Method for preparing nanometer zinc oxide thin film using high temperature oxidation
A technology of nano-zinc oxide and high-temperature oxidation, which is applied in the direction of solid-state diffusion coating, vacuum evaporation coating, coating, etc., can solve the problems of expensive equipment and application limitations, and achieve simple and easy preparation process, convenient operation, and avoid The effect of forming oxygen vacancies and zinc interstitial
- Summary
- Abstract
- Description
- Claims
- Application Information
AI Technical Summary
Problems solved by technology
Method used
Image
Examples
example 1
[0018] Using electron beam evaporation technology, the experimental equipment is GDM-450 vacuum coating machine. Put the bulk zinc sulfide with a purity of 99.9% into the crucible, and put the substrate in the fixture after ultrasonic cleaning. Close the vacuum chamber and each pumping valve, and start vacuuming. Heat the substrate to 250°C and make the vacuum degree reach 2×10 -3 Pa. Turn on the high-voltage power supply, pre-melt the bulk zinc sulfide material in the crucible, and stabilize the air pressure in the vacuum chamber at 3.0×10 -3 Pa. Remove the movable baffle and begin to deposit the zinc sulfide film. Adjust the evaporation current and voltage to keep the electron beam current at 20mA. The evaporation process is controlled by the minimax optical control method until the desired film thickness is deposited. Then move the zinc sulfide thin film prepared by electron beam evaporation into a muffle furnace, and oxidize and anneal it in an environment of 700° C....
example 2
[0020] Using electron beam evaporation technology, the experimental equipment is GDM-450 vacuum coating machine. Put the bulk zinc sulfide with a purity of 99.9% into the crucible, and put the substrate in the fixture after ultrasonic cleaning. Close the vacuum chamber and each pumping valve, and start vacuuming. The substrate is heated to 200°C, and the vacuum degree reaches 2×10 -3 Pa. Turn on the high-voltage power supply, pre-melt the bulk zinc sulfide material in the crucible, and stabilize the air pressure in the vacuum chamber at 3.5×10 -3 Pa. Remove the movable baffle and begin to deposit the zinc sulfide film. Adjust the evaporation current and voltage to keep the electron beam current at 20mA. The evaporation process is controlled by the minimax optical control method until the desired film thickness is deposited. Then move the zinc sulfide thin film prepared by electron beam evaporation into a muffle furnace, and oxidize and anneal in an environment of 900° C....
Embodiment 3
[0022] Using electron beam evaporation technology, the experimental equipment is GDM-450 vacuum coating machine. Put the bulk zinc sulfide with a purity of 99.9% into the crucible, and put the substrate in the fixture after ultrasonic cleaning. Close the vacuum chamber and each pumping valve, and start vacuuming. Heat the substrate to 180°C and make the vacuum degree reach 2×10 -3 Pa. Turn on the high-voltage power supply, pre-melt the bulk zinc sulfide material in the crucible, and stabilize the air pressure in the vacuum chamber at 5×10 -3 Pa. Remove the movable baffle and begin to deposit the zinc sulfide film. Adjust the evaporation current and voltage to keep the electron beam current at 20mA. The evaporation process is controlled by the minimax optical control method until the desired film thickness is deposited. Then move the zinc sulfide thin film prepared by electron beam evaporation into a muffle furnace, and oxidize and anneal in an environment of 400° C. for ...
PUM
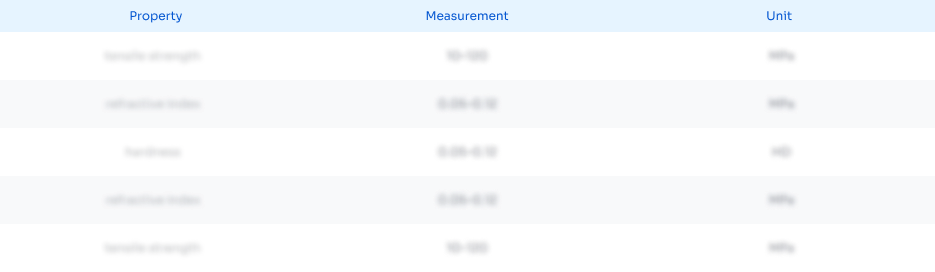
Abstract
Description
Claims
Application Information

- R&D Engineer
- R&D Manager
- IP Professional
- Industry Leading Data Capabilities
- Powerful AI technology
- Patent DNA Extraction
Browse by: Latest US Patents, China's latest patents, Technical Efficacy Thesaurus, Application Domain, Technology Topic, Popular Technical Reports.
© 2024 PatSnap. All rights reserved.Legal|Privacy policy|Modern Slavery Act Transparency Statement|Sitemap|About US| Contact US: help@patsnap.com