Semiconductor device and manufacturing method thereof
a technology of semiconductor devices and semiconductors, applied in semiconductor devices, semiconductor/solid-state device details, electrical apparatus, etc., can solve problems such as junction leakage current generation, various problems, and introduction of metal contamination into side surfaces, so as to prevent characteristic deterioration, reduce the concentration of contaminating metals, and prevent characteristic deterioration
- Summary
- Abstract
- Description
- Claims
- Application Information
AI Technical Summary
Benefits of technology
Problems solved by technology
Method used
Image
Examples
embodiment 1
[0031] Embodiments of the present invention are detailed using TSOP assembly of a semiconductor device shown in FIGS. 4 to 11 as examples. An is assembly flowchart of the present invention has additional processes of laser beam irradiation for the backside of a wafer and pressing a hot material to a chip's backside.
[0032] First of all, as shown in the assembly flowchart of FIG. 4, the surface of a silicon wafer, on which semiconductor devices have been fabricated in a normal method, was protected with a protection sheet, and the backside of the wafer was grinded. During this grinding process, the first rough grinding was performed at roughness of about #300 until the wafer thickness becomes about between 750 μm and 300 μm, and finishing grinding was then performed at roughness of about #2000 until the wafer thickness becomes 280 μm. Thereafter, the protection sheet on the surface is removed and washed with water in order to remove dusts attached to the grinded surface during the gr...
embodiment 2
[0051] Next, embodiment 2 in the present invention is detailed using FBGA assembly of a semiconductor device shown in FIGS. 12 to 14 as an example.
[0052] First of all, as shown in the assembly flowchart of FIG. 12, the surface of a silicon wafer on which semiconductor devices are fabricated in a normal method, was protected by a protection sheet, and the backside of the wafer was grinded in that state. During this grinding process, the first rough grinding is performed at roughness of about #300 until the thickness of the wafer becomes about 750 μm and 200 μm, and finishing grinding was then performed at roughness of about #2000 until the thickness of the wafer becomes 180 μm. Here, a comparison is made among a case of grinding using a normal backside grinder, and the following cases in the present invention: [0053] a case (d) where the backside is grinded with copper-contamination-free transfer system, grinding blade and grinding water; [0054] a case (e) where the final grinding i...
embodiment 3
[0060] Next, embodiment 3 of the present invention is detailed. In this Example, the gettering layer described in embodiment 1 was formed by a plasma treatment.
[0061] In the flowchart of FIG. 15, similarly to embodiment 1, a first gettering layer was formed on the backside of a wafer by a first plasma treatment after backside of the wafer was grinded, and then a second gettering layer was formed by a second plasma treatment after the wafer is diced. Both the first and second plasma treatments are carried out in a plasma atmosphere containing an impurity. These plasma treatments were performed, for example, using a plasma device, with plasma power of 2 KW, at substrate temperature of 150 degrees centigrade, using diluent gas containing oxygen as an impurity, at pressure of 1 Torr, and for treatment time of 60 seconds. Processes of backside grinding, dicing, bonding chips to LOC tape, wire bonding, and resin sealing are the same as those of embodiment 1 and descriptions thereof are t...
PUM
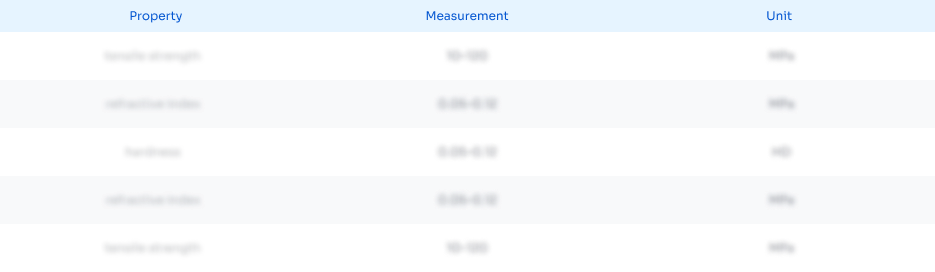
Abstract
Description
Claims
Application Information

- R&D
- Intellectual Property
- Life Sciences
- Materials
- Tech Scout
- Unparalleled Data Quality
- Higher Quality Content
- 60% Fewer Hallucinations
Browse by: Latest US Patents, China's latest patents, Technical Efficacy Thesaurus, Application Domain, Technology Topic, Popular Technical Reports.
© 2025 PatSnap. All rights reserved.Legal|Privacy policy|Modern Slavery Act Transparency Statement|Sitemap|About US| Contact US: help@patsnap.com