A Heat Treatment Process for Improving the Fatigue Life of gh4738 Alloy
A technology for fatigue life and nickel-based superalloys, which is applied in the field of heat treatment of high-temperature alloys, can solve problems such as alloy initiation cracks and lower alloy service performance, and achieve the effects of improving fatigue life, inhibiting growth, and improving alloy fatigue life
- Summary
- Abstract
- Description
- Claims
- Application Information
AI Technical Summary
Problems solved by technology
Method used
Image
Examples
Embodiment 1
[0028] The first step, raw material preparation:
[0029] The GH4738 nickel-based superalloy with the following components is selected according to the mass fraction: carbon 0.08%, chromium 19.61%, cobalt 13.55%, molybdenum 4.23%, titanium 2.98%, aluminum 1.47%, boron 0.007%, zirconium 0.11%, and the balance is nickel. Cut the alloy into Try on sticks, wash and dry until ready to use.
[0030] The second step, solution treatment:
[0031] The GH4738 alloy sample was heated to 1020°C for solution treatment at a heating rate of 25°C / min for 60 minutes, and then the alloy sample was cooled to 800°C by flowing air in the heat treatment furnace, and the cooling rate at this stage was 40°C / min; Remove and air cool to room temperature.
[0032] The third step, aging treatment:
[0033] The GH4738 alloy sample was heated to 770°C for 8 hours at a heating rate of 25°C / min, and then air-cooled to room temperature.
Embodiment 2
[0035] The first step, raw material preparation:
[0036] The GH4738 nickel-based superalloy with the following components is selected according to the mass fraction: carbon 0.08%, chromium 19.61%, cobalt 13.55%, molybdenum 4.23%, titanium 2.98%, aluminum 1.47%, boron 0.007%, zirconium 0.11%, and the balance is nickel. Cut the alloy into Try on sticks, wash and dry until ready to use.
[0037] The second step, solution treatment:
[0038] The GH4738 alloy sample was heated to 1025°C for solution treatment at a heating rate of 20°C / min for 70 minutes, and then the alloy sample was cooled to 800°C by flowing air in the heat treatment furnace, and the cooling rate at this stage was 45°C / min; Remove and air cool to room temperature.
[0039] The third step, aging treatment:
[0040] The GH4738 alloy sample was heated to 765°C for 9 hours at a heating rate of 20°C / min, and then air-cooled to room temperature.
Embodiment 3
[0042] The first step, raw material preparation:
[0043] The GH4738 nickel-based superalloy with the following components is selected according to the mass fraction: carbon 0.08%, chromium 19.61%, cobalt 13.55%, molybdenum 4.23%, titanium 2.98%, aluminum 1.47%, boron 0.007%, zirconium 0.11%, and the balance is nickel. Cut the alloy into Try on sticks, wash and dry until ready to use.
[0044] The second step, solution treatment:
[0045] The GH4738 alloy sample was heated to 1030°C for solution treatment at a heating rate of 25°C / min for 60 minutes, and then the alloy sample was cooled to 800°C by flowing air in the heat treatment furnace, and the cooling rate at this stage was 60°C / min; Remove and air cool to room temperature.
[0046] The third step, aging treatment:
[0047] The GH4738 alloy sample was heated to 760 °C for 10 h at a heating rate of 30 °C / min, and then air-cooled to room temperature.
PUM
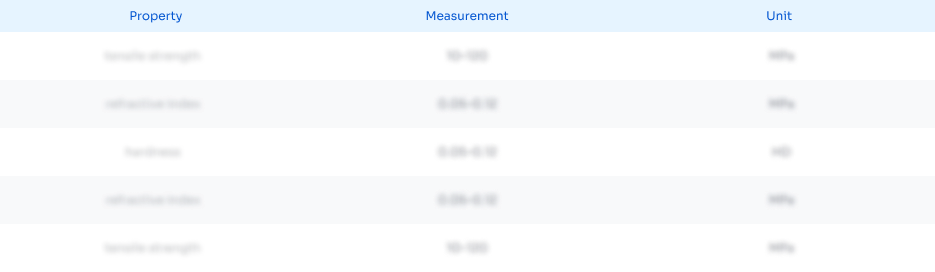
Abstract
Description
Claims
Application Information

- Generate Ideas
- Intellectual Property
- Life Sciences
- Materials
- Tech Scout
- Unparalleled Data Quality
- Higher Quality Content
- 60% Fewer Hallucinations
Browse by: Latest US Patents, China's latest patents, Technical Efficacy Thesaurus, Application Domain, Technology Topic, Popular Technical Reports.
© 2025 PatSnap. All rights reserved.Legal|Privacy policy|Modern Slavery Act Transparency Statement|Sitemap|About US| Contact US: help@patsnap.com