Method of preparing lamination dispersion strengthening platinum-base composite material
A composite material and dispersion strengthening technology, which is applied in the field of preparing layered dispersion strengthened platinum-based composite materials, can solve the problems of air bubbles at the laminated composite interface, increase production costs, and prolong the process flow, so as to improve the bonding strength and reduce the cost of precious metals. Loss, the effect of shortening the process flow
- Summary
- Abstract
- Description
- Claims
- Application Information
AI Technical Summary
Problems solved by technology
Method used
Image
Examples
Embodiment 1
[0022] Configure 3000g of raw materials according to the weight percentage of ZrO20.1, Rh 5, and Pt balance, and smelt under vacuum to form ZrO-containing 2 0.1% PtRh 5ZrO 2 0.1 alloy, poured into a flat ingot with a thickness of 8×70mm, after homogenization treatment at 800-1200°C / 2 hours, hot billeting, multi-pass cold rolling, intermediate heat treatment at 800-1200°C / 0.5 hours, finish rolling to thickness It is 0.03-0.08mm.
[0023] The PtRhZr alloy strip with a thickness of 0.03-0.08mm is internally oxidized for 10-100 hours in an oxidizing atmosphere of 0.5-2MPa at a temperature of 800-1300°C to form ZrO 2 Reinforced PtRh5 sheet semi-finished products.
[0024] ZrO with a thickness of 0.03-0.08mm 2 The strengthened PtRh5 thin strip is cut into small pieces with a growth of not less than 200mm and a width of not less than 180mm. According to the thickness and size requirements of products such as crucibles or bushings, a certain amount of small pieces are stacked toget...
Embodiment 2
[0027] The difference from Example 1 is:
[0028] With the composite ingot made in embodiment 1, vacuum tightness is 10 -2 ~10 -3 Pa, pre-press first, then heat up to 1100-1300°C, pressurize to 30-60MPa, hold the pressure for 30-60min, then cool to room temperature with the furnace, and then get the material for making crucible or bushing product thickness.
Embodiment 3
[0030] The difference from Example 1 is:
[0031] With the composite ingot made in embodiment 1, vacuum tightness is 10 -2 ~10 -3 Pa, pre-press first, then heat up to 1200-1300°C, pressurize to 20-30MPa, hold the pressure for 20-50min, then cool to room temperature with the furnace, and then get the material for making crucible or bushing product thickness.
PUM
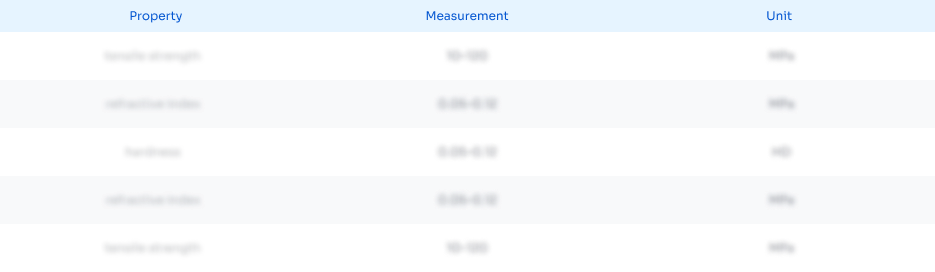
Abstract
Description
Claims
Application Information

- R&D
- Intellectual Property
- Life Sciences
- Materials
- Tech Scout
- Unparalleled Data Quality
- Higher Quality Content
- 60% Fewer Hallucinations
Browse by: Latest US Patents, China's latest patents, Technical Efficacy Thesaurus, Application Domain, Technology Topic, Popular Technical Reports.
© 2025 PatSnap. All rights reserved.Legal|Privacy policy|Modern Slavery Act Transparency Statement|Sitemap|About US| Contact US: help@patsnap.com