Heat processing technique for thinning TiAl-base alloy sheet interlayer spacing
A technology of lamellar spacing and base alloy, which is applied in the field of heat treatment process for thinning the lamellar spacing of TiAl-based alloys, which can solve the problems of low strength, poor room temperature plasticity and fracture toughness of TiAl-based alloys, etc.
- Summary
- Abstract
- Description
- Claims
- Application Information
AI Technical Summary
Problems solved by technology
Method used
Image
Examples
Embodiment 1
[0037] Example 1 The ingot of TiAl-based alloy (Ti-47Al-2Cr-2Nb) with full lamellar shape after casting is subjected to lamellar refinement treatment, and the specific process steps are as follows:
[0038] Step 1: Homogenize the Ti-47Al-2Cr-2Nb alloy at 900°C / 48h, and then perform hot isostatic pressing. The processing standard is 1280°C / 175MPa / 4h.
[0039] The second step: putting the Ti-47Al-2Cr-2Nb alloy treated in the first step into a vacuum heat treatment furnace for cyclic aging treatment in the α+γ dual-phase zone. The specific steps are:
[0040] (A) at a heating rate of 8.33×10 -2 ℃ / s to raise the temperature of the Ti-47Al-2Cr-2Nb alloy to 1180℃ in the first temperature zone of the α+γ dual-phase zone, and keep it warm for 5 minutes;
[0041] (B) At the heating rate v h =3.33×10 -2 °C / s raise the temperature of the Ti-47Al-2Cr-2Nb alloy treated in step (A) to 1280 °C in the second temperature zone of the α+γ dual-phase zone, and keep it for 15 minutes;
[004...
Embodiment 2
[0048] Example 2 The TiAl-based alloy (Ti-45Al-8.5Nb-0.1C) ingot formed by vacuum self-consumption solidification is subjected to lamellar refinement treatment. The specific process steps are:
[0049] Step 1: Homogenize the Ti-45Al-8.5Nb-0.1C alloy at 1050°C / 12h, and then perform hot isostatic pressing. The treatment standard is 1250°C / 200MPa / 3h.
[0050] The second step: putting the Ti-45Al-8.5Nb-0.1C alloy treated in the first step into a vacuum heat treatment furnace for cyclic aging treatment in the α+γ dual-phase zone. The specific steps are:
[0051] (A) at a heating rate of 8.33×10 -2 ℃ / s to raise the temperature of Ti-45Al-8.5Nb-0.1C alloy to 1200℃ in the first temperature zone of α+γ dual-phase zone, and keep it warm for 3min;
[0052] (B) At the heating rate v h =5.00×10 -2 °C / s raise the temperature of the Ti-45Al-8.5Nb-0.1C alloy treated in step (A) to 1300 °C in the second temperature zone, and keep it for 20 minutes;
[0053] (C) at cooling rate v c =2.0...
PUM
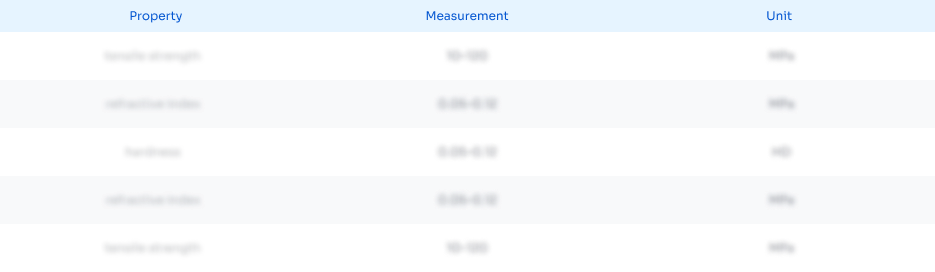
Abstract
Description
Claims
Application Information

- R&D Engineer
- R&D Manager
- IP Professional
- Industry Leading Data Capabilities
- Powerful AI technology
- Patent DNA Extraction
Browse by: Latest US Patents, China's latest patents, Technical Efficacy Thesaurus, Application Domain, Technology Topic, Popular Technical Reports.
© 2024 PatSnap. All rights reserved.Legal|Privacy policy|Modern Slavery Act Transparency Statement|Sitemap|About US| Contact US: help@patsnap.com