Low carbon high sulfur free-cutting steel production process
A technology of free-cutting steel and production process, which is applied to the improvement of process efficiency, furnace type, furnace, etc. It can solve the problems of steel breakout, poor fluidity, and difficulty in continuous casting production, so as to achieve simple process lines, reduce production accidents, highly operable effect
- Summary
- Abstract
- Description
- Claims
- Application Information
AI Technical Summary
Problems solved by technology
Method used
Image
Examples
Embodiment approach 1
[0038] (1) Consteel electric furnace oxygen blowing without power supply smelting technology is adopted, the ratio of molten iron to scrap steel is 1.0, the furnace door carbon oxygen lance and the furnace wall medium oxygen sub-lance alternately blow oxygen into the furnace for carbon-enriched smelting, and the chemical reaction of molten steel It can replace electric energy. The decarburization amount of molten steel during the smelting period is 0.30%, the C content at the end point of smelting is 0.08%, and the end point temperature is 1630°C.
[0039] (2) Tapping with steel and slag left at the bottom of the eccentric furnace (EBT), pre-deoxidation is carried out after the furnace, and when the tapping amount reaches 1 / 3, steel core aluminum and compound refining deoxidizer 0.5kg / t, silicon Iron, ferromanganese or silicomanganese alloy for alloying; when the tapping amount reaches 2 / 3, add slagging material to the ladle: dosage of active lime: 6kg / t.
[0040] (3) Refining...
Embodiment approach 2
[0043] (1) Consteel electric furnace oxygen blowing without power supply smelting technology is adopted. The ratio of hot charging molten iron to scrap steel in the electric furnace is 2.0. The furnace door carbon oxygen lance and the furnace wall medium oxygen sub-lance alternately blow oxygen into the furnace for carbon-rich smelting, and the chemical reaction of molten steel It can replace electric energy. The decarburization amount of molten steel during the smelting period is 0.45%, the C content at the end point of smelting is 0.10%, and the end point temperature is 1640°C.
[0044] (2) Tapping with steel and slag left at the bottom of the eccentric furnace (EBT), pre-deoxidation is carried out after the furnace, and when the tapping amount reaches 1 / 3, steel core aluminum and compound refining deoxidizer 0.5kg / t, silicon Iron, ferromanganese or silicon-manganese alloy for alloying; when the tapping amount reaches 2 / 3, add slagging material to the ladle: active lime dosag...
Embodiment approach 3
[0048] (1) Consteel electric furnace oxygen blowing without power supply smelting technology is adopted. The ratio of molten iron to scrap steel in electric furnace is 3.0. The furnace door carbon oxygen lance and the furnace wall medium oxygen sub-lance alternately blow oxygen into the furnace for carbon-enriched smelting, and the chemical reaction of molten steel It can replace electric energy. The decarburization amount of molten steel during the smelting period is 0.60%, the C content at the end point of smelting is 0.12%, and the end point temperature is 1650°C.
[0049] (2) Tapping with steel and slag left at the bottom of the eccentric furnace (EBT), pre-deoxidation is carried out after the furnace, and when the tapping amount reaches 1 / 3, steel core aluminum and compound refining deoxidizer 0.5kg / t, silicon Iron, ferromanganese or silicon-manganese alloy for alloying; when the tapping amount reaches 2 / 3, add slagging material to the ladle: active lime dosage: 8kg / t.
...
PUM
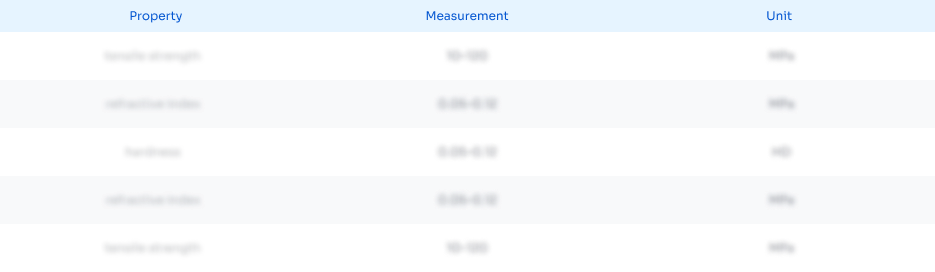
Abstract
Description
Claims
Application Information

- R&D
- Intellectual Property
- Life Sciences
- Materials
- Tech Scout
- Unparalleled Data Quality
- Higher Quality Content
- 60% Fewer Hallucinations
Browse by: Latest US Patents, China's latest patents, Technical Efficacy Thesaurus, Application Domain, Technology Topic, Popular Technical Reports.
© 2025 PatSnap. All rights reserved.Legal|Privacy policy|Modern Slavery Act Transparency Statement|Sitemap|About US| Contact US: help@patsnap.com