Method for separating molybdenum and nickel in molybdenum- and nickel-containing black shale
A black shale and separation method technology, applied in the field of metallurgy and chemical industry, can solve the problems of large amount of flue gas, high cost, and large consumption of reagents, and achieve the effects of avoiding pollution, process strengthening, and smelting process simplification
- Summary
- Abstract
- Description
- Claims
- Application Information
AI Technical Summary
Problems solved by technology
Method used
Examples
example 1
[0025] 1. Raw material: molybdenum content is 6.32%, nickel content is 3.05%, iron content is 8.27%, sulfur content is 21.58%, broken and crushed to 200 mesh (≥90%).
[0026] 2. One-stage oxygen pressure alkali leaching: add industrial soda ash with a mass percentage concentration of 50% and caustic soda with a mass percentage concentration of 10% for pulping, control the solid-liquid mass-volume ratio of 1:4, and pump it into the In the autoclave, industrial oxygen was introduced, the conversion temperature was controlled at 150° C., and the leaching reaction was carried out for 180 minutes under the condition of the pressure in the autoclave of 1.6 MPa. A section of molybdenum-containing leaching solution and a section of nickel-containing leaching residue are obtained by filtering, and a section of molybdenum-containing leaching solution is treated with molybdenum precipitation to obtain ammonium molybdate.
[0027] Molybdenum leaching rate: 90.37% Ammonium molybdate recovery...
example 2
[0032] 1. Raw material: molybdenum content is 5.92%, nickel content is 3.17%, iron content is 15.69%, sulfur content is 13.88%, broken and crushed to 200 mesh (≥90%).
[0033] 2. One-stage oxygen pressure alkali leaching: add industrial soda ash with a mass percentage concentration of 40% and caustic soda with a mass percentage concentration of 20% for pulping, control the solid-liquid mass volume ratio of 1:3, and pump it into the In the autoclave, industrial oxygen was introduced, the conversion temperature was controlled at 220° C., and the leaching reaction was carried out for 90 minutes under the condition of the inner pressure of the autoclave at 3.5 MPa. A section of molybdenum-containing leaching solution and a section of nickel-containing leaching residue are obtained by filtering, and a section of molybdenum-containing leaching solution is treated with molybdenum precipitation to obtain ammonium molybdate.
[0034] Molybdenum leaching rate: 94.25% Ammonium molybdate ...
example 3
[0039] 1. Raw materials: molybdenum content is 4.58%, nickel content is 2.79%, iron content is 17.37%, sulfur content is 23.0%, broken and crushed to 200 mesh (≥90%).
[0040] 2. One-stage oxygen pressure alkali leaching: add industrial soda ash with a mass percentage concentration of 30% and caustic soda with a mass percentage concentration of 20% for pulping, control the solid-liquid mass volume ratio of 1:2, and pump it into the In the autoclave, anhydrous air was passed through, the conversion temperature was controlled at 100° C., and the leaching reaction was carried out for 120 minutes under the condition of the pressure in the autoclave of 0.8 MPa. A section of molybdenum-containing leaching solution and a section of nickel-containing leaching residue are obtained by filtering, and a section of molybdenum-containing leaching solution is treated with molybdenum precipitation to obtain ammonium molybdate.
[0041] Molybdenum leaching rate: 75.17% Ammonium molybdate recov...
PUM
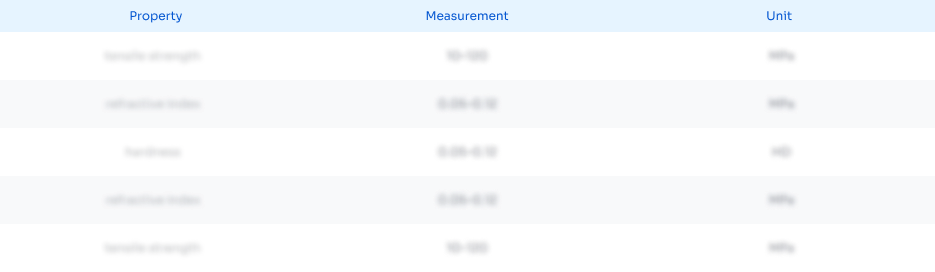
Abstract
Description
Claims
Application Information

- Generate Ideas
- Intellectual Property
- Life Sciences
- Materials
- Tech Scout
- Unparalleled Data Quality
- Higher Quality Content
- 60% Fewer Hallucinations
Browse by: Latest US Patents, China's latest patents, Technical Efficacy Thesaurus, Application Domain, Technology Topic, Popular Technical Reports.
© 2025 PatSnap. All rights reserved.Legal|Privacy policy|Modern Slavery Act Transparency Statement|Sitemap|About US| Contact US: help@patsnap.com