3D printing method for continuous fiber woven body reinforced fiber composite material
A 3D printing, continuous fiber technology, applied in additive processing, 3D object support structure, additive manufacturing, etc., can solve the problems of low fiber content, poor interlayer bonding performance, low structural strength, etc. The effect of enhancing the bonding force between layers and enhancing the strength
- Summary
- Abstract
- Description
- Claims
- Application Information
AI Technical Summary
Problems solved by technology
Method used
Image
Examples
Embodiment 1
[0059] (1) Carry out sizing treatment to the carbon fiber, then make the carbon fiber into a plain weave structure through a weaving process, and then use molten PLA resin to impregnate it to prepare a continuous fiber braid;
[0060] (2) According to the mass ratio: 50% of short carbon fibers, 45% of PLA resin fibers, 3% of silane coupling agent, and 2% of lubricants are mixed to make felts, and the felts are needled and rolled into strips. Heat strip felt at 230-250°C for 6-10 minutes, twist and extrude through extrusion equipment at a pressure of 6-10MPa, then cool and cut into short carbon fiber reinforced PLA resin substrates of appropriate width;
[0061] (3) Import 3D printing model;
[0062] (4) The short carbon fiber-reinforced PLA resin substrate obtained in step (2) is heated, melted and stirred, and sent to the No. 1 3D printing nozzle, and the continuous fiber braid in step (1) is heated and sent to the No. 2 3D printing nozzle. Nozzle;
[0063] (5) The printer ...
Embodiment 2
[0067] (1) Perform electrochemical treatment on the aramid fiber, then make the aramid fiber into a twill weave structure through a weaving process, and then impregnate it with molten PEEK resin to prepare a continuous fiber braid;
[0068] (2) According to the mass ratio: 55% of short aramid fiber, 40% of PEEK resin fiber, 3% of silane coupling agent, and 2% of dispersant are mixed to make a felt, and the felt is needled and rolled into strips Heat strip felt at 250-270°C for 8-10 minutes, twist and extrude through extrusion equipment at a pressure of 9-13MPa, and cut it into short aramid fiber-reinforced PEEK resin with appropriate width after cooling Substrate;
[0069] (3) Import 3D printing model;
[0070] (4) The short aramid fiber-reinforced PEEK resin base material obtained in step (2) is heated, melted and stirred and sent to No. 1 3D printing nozzle, and the continuous fiber braid obtained in step (1) is heated and sent to No. 2 nozzle. No. 3D printing nozzle;
[...
Embodiment 3
[0075] (1) The continuous fiber is electrochemically treated, and then the continuous fiber is made into a three-dimensional braided structure through a weaving process, and then it is impregnated with molten PP resin to prepare a continuous fiber braid; the continuous fiber is hemp Mixed fiber of fiber and basalt fiber;
[0076] (2) According to the mass ratio: 58% of the short mixed fiber (hemp fiber and basalt fiber mixed fiber), 37% of PP resin fiber, 3% of maleic anhydride, and 2% of thermal oxygen stabilizer are mixed to make felt. After needle-punching, the felt is gathered and rolled into strips, and the strip-shaped felt is heated at 230-240°C for 7-9 minutes, twisted and extruded at a pressure of 8-11MPa through the extrusion equipment, and then cooled. Short mixed fiber reinforced PP resin substrate cut into appropriate width;
[0077] (3) Import 3D printing model;
[0078] (4) The short mixed fiber reinforced thermoplastic resin substrate is heated, melted and st...
PUM
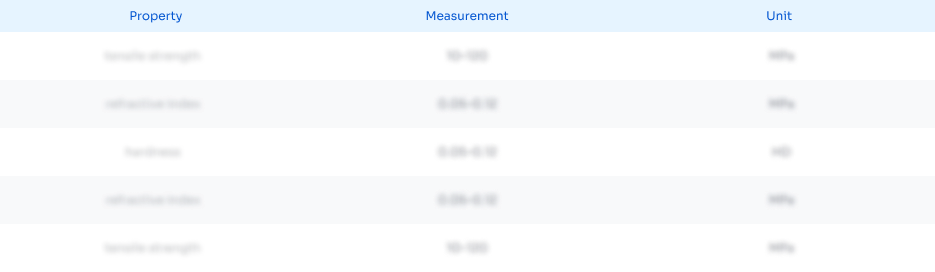
Abstract
Description
Claims
Application Information

- R&D
- Intellectual Property
- Life Sciences
- Materials
- Tech Scout
- Unparalleled Data Quality
- Higher Quality Content
- 60% Fewer Hallucinations
Browse by: Latest US Patents, China's latest patents, Technical Efficacy Thesaurus, Application Domain, Technology Topic, Popular Technical Reports.
© 2025 PatSnap. All rights reserved.Legal|Privacy policy|Modern Slavery Act Transparency Statement|Sitemap|About US| Contact US: help@patsnap.com