Device and method for controlling residual stress on surface of metal microstructure
A technology of metal microstructure and residual stress, applied in metal processing equipment, manufacturing tools, laser welding equipment, etc., can solve the problems of inability to achieve online detection and judgment of laser shot peening effect, affecting service life, etc., to improve mechanical properties , the effect of improving the service life
- Summary
- Abstract
- Description
- Claims
- Application Information
AI Technical Summary
Problems solved by technology
Method used
Image
Examples
Embodiment
[0023] Taking the aluminum sample as an example, place the aluminum sample on figure 1 In the measurement box 11, press the figure 1 The structure connects the laser micro-peening generation system, the measurement feedback system and the control system, such as figure 2 As shown, the implementation process is as follows:
[0024] [1] Step 100: Cover an energy absorbing layer (10 μm thick aluminum foil) and a constraining layer (1mm thick water curtain) on the surface of the aluminum film; complete sample preparation:
[0025][2] Step 101: Set and adjust the parameters of the output laser: the spot size is 25 μm, the pulse width is 6 ns, the energy is 0.8 mJ, the overlap rate of the spot is 50%, and the shot peening path is compiled according to the size of the treatment area.
[0026] [3] Step 102: start the numerical control system to control the laser peening head 9, and perform impact treatment on the surface of the micro-component with a straight line trajectory;
[0...
PUM
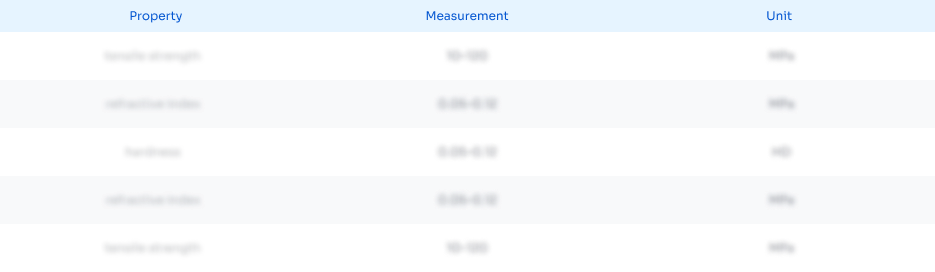
Abstract
Description
Claims
Application Information

- R&D Engineer
- R&D Manager
- IP Professional
- Industry Leading Data Capabilities
- Powerful AI technology
- Patent DNA Extraction
Browse by: Latest US Patents, China's latest patents, Technical Efficacy Thesaurus, Application Domain, Technology Topic, Popular Technical Reports.
© 2024 PatSnap. All rights reserved.Legal|Privacy policy|Modern Slavery Act Transparency Statement|Sitemap|About US| Contact US: help@patsnap.com