Method for producing steel for small square billet continuous casting high titanium alloy bonding wire
A small billet continuous casting and titanium alloy technology, applied in the field of steelmaking, can solve the problems of mold slag forming and leaking, nozzle blockage, mold mold mold slag agglomeration, etc., to reduce the risk of fish forming and nozzle blockage, reduce Inhalation of nitrogen gas and reduction of aluminum carryover effect
- Summary
- Abstract
- Description
- Claims
- Application Information
AI Technical Summary
Problems solved by technology
Method used
Image
Examples
Embodiment Construction
[0024] The present invention can be implemented in steel production plants with refining equipment outside the furnace. Tables 2 to 5 below list examples of key parameters of the production process when the third steelmaking plant of Shougang adopts the present invention to produce high-titanium alloy welding wire steel.
[0025] Table 2 Key parameters of converter process
[0026]
Heat End of the converter
Temperature (℃) End of converter
Point C (%) End of converter
point P (%) End of converter
point S (%) Amount of aluminum used for final deoxidation of converter
(Converted, kg / t) 8D00711 1689 0.05 0.008 0.021 0.98 8D00712 1710 0.02 0.012 0.027 1.28 8E00725 1690 0.05 0.012 0.027 1.35 8D00719 1710 0.05 0.011 0.030 0.71 8D00720 1690 0.05 0.006 0.026 0.73
[0027] Table 3 Key parameters of refining process
[0028]
Heat Refined to the station
ao(ppm) Refined to the station
Alu...
PUM
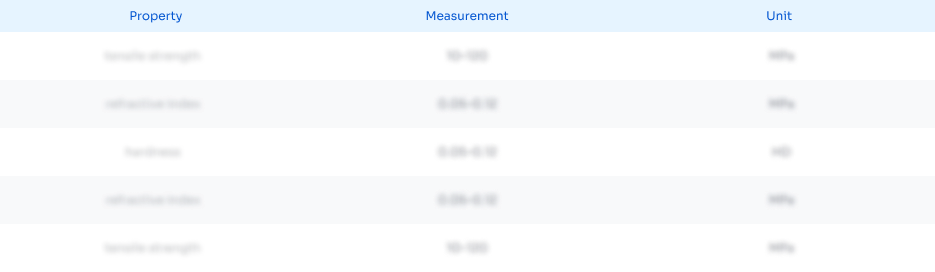
Abstract
Description
Claims
Application Information

- Generate Ideas
- Intellectual Property
- Life Sciences
- Materials
- Tech Scout
- Unparalleled Data Quality
- Higher Quality Content
- 60% Fewer Hallucinations
Browse by: Latest US Patents, China's latest patents, Technical Efficacy Thesaurus, Application Domain, Technology Topic, Popular Technical Reports.
© 2025 PatSnap. All rights reserved.Legal|Privacy policy|Modern Slavery Act Transparency Statement|Sitemap|About US| Contact US: help@patsnap.com