Fluorocarbon coating liquid, fluorocarbon coating and solar backboard
A technology of solar back sheet and fluorocarbon coating, applied in the field of solar back sheet, can solve the problem of poor heat resistance of transparent fluorocarbon coating, and achieves satisfactory heat resistance and outdoor use effect, good stability, and satisfactory packaging strength Effect
- Summary
- Abstract
- Description
- Claims
- Application Information
AI Technical Summary
Problems solved by technology
Method used
Image
Examples
preparation example Construction
[0066] Before coating the fluorocarbon coating solution on the surface of the substrate, the above preparation method further includes the step of configuring the raw material of the fluorocarbon layer into the fluorocarbon coating solution.
[0067] The fluorocarbon coating provided by the present invention carries out the following tests:
[0068] Adhesion of fluorocarbon layer: According to the standard of GB 1720-1979 "Determination of Paint Film Adhesion", test the adhesion of fluorocarbon layer to the substrate, of which 100 / 100 means no peeling, 90 / 100 means 10% off .
[0069] Encapsulation strength test: According to the standard of GB / T 31034-2014 "Insulating Backplane for Crystalline Silicon Solar Cell Modules", the bonding strength of the inner fluorocarbon layer and EVA is tested, using the 180° peel force test method.
[0070] QUV aging treatment: According to the standard of GB / T 31034-2014 "Insulation Backplane for Crystalline Silicon Solar Cell Modules", it is...
Embodiment 1
[0076] The preparation method of the fluorocarbon coating solution provided in this embodiment includes:
[0077] 70% polytetrafluoroethylene type fluorocarbon resin, 5% nano ceria UV absorber, particle size is 10~30nm, 3% matting powder, 0.5% polyacrylate additive, 12% thermoplastic polyurethane, 9.5% isocyanate. The host resin was dispersed in an organic solvent to form a fluorocarbon coating liquid with a solid content of 58%. Among them, the PTFE type fluorocarbon resin is provided by Daikin Fluorochemical, the nano ceria absorber is provided by BYK, the matting powder is provided by Grace Co., Ltd., the polyacrylate is provided by BYK, and the thermoplastic polyurethane is provided by He The isocyanate was provided by DaChem, the isocyanate was provided by Bayer, and the organic solvent was butyl acetate.
[0078] The coating was applied on transparent PET (275 μm thick) with a coating thickness of 16 μm.
[0079] The performance test results of the prepared fluorocarb...
Embodiment 2
[0081] The preparation method of the fluorocarbon coating solution provided in this embodiment includes:
[0082] 50% polytetrafluoroethylene type fluorocarbon resin, 10% nano ceria UV absorber, particle size is 10~30nm, 4% matting powder, 0.8% polyacrylate additive, 15.2% thermoplastic polyurethane, 20% isocyanate. The host resin was dispersed in an organic solvent to form a fluorocarbon coating liquid with a solid content of 50%. Among them, the PTFE type fluorocarbon resin is provided by Daikin Fluorochemical, the nano ceria absorber is provided by BYK, the matting powder is provided by Grace Co., Ltd., the polyacrylate is provided by BYK, and the thermoplastic polyurethane is provided by He The isocyanate was provided by DaChem, the isocyanate was provided by Bayer, and the organic solvent was butyl acetate.
[0083] The coating was applied on transparent PET (300 μm thick) with a coating thickness of 25 μm.
[0084] The performance test results of the prepared fluoroca...
PUM
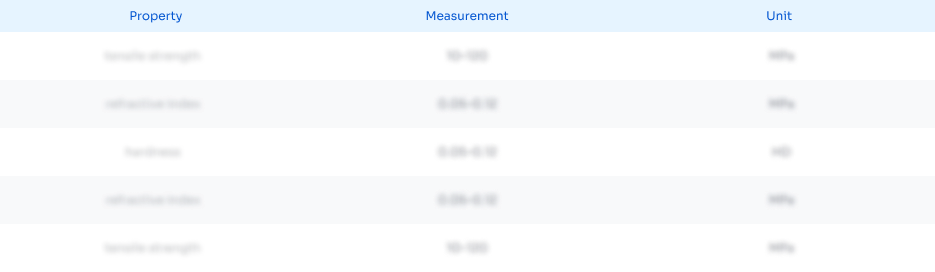
Abstract
Description
Claims
Application Information

- R&D
- Intellectual Property
- Life Sciences
- Materials
- Tech Scout
- Unparalleled Data Quality
- Higher Quality Content
- 60% Fewer Hallucinations
Browse by: Latest US Patents, China's latest patents, Technical Efficacy Thesaurus, Application Domain, Technology Topic, Popular Technical Reports.
© 2025 PatSnap. All rights reserved.Legal|Privacy policy|Modern Slavery Act Transparency Statement|Sitemap|About US| Contact US: help@patsnap.com