Method for preparing negative thermal expansion Mn3 (Cu0.5Ge0.5)N bulk material
A technology of cu0.5ge0.5 and negative thermal expansion, which is applied in the field of rapid preparation of Mn3N bulk materials, can solve the problems of small powder compacted sample size, long preparation cycle, and long reaction time, so as to shorten the preparation cycle and reaction time Short, reduced reaction time effect
- Summary
- Abstract
- Description
- Claims
- Application Information
AI Technical Summary
Problems solved by technology
Method used
Image
Examples
Embodiment 1
[0018] Mn powder and nitrogen are subjected to solid-gas reaction in a vacuum furnace, the nitrogen pressure in the furnace is 1.02MPa, the reaction temperature is 750°C, and the reaction time is 6 hours to obtain Mn 2 N 0.86 single phase powder. Will Mn 2 N 0.86 , Cu and Ge powders according to Mn 3 (Cu 0.5 Ge 0.5 ) The stoichiometric ratio of the N compound was weighed and mixed uniformly. The mixed powder was sintered under the protection of argon by spark plasma sintering. The process parameters were: sintering temperature 720°C, sintering pressure 60MPa, and heat preservation at sintering temperature for 30min.
[0019] The Mn that embodiment 1 prepares 3 (Cu 0.5 Ge 0.5 ) Phase analysis of N bulk material see figure 1 (a), negative thermal expansion performance test curve see figure 2 , and the characterization parameters of the negative thermal expansion properties of the material are shown in Table 1.
Embodiment 2
[0021] Mn powder and nitrogen were subjected to a solid-gas reaction in a vacuum furnace, the nitrogen pressure in the furnace was 1.04MPa, the reaction temperature was 800°C, and the reaction time was 5 hours to obtain Mn 2 N 0.86 single phase powder. Will Mn 2 N 0.86 , Cu and Ge powders according to Mn 3 (Cu 0.5 Ge 0.5 ) The stoichiometric ratio of N compounds was weighed and mixed evenly, and the mixed powder was sintered under the protection of argon by spark plasma sintering method. The process parameters were: sintering temperature 760°C, sintering pressure 50MPa, and heat preservation at sintering temperature for 20min.
[0022] The Mn that embodiment 2 prepares 3 (Cu 0.5 Ge 0.5 ) Phase analysis of N bulk material see figure 1 (b), negative thermal expansion performance test curve see image 3 , and the characterization parameters of the negative thermal expansion properties of the material are shown in Table 1.
Embodiment 3
[0024] Mn powder and nitrogen were subjected to a solid-gas reaction in a vacuum furnace. The nitrogen pressure in the furnace was 1.08 MPa, the reaction temperature was 1000 ° C, and the reaction time was 4 hours to obtain Mn 2 N 0.86 single phase powder. Will Mn 2 N 0.86 , Cu and Ge powders according to Mn 3 (Cu 0.5 Ge 0.5 ) The stoichiometric ratio of the N compound was weighed and mixed evenly, and the mixed powder was sintered under the protection of argon by spark plasma sintering. The process parameters were: sintering temperature 820°C, sintering pressure 30MPa, and heat preservation at sintering temperature for 5min.
[0025] The Mn that embodiment 3 prepares 3 (Cu 0.5 Ge 0.5 ) Phase analysis of N bulk material see figure 1 (c), negative thermal expansion performance test curve see Figure 4 , and the characterization parameters of the negative thermal expansion properties of the material are shown in Table 1.
[0026]
[0027] The Mn prepared in the emb...
PUM
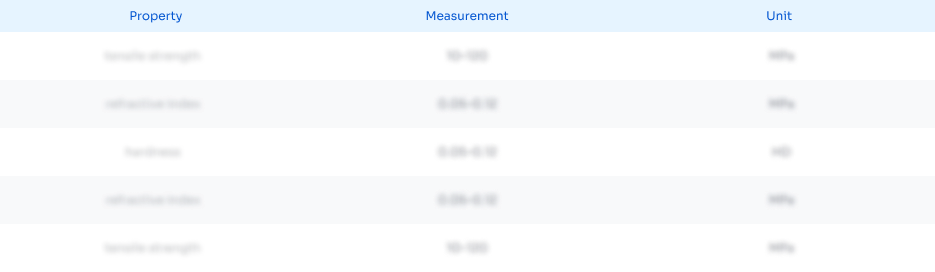
Abstract
Description
Claims
Application Information

- R&D
- Intellectual Property
- Life Sciences
- Materials
- Tech Scout
- Unparalleled Data Quality
- Higher Quality Content
- 60% Fewer Hallucinations
Browse by: Latest US Patents, China's latest patents, Technical Efficacy Thesaurus, Application Domain, Technology Topic, Popular Technical Reports.
© 2025 PatSnap. All rights reserved.Legal|Privacy policy|Modern Slavery Act Transparency Statement|Sitemap|About US| Contact US: help@patsnap.com