Method for preparing polyacrylate/nano-SiO2 compound coating agent by using reactive emulsifier
A reactive emulsifier, polyacrylate technology, applied in coating, application, small raw hide/large hide/leather/fur treatment, etc., can solve the problems of limiting the development space of polymer emulsions, environmental pollution, emulsion performance defects, etc. , to reduce adverse effects, strong water resistance, and improved performance
- Summary
- Abstract
- Description
- Claims
- Application Information
AI Technical Summary
Problems solved by technology
Method used
Examples
Embodiment 1
[0033] The three-necked flask was heated to 38° C. in a water bath, and 2 wt % of emulsifier 1-allyloxy-3-(4-nonylphenol)-2-propanol polyoxyethylene ether ammonium sulfate and 60 wt % of deionized water were added, Stir at a speed of 300 rpm for 20 minutes. After the emulsifier is uniformly dispersed, add 1 wt % tetraethylorthosilicate and 4 wt % silane coupling agent vinyltrimethoxysilane, and react at a constant temperature for 20 min. Add 1 / 5 mixed monomer of butyl acrylate and methyl methacrylate (the mixed monomer accounts for 25wt% of the total mass of the system, and the molar ratio of the two monomers is 3:2), raise the temperature to 70°C, and react for 30 minutes. Add the remaining mixed monomers and 0.5wt% ammonium persulfate aqueous solution dropwise respectively. After the dropwise addition, raise the temperature to 80°C and keep it warm for 2 hours; Composite finish.
Embodiment 2
[0035] The three-necked flask was heated to 40°C in a water bath, and 3 wt% of emulsifier 1-allyloxy-3-(4-nonylphenol)-2-propanol polyoxyethylene ether ammonium sulfate and 60 wt% of deionized water were added, Stir at 300rpm for 20min. After the emulsifier is uniformly dispersed, add 0.8wt% ethyl orthosilicate and 4wt% silane coupling agent tetramethyldivinyldisiloxane, and react at constant temperature for 20min. Add 1 / 5 mixed monomer of butyl acrylate and methyl methacrylate (the mixed monomer accounts for 26wt% of the total mass of the system, and the molar ratio of the two monomers is 2:1), raise the temperature to 72°C, and react for 30 minutes. Add the remaining mixed monomers and 0.6wt% potassium persulfate aqueous solution dropwise. After the dropwise addition, raise the temperature to 80°C and keep it warm for 2 hours; add sodium carbonate aqueous solution at room temperature to adjust the pH of the emulsion to about 7 to obtain a nanocomposite Finishing agent.
Embodiment 3
[0037] Heat the three-necked flask in a water bath to 42°C, add 3.5wt% emulsifier 1-allyloxy-3-(4-nonylphenol)-2-propanol polyoxyethylene ether ammonium sulfate and 62wt% deionized water , stirred at a speed of 300 rpm for 20 minutes, and after the emulsifier was uniformly dispersed, 1.5 wt % ethyl orthosilicate and 3.5 wt % silane coupling agent vinyltriethoxysilane were added, and the reaction was carried out at constant temperature for 20 min. Add 1 / 3 mixed monomer of butyl acrylate and methyl acrylate (the mixed monomer accounts for 27wt% of the total mass of the system, and the molar ratio of the two monomers is 2:1), raise the temperature to 75°C, react for 30min, and add dropwise After the remaining mixed monomers and 0.7wt% ammonium persulfate aqueous solution are added dropwise, the temperature is raised to 80°C, and the reaction is kept for 2 hours; sodium acetate aqueous solution is added at room temperature, and the pH of the emulsion is adjusted to about 7 to obtai...
PUM
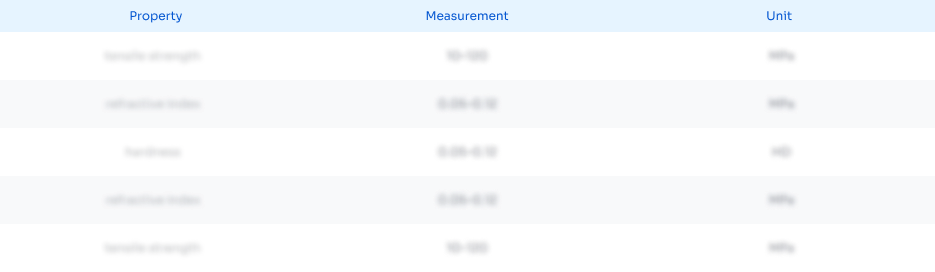
Abstract
Description
Claims
Application Information

- R&D Engineer
- R&D Manager
- IP Professional
- Industry Leading Data Capabilities
- Powerful AI technology
- Patent DNA Extraction
Browse by: Latest US Patents, China's latest patents, Technical Efficacy Thesaurus, Application Domain, Technology Topic, Popular Technical Reports.
© 2024 PatSnap. All rights reserved.Legal|Privacy policy|Modern Slavery Act Transparency Statement|Sitemap|About US| Contact US: help@patsnap.com