Preparation method of carbon-cladded magnetic metal nanometer material
A magnetic metal nano and carbon-coated technology, which is applied in the manufacture of inductors/transformers/magnets, electrical components, circuits, etc., can solve problems such as difficulty in large-scale production, high preparation temperature, and complex equipment, and achieve easy control of reaction parameters , low energy consumption, low temperature effect
- Summary
- Abstract
- Description
- Claims
- Application Information
AI Technical Summary
Problems solved by technology
Method used
Image
Examples
Embodiment 1
[0021] Under argon protection, 1.9568g CoCl 2 ·6H 2 O is completely dissolved in 20mL of absolute ethanol, and a reducing agent is added while stirring, and the reducing agent is composed of 85% weight concentration of NH 2 -NH 2 ·H 2 O aqueous solution 12mL and 2.0382g NaOH composition. After reacting at 35°C for 30 minutes, the obtained product was centrifuged and washed twice with water and ethanol in sequence to obtain 340 mg of dendritic metal cobalt.
[0022] 40 mg of the obtained cobalt metal was placed in 40 mL of 0.13 M aqueous glucose solution. Sonicate for 15 minutes and place the mixture in a polytetrafluoroethylene reactor. React at 160°C for 16 hours. Cool naturally at room temperature, centrifuge, wash with water and acetone twice in sequence, and dry in vacuum at room temperature. The carbon-coated dendritic cobalt material can be obtained, and the thickness of the carbon coating is about 250 nanometers.
Embodiment 2
[0024] Take 160 mg of the dendritic metal cobalt obtained in Example 1 and place it in 40 mL of 0.13 M glucose deoxygenated aqueous solution. After ultrasonication for 15 minutes, place the mixture in a polytetrafluoroethylene reactor and react at 180° C. for 16 hours. Cool, centrifuge, wash with water and acetone in turn, and dry under vacuum at room temperature. A carbon-coated dendritic cobalt material can be obtained, and the thickness of the carbon coating is about 100 nanometers.
[0025] In Examples 1 and 2, different carbon coating thicknesses can be obtained by controlling the weights of glucose and metal cobalt.
Embodiment 3
[0027] Under argon protection, 0.1396g FeSO 4 ·7H 2 O and 0.1492g NiSO 4 ·6H 2 O was completely dissolved in 10 mL of water, then 1.3601 g of polyethylene glycol (Mw=20000) and 0.5 mL of cyclohexane were added, ultrasonicated at room temperature for 80 minutes, then the mixture was heated to 78 °C, and a reducing agent was added. Consisting of 85% by weight NH 2 -NH 2 ·H 2 O aqueous solution 5mL and 1.0352g NaOH, reacted for 30 minutes to obtain a black sample, centrifuged, washed with water and ethanol twice to obtain 50 mg of iron-nickel alloy nanoparticles with a diameter of about 35 nanometers.
[0028] 19.6 mg of the obtained iron-nickel alloy nanoparticles were placed in 38 mL of deoxygenated water, and then dissolved in 3.0159 g of glucose. After ultrasonication for 15 minutes, the mixture was placed in a polytetrafluoroethylene reactor and reacted at 170° C. for 3.5 hours. Cool naturally at room temperature, centrifuge, wash with water and acetone twice in sequen...
PUM
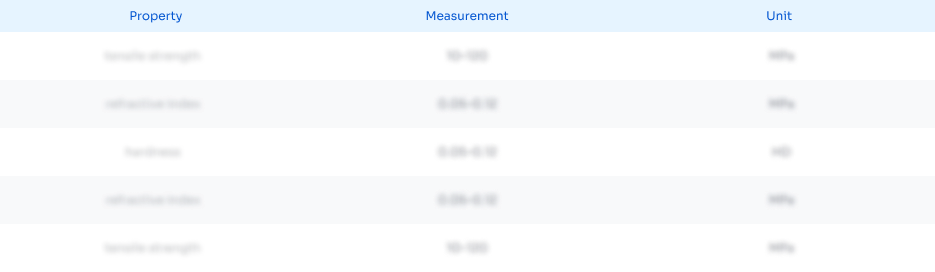
Abstract
Description
Claims
Application Information

- R&D Engineer
- R&D Manager
- IP Professional
- Industry Leading Data Capabilities
- Powerful AI technology
- Patent DNA Extraction
Browse by: Latest US Patents, China's latest patents, Technical Efficacy Thesaurus, Application Domain, Technology Topic, Popular Technical Reports.
© 2024 PatSnap. All rights reserved.Legal|Privacy policy|Modern Slavery Act Transparency Statement|Sitemap|About US| Contact US: help@patsnap.com