Ceramic electronic parts and its making method
A technology of electronic components and manufacturing methods, applied in the direction of fixed capacitor parts, electrical components, resistance terminals/electrodes, etc., can solve the problems of damaging the reliability of electronic components, complex manufacturing processes, low productivity, etc., and achieve wear resistance Strong, prevents the intrusion of the plating solution, and has the effect of small characteristic deviation
- Summary
- Abstract
- Description
- Claims
- Application Information
AI Technical Summary
Problems solved by technology
Method used
Image
Examples
Embodiment 1
[0044] As the external electrode, a ceramic green body for a multilayer ceramic capacitor in which a Cu bottom electrode is formed is prepared. After sintering the bottom electrode, prepare a water repellent for water repellent treatment. As a water repellent treatment agent, for methyl ethyl ketone as an organic solvent, 30g / L of Ra-(CH 2 )-Si-(O-Rb) 3 . Here, Ra is a perfluoro group, and Rb is an amino group. The ceramic green body forming the bottom electrode was immersed in the water-repellent treatment agent for 2 minutes, the liquid was removed, and after air-drying, Ni plating and Sn plating were sequentially performed to fabricate a multilayer ceramic capacitor.
[0045] For the obtained multilayer ceramic capacitor, 4WV was applied to a thermostatic bath at a temperature of 85°C and a humidity of 85% for the formation state of the internal plating film of the external electrode of the cross-sectional structure, the solderability, and the humidity of 85%, and the number of...
Embodiment 2
[0050] As in Example 1, the multilayer ceramic capacitor formed by immersing the bottom electrode in the water repellent treatment agent was treated with a ceramic green body for 2 minutes, the liquid was removed, and it was air-dried. Then, the ceramic green body is put into the furnace and heat-treated at 100-120°C for 30 minutes. As a comparative example, as in Example 1, no heat treatment was performed, and a ceramic green body to which the water repellent treatment agent was adsorbed was prepared. Then, assuming that the hand-operated water repellent treatment agent in the mass production process is peeled off, the ceramic green bodies are treated with a roller at 60 rpmj and 30 minutes at 2L perimeter. In addition, Ni plating and Sn plating are sequentially performed on the bottom electrode to manufacture a multilayer ceramic capacitor. Regarding these multilayer ceramic capacitors, as in Example 1, the results of plating penetration into the electrodes, solderability, and w...
Embodiment 3
[0054] Prepare a ceramic green body for chip inductors made of porous ferrite material as the ceramic green body. Using this ceramic green body, as in Example 1, the external electrodes were subjected to water-repellent treatment, Ni and Sn were plated in sequence, and terminal electrodes were formed on both ends of the ceramic green body. As a comparative example, a water-repellent agent using a carboxyl group as an adsorption group without water-repellent treatment was produced, and a sample of resin immersion was performed. Then, in the same manner as in Example 1, Table 3 shows the results of the plating penetration into the electrode, solderability, and moisture resistance load tests.
[0055] this invention
[0056] It is understood from Table 3 that the water-repellent treatment of the present invention does not penetrate into the electroplating in the electrode, the solderability is also good, and even in the humidity resistance load test, no deterioration of ...
PUM
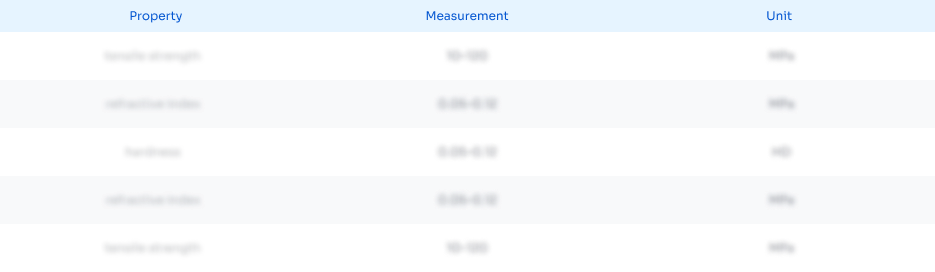
Abstract
Description
Claims
Application Information

- R&D
- Intellectual Property
- Life Sciences
- Materials
- Tech Scout
- Unparalleled Data Quality
- Higher Quality Content
- 60% Fewer Hallucinations
Browse by: Latest US Patents, China's latest patents, Technical Efficacy Thesaurus, Application Domain, Technology Topic, Popular Technical Reports.
© 2025 PatSnap. All rights reserved.Legal|Privacy policy|Modern Slavery Act Transparency Statement|Sitemap|About US| Contact US: help@patsnap.com