Zinc-nickel alloy electroplating process for metal surface
An electro-galvanized nickel and alloy process technology, applied in the field of electroplating nickel alloys, can solve the problems of large workpiece mass loss and poor cyclic corrosion resistance of the workpiece, and achieve the effects of less mass loss, improved cyclic corrosion resistance and improved performance.
- Summary
- Abstract
- Description
- Claims
- Application Information
AI Technical Summary
Problems solved by technology
Method used
Image
Examples
Embodiment 1
[0040] Electroplating zinc-nickel alloy process for metal surfaces, including the following steps:
[0041] Pretreatment step: soak the workpiece in the surface treatment solution, soak for 4 minutes under the condition of 40rmp, and then wash the pretreated workpiece with water flow at 60°C to prepare the pretreated workpiece. Each liter of surface treatment solution contains hydrogen Sodium oxide 75g, alkyl glucoside 5g and oleic acid triethanolamine salt 15g;
[0042] Activation step: place the pretreated workpiece in the activation solution of citric acid and octyl dimethyl amine oxide, the mass ratio of citric acid and octyl dimethyl amine oxide is 2:0.6, let it stand for 30s, and remove it to obtain the active chemical parts;
[0043] Electroplating step: place the activated workpiece in the electroplating solution at 32°C for electroplating, the electroplating solution includes sodium hydroxide 120g / L, zinc ion content 6g / L, nickel ion content 1.2g / L, electroplating ti...
Embodiment 2
[0047] Electroplating zinc-nickel alloy process for metal surfaces, including the following steps:
[0048] Pretreatment step: Soak the workpiece in the surface treatment solution for 12 minutes at 30rmp, and then wash the pretreated workpiece with water at 70°C to obtain a pretreated workpiece. Each liter of surface treatment solution contains hydrogen Sodium oxide 75g, alkyl glucoside 5g and oleic acid triethanolamine salt 15g;
[0049] Activation step: place the pretreated workpiece in the activation solution of citric acid and octyl dimethyl amine oxide, the mass ratio of citric acid and octyl dimethyl amine oxide is 5:0.6, let it stand for 90s, and remove it to obtain the active chemical parts;
[0050] Electroplating step: Place the activated workpiece in an electroplating solution at 22°C for electroplating. The electroplating solution includes sodium hydroxide 140g / L, zinc ion content 10g / L, nickel ion content 2.4g / L, electroplating time is 45min, remove The workpiec...
Embodiment 3
[0054] Electroplating zinc-nickel alloy process for metal surfaces, including the following steps:
[0055] Pretreatment step: immerse the workpiece in the surface treatment solution, soak for 10 minutes under the condition of 40rmp, and then wash the pretreated workpiece with water at 65°C to prepare the pretreated workpiece. Each liter of surface treatment solution contains hydrogen Sodium oxide 60g, alkyl glucoside 2g and oleic acid triethanolamine salt 8g;
[0056] Activation step: place the pretreated workpiece in the activation solution of citric acid and octyl dimethyl amine oxide, the mass ratio of citric acid and octyl dimethyl amine oxide is 5:0.6, let it stand for 70s, and remove it to obtain the active chemical parts;
[0057] Electroplating step: Place the activated workpiece in an electroplating solution at 22°C for electroplating. The electroplating solution includes sodium hydroxide 140g / L, zinc ion content 10g / L, nickel ion content 2.4g / L, electroplating time...
PUM
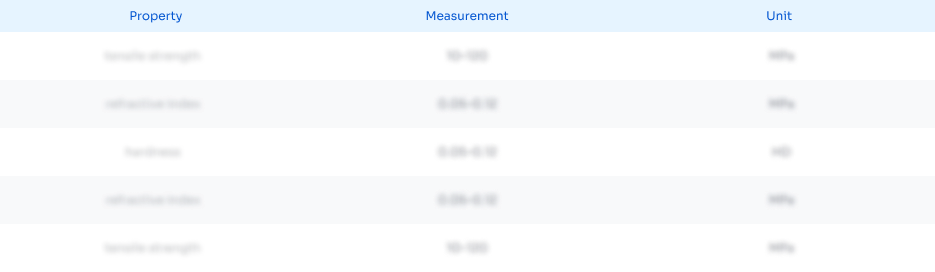
Abstract
Description
Claims
Application Information

- R&D
- Intellectual Property
- Life Sciences
- Materials
- Tech Scout
- Unparalleled Data Quality
- Higher Quality Content
- 60% Fewer Hallucinations
Browse by: Latest US Patents, China's latest patents, Technical Efficacy Thesaurus, Application Domain, Technology Topic, Popular Technical Reports.
© 2025 PatSnap. All rights reserved.Legal|Privacy policy|Modern Slavery Act Transparency Statement|Sitemap|About US| Contact US: help@patsnap.com