Method for preparing manganese-stabilized zirconia film
A technology for stabilizing zirconia and thin films, which is applied in the field of preparation of manganese-stabilized zirconia thin films, can solve problems such as the easy occurrence of second-phase oxides, eliminate the formation of amorphous layers and second-phase oxides, and achieve rapid preparation Effect
- Summary
- Abstract
- Description
- Claims
- Application Information
AI Technical Summary
Problems solved by technology
Method used
Examples
Embodiment 1
[0016] ZrO 2 powder and MnO 2 Powder is used as raw material, according to the Zr:Mn molar ratio of 3:1, weigh, mix, and grind for 2 hours, take it out after constant temperature treatment at 1400°C for 12-24 hours, then carefully grind for 2 hours, mix well, and weigh 5g in one portion , use a hard steel mold on the tablet press, and use a pressure of 10MPa to press into a disc-shaped sample with a diameter of 20mm and a thickness of 2mm. After the sample is placed in a corundum crucible, it is placed in a silicon carbon tube heating element tubular high-temperature furnace. In an argon atmosphere, it is sintered at 1400 ° C for 12-24 hours and then cooled to room temperature with the furnace to obtain Zr 0.75 mn 0.25 o 2 Stabilized zirconia blocks, which are ground to produce targets. Then, manganese-stabilized zirconia thin films were prepared by pulsed laser deposition technology. The laser used in the experiment was a COMPex205 KrF excimer laser produced by Lambda Phy...
Embodiment 2
[0018] ZrO 2 powder and MnO 2 Powder is used as raw material, according to the Zr:Mn molar ratio of 3:1, weigh, mix, and grind for 2 hours, take it out after constant temperature treatment at 1400°C for 12-24 hours, then carefully grind for 2 hours, mix well, and weigh 5g in one portion , use a hard steel mold on the tablet press, and use a pressure of 10MPa to press into a disc-shaped sample with a diameter of 20mm and a thickness of 2mm. After the sample is placed in a corundum crucible, it is placed in a silicon carbon tube heating element tubular high-temperature furnace. In an argon atmosphere, it is sintered at 1400 ° C for 12-24 hours and then cooled to room temperature with the furnace to obtain Zr 0.75 mn 0.25 o 2 Stabilized zirconia blocks, which are ground to produce targets. Then, manganese-stabilized zirconia thin films were prepared by pulsed laser deposition technology. The laser used in the experiment was a COMPex205 KrF excimer laser produced by Lambda Phy...
Embodiment 3
[0020] ZrO 2 powder and MnO 2 Powder is used as raw material, according to the Zr:Mn molar ratio of 3:1, weigh, mix, and grind for 2 hours, take it out after constant temperature treatment at 1400°C for 12-24 hours, then carefully grind for 2 hours, mix well, and weigh 5g in one portion , use a hard steel mold on the tablet press, and use a pressure of 10MPa to press into a disc-shaped sample with a diameter of 20mm and a thickness of 2mm. After the sample is placed in a corundum crucible, it is placed in a silicon carbon tube heating element tubular high-temperature furnace. In an argon atmosphere, it is sintered at 1400 ° C for 12-24 hours and then cooled to room temperature with the furnace to obtain Zr 0.75 mn 0.25 o 2 Stabilized zirconia blocks, which are ground to produce targets. Then, manganese-stabilized zirconia thin films were prepared by pulsed laser deposition technology. The laser used in the experiment was a COMPex205 KrF excimer laser produced by Lambda Phy...
PUM
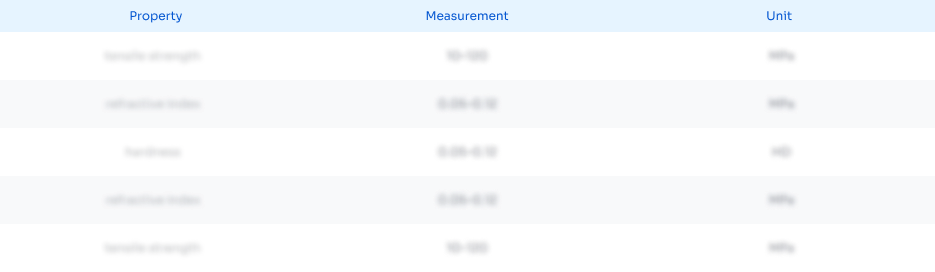
Abstract
Description
Claims
Application Information

- R&D
- Intellectual Property
- Life Sciences
- Materials
- Tech Scout
- Unparalleled Data Quality
- Higher Quality Content
- 60% Fewer Hallucinations
Browse by: Latest US Patents, China's latest patents, Technical Efficacy Thesaurus, Application Domain, Technology Topic, Popular Technical Reports.
© 2025 PatSnap. All rights reserved.Legal|Privacy policy|Modern Slavery Act Transparency Statement|Sitemap|About US| Contact US: help@patsnap.com