Method for improving corrosion resistance of copper by adding oxygen group alloy elements
An alloy element, anti-corrosion technology, applied in the field of anti-corrosion of metal surfaces, can solve the problems of high cost and high price, and achieve the effect of improving protection ability, reducing production cost and reducing packaging cost
- Summary
- Abstract
- Description
- Claims
- Application Information
AI Technical Summary
Problems solved by technology
Method used
Image
Examples
Embodiment 1
[0026] a. 0.5wt.% of S with a purity of 99.99wt.% is mixed with 99.5wt.% of pure Cu with a purity of 99.99wt.%.
[0027] b. Put the mixed material in the electric arc furnace, then vacuumize the furnace body, and feed high-purity argon gas, the flow rate of high-purity argon gas is 3000cm 3 / min, the air pressure is one atmosphere;
[0028] c. Start the electric arc furnace, set the discharge power to 2kW through glow discharge, heat up the copper and oxygen group alloy elements to 1133°C to melt, stop melting after 5 minutes of melting, cool down to room temperature, turn on the furnace, turn over the materials, and Turn the bottom one to the top, and turn the top one to the bottom. After turning over, close the furnace door, then vacuumize the furnace body, inject high-purity argon gas, and then re-melt and smelt. Repeat this process for 6 times to make Cu. -S alloy;
[0029] d. Put the prepared Cu-S alloy into a heating furnace with high-purity hydrogen and anneal it at a...
Embodiment 2
[0032] a. 0.1 wt.% of Se with a purity of 99.99 wt.% is mixed with 99.9 wt.% of pure Cu with a purity of 99.99 wt.%.
[0033] b. Place the mixed materials in the electric arc furnace respectively, then vacuumize the furnace body, and feed high-purity argon with a flow rate of 4000cm 3 / min, the air pressure is one atmosphere;
[0034] c. Start the electric arc furnace, set the discharge power to 5kW through glow discharge, heat up the copper and oxygen group alloy elements to 1150°C to melt, stop melting after 5 minutes, lower to room temperature, turn on the furnace, turn over the materials, and Turn the bottom one to the top, and turn the top one to the bottom. After turning over, close the furnace door, then vacuum the furnace body, inject high-purity argon gas, and then re-melt and smelt. Repeat this process for 7 times to make Cu. -Se alloy;
[0035] d. Put the prepared Cu-Se alloy into a heating furnace with high-purity hydrogen for annealing at a temperature of 600°C;...
Embodiment 3
[0038] a. Mix 0.05wt.% of Te with a purity of 99.99wt.% and 99.95wt.% of pure Cu with a purity of 99.99wt.%.
[0039] b. Place the mixed materials in the electric arc furnace respectively, then vacuumize the furnace body, and feed high-purity argon with a flow rate of 6000cm 3 / min, the air pressure is one atmosphere;
[0040]c. Start the electric arc furnace, set the discharge power to 10kW through glow discharge, and heat up the copper and oxygen group alloy elements to 1183°C to melt. After smelting for 5 minutes, stop the smelting, lower it to room temperature, turn on the furnace, turn over the materials, and put the original Turn the bottom one to the top, and turn the top one to the bottom. After turning over, close the furnace door, then vacuumize the furnace body, inject high-purity argon gas, and then re-melt and smelt. Repeated melting 8 times to make Cu -Te alloy;
[0041] d. Put the prepared Cu-Te alloy into a heating furnace with high-purity hydrogen for anneal...
PUM
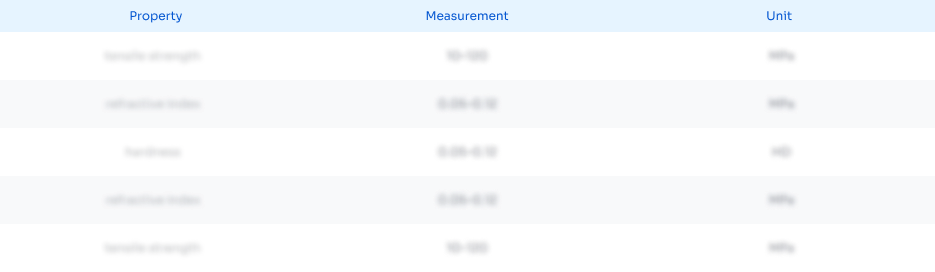
Abstract
Description
Claims
Application Information

- Generate Ideas
- Intellectual Property
- Life Sciences
- Materials
- Tech Scout
- Unparalleled Data Quality
- Higher Quality Content
- 60% Fewer Hallucinations
Browse by: Latest US Patents, China's latest patents, Technical Efficacy Thesaurus, Application Domain, Technology Topic, Popular Technical Reports.
© 2025 PatSnap. All rights reserved.Legal|Privacy policy|Modern Slavery Act Transparency Statement|Sitemap|About US| Contact US: help@patsnap.com