve completely, drop into 60kg of germanium concentrates through being pulverized to 200-400 purpose, The content of germanium is 8.48%, and the amount of germanium metal is 5.088kg. Stir evenly, heat to 80°C, and react for 1.5 hours. After heating to boiling and evaporating 60 liters of water, cool, and then transfer the solution into a 500L distillation reactor. Add 175kg of magnesium chloride, 250kg of industrial hydrochloric acid, turn on the steam and heat up to boiling, then carry out distillation. The distillation speed is controlled at 0.3-0.4 L / min, and the distillation time is 2.0h to obtain 4.987kg of germanium tetrachloride metal. From germanium waste to germanium tetrachloride The yield is 98.01%. After the distillation is over, after the reactor is cooled and warm, open the bottom valve of the reac...
Embodiment 3
[0032] Embodiment 3: in the pretreatment reactor of 500L, first add the water of 40L, then add the concentrated sulfuric acid that the mass percent concentration of 120kg is 98%, stir after making evenly dissolving completely, drop into germanium soot 120kg, germanium content is 3.16 %, the amount of germanium metal is 3.792kg, stir evenly, heat to 90-95°C, let it mature for 1.5h, after cooling, then transfer the solution into a 500L distillation reactor, add 200kg of magnesium chloride, 250kg of industrial hydrochloric acid, Turn on the steam and heat up to boiling, then carry out distillation, the distillation speed is 0.3-0.4L per minute, the distillation time is 2.0h, and 4.987kg of germanium tetrachloride metal is obtained, and the yield from germanium waste to germanium tetrachloride is 98.01%. After the distillation is over, after the reactor is cooled and warm, open the bottom valve of the reactor to release two-thirds of the distillation raffinate, leaving one-third of...
PUM
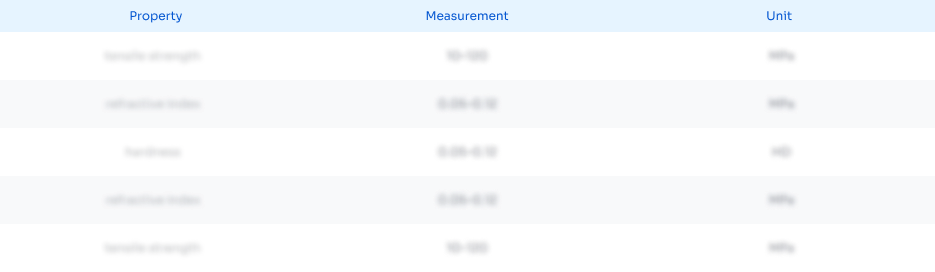
Abstract
Description
Claims
Application Information

- R&D Engineer
- R&D Manager
- IP Professional
- Industry Leading Data Capabilities
- Powerful AI technology
- Patent DNA Extraction
Browse by: Latest US Patents, China's latest patents, Technical Efficacy Thesaurus, Application Domain, Technology Topic, Popular Technical Reports.
© 2024 PatSnap. All rights reserved.Legal|Privacy policy|Modern Slavery Act Transparency Statement|Sitemap|About US| Contact US: help@patsnap.com