A composite material of reinforced thermoplastic polymer resin and its preparation method
A technology for enhancing thermoplasticity and composite materials, which is applied in the field of composite materials for reinforced thermoplastic polymer resins and its preparation, and can solve the problems of low processing fusion of polar mineral coal gangue powder, reduction of material mechanical properties and thermal stability, and thermoplasticity. Problems such as high viscosity of polymer processing, to achieve the effect of improving better compatibility, improving ecological environment protection, and improving compatibility
- Summary
- Abstract
- Description
- Claims
- Application Information
AI Technical Summary
Problems solved by technology
Method used
Image
Examples
Embodiment 1
[0034] Preparation of coal gangue powder: crush the coal gangue, use jet mill, grind to 1250 mesh, dry and set aside;
[0035] Coal gangue powder pretreatment: add 80 parts of modified coal gangue powder with a mass ratio of 1.0wt% 3-chloropropyltriethoxysilane coupling agent to the mixer, mix at a high speed of 150r / min for 10 minutes, and then add Mix the materials at a low speed of 60 r / min for 5 minutes, and put the mixed coal gangue powder on hold for 24 hours. Add the matured coal gangue powder and 40 parts of acrylonitrile-butadiene-styrene copolymer into the mixer, mix at a high speed of 150r / min for 5 minutes, and then put the mixture into the twin-screw extruder to melt. Extrusion and granulation make the toughening agent coat the coal gangue powder to form a coal gangue / toughening agent capsule structure. Extrusion granulator conditions are shown in Table 1:
[0036] Table 1 Extruder processing parameters
Embodiment 2
[0043]Coal gangue powder pretreatment: add 0.5wt% 3-chloropropyl triethoxysilane coupling agent to the mixer to modify 100 parts of coal gangue powder, mix at a high speed of 150r / min for 10 minutes, and then add Mix the materials at a low speed of 60 r / min for 5 minutes, and put the mixed coal gangue powder on hold for 24 hours. Add the matured coal gangue powder and 20 parts of acrylonitrile-butadiene-styrene copolymer into the mixer, mix at a high speed of 150r / min for 5 minutes, and then put the mixture into the twin-screw extruder to melt. Extrusion and granulation make the toughening agent coat the coal gangue powder to form a coal gangue / toughening agent capsule structure. Extrusion granulator conditions are shown in Table 1;
[0044] Mixing: Using a high-speed mixer, mix 100 parts of coal gangue particles, 100 parts of PVC resin powder, 5 parts of basalt fiber (8mm), 10 parts of high-viscosity methyl methacrylate with a viscosity of 10.8, 6 parts of calcium zinc stab...
Embodiment 3
[0047] Coal gangue powder pretreatment: add 2.5wt% 3-chloropropyl triethoxysilane coupling agent modified 60 parts of coal gangue powder into the mixer, mix at a high speed of 150r / min for 10 minutes, and then add Mix the materials at a low speed of 60 r / min for 5 minutes, and put the mixed coal gangue powder on hold for 24 hours. Add the matured coal gangue powder and 30 parts of acrylonitrile-butadiene-styrene copolymer into the mixer, mix at a high speed of 150r / min for 5 minutes, and then put the mixture into the twin-screw extruder to melt. Extrusion and granulation make the toughening agent coat the coal gangue powder to form a coal gangue / toughening agent capsule structure. Extrusion granulator conditions are shown in Table 1;
[0048] Mixing: Using a high-speed mixer, mix 100 parts of coal gangue particles, 100 parts of PVC resin powder, 5 parts of basalt fiber (10mm), 5 parts of high-viscosity methyl methacrylate with a viscosity of 10.2, 5 parts of high-viscosity me...
PUM
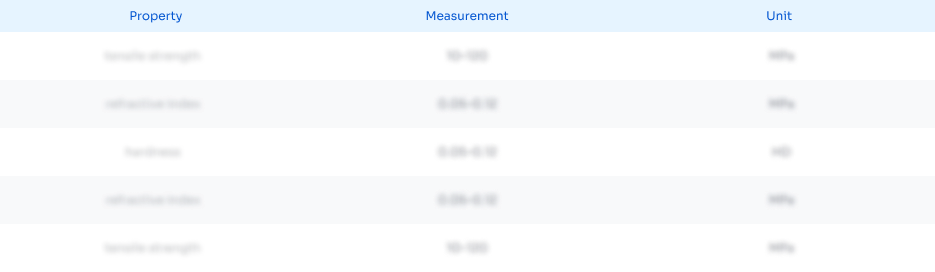
Abstract
Description
Claims
Application Information

- R&D
- Intellectual Property
- Life Sciences
- Materials
- Tech Scout
- Unparalleled Data Quality
- Higher Quality Content
- 60% Fewer Hallucinations
Browse by: Latest US Patents, China's latest patents, Technical Efficacy Thesaurus, Application Domain, Technology Topic, Popular Technical Reports.
© 2025 PatSnap. All rights reserved.Legal|Privacy policy|Modern Slavery Act Transparency Statement|Sitemap|About US| Contact US: help@patsnap.com