Semiconductor device and manufacturing method for the same
a semiconductor and manufacturing method technology, applied in semiconductor devices, semiconductor/solid-state device details, electrical devices, etc., can solve the problems of inability to reduce, easy to fracture wafers or semiconductor chips, and inability to reduce, so as to prevent cracks and breakage, and low elasticity
- Summary
- Abstract
- Description
- Claims
- Application Information
AI Technical Summary
Benefits of technology
Problems solved by technology
Method used
Image
Examples
embodiment 1
[0059]FIG. 1 is an illustrative wafer sectional view showing, in process order, a method for manufacturing a semiconductor device according to an embodiment of the invention. In the figure, a semiconductor substrate 1 (also referred to as “wafer 1”), processed by various device-forming and wiring processes and so on, is covered with a protection film (passivation film) (not shown) formed by a nitride film or the like in the area except for terminal regions (not shown) on a surface 1a as a surface on an active surface layer side. In the terminal regions, there are formed pads for electric connections of the circuits formed on the wafer to the external.
[0060] On the pads, projection electrodes 2 (posts) are formed in plurality, for example, of copper (Cu), gold (Au), solder, etc. by electroplating, for example, as shown in FIG. 1A. The projection electrode 2 has a height of approximately 50 μm with respect to the protection film surface, assuming a columnar form such as a circular cy...
PUM
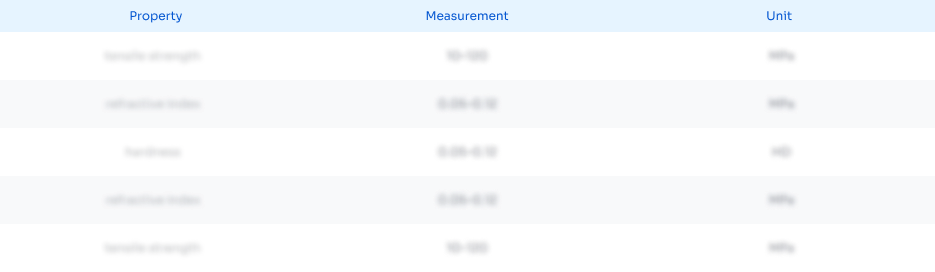
Abstract
Description
Claims
Application Information

- R&D
- Intellectual Property
- Life Sciences
- Materials
- Tech Scout
- Unparalleled Data Quality
- Higher Quality Content
- 60% Fewer Hallucinations
Browse by: Latest US Patents, China's latest patents, Technical Efficacy Thesaurus, Application Domain, Technology Topic, Popular Technical Reports.
© 2025 PatSnap. All rights reserved.Legal|Privacy policy|Modern Slavery Act Transparency Statement|Sitemap|About US| Contact US: help@patsnap.com