Multilayered-structure flexible film with high thermal conductivity and three-level shape memory characteristic and preparation method of multilayered-structure flexible film
A multi-layer structure, flexible film technology, applied in chemical instruments and methods, lamination, layered products, etc., can solve problems such as reducing the thermal conductivity of composites, achieve easy industrialization, reduce interface thermal resistance, and process compactness Effect
- Summary
- Abstract
- Description
- Claims
- Application Information
AI Technical Summary
Problems solved by technology
Method used
Image
Examples
preparation example Construction
[0046] The preparation method of the multilayer structure flexible film with high thermal conductivity and tertiary shape memory comprises the following steps:
[0047] (1) Add sodium alginate to the dispersant, stir overnight, and prepare a sodium alginate dispersion with a concentration of 1-3 mg / mL;
[0048] (2) Graphene oxide is added to the dispersant, stirred for 2 hours, ultrasonicated for 30 minutes, and a graphene oxide dispersion with a concentration of 1-3 mg / mL is prepared;
[0049](3) The thermoplastic polymer material is added to the dispersant, stirred for 0.5-1 hour, ultrasonicated for 5-10 minutes, and a thermoplastic polymer material dispersion with a concentration of 1-3 mg / mL is prepared;
[0050] (4) The sodium alginate dispersion in step (1) is mixed with the graphene oxide dispersion in step (2) and the thermoplastic polymer material dispersion obtained in step (3) according to the set weight ratio, and stirred for 0.5- 1h, ultrasonication for 10min, to...
Embodiment 1
[0058] The multi-layer structure flexible film with high thermal conductivity and three-stage shape memory and its preparation method provided by this implementation are specifically a five-layer structure graphene oxide-polymer material composite film, which is composed of graphene oxide, sodium alginate , polyethylene glycol and paraffin, the mass percentage of graphene oxide in the composite film is 20%, the mass percentage of sodium alginate is 40%, the mass percentage of polyethylene glycol is 20%, and the mass percentage of paraffin is 20%.
[0059] During the preparation process of the composite membrane, a membrane needs to be formed on a pre-synthesized polyacrylamide hydrogel, including a single-layer thin film and a multi-layer thin film.
[0060] Aforesaid polyacrylamide hydrogel, its synthetic steps are as follows:
[0061] (1) Add acrylamide, methylene acrylamide, ammonium persulfate, and distilled water to 100ml of distilled water at a mass ratio of 15:0.3:0.3 ...
Embodiment 2
[0076] The multilayer structure flexible film with high thermal conductivity and tertiary shape memory and the preparation method thereof provided in this implementation are specifically a 10-layer graphene oxide-polymer material composite film, which is basically the same as in Example 1, The difference is that:
[0077] The composite film is made of graphene oxide, sodium alginate, polycaprolactone and paraffin, the mass percent of graphene oxide in the composite film is 40%, the mass percent of sodium alginate is 30%, the polycaprolactone The mass percentage is 15%, and the mass percentage of paraffin wax is 15%. Composite membranes need to be formed on pre-synthesized polyacrylamide hydrogels.
[0078] Aforesaid polyacrylamide hydrogel, its synthetic steps are as follows:
[0079] (1) Add acrylamide, methylene acrylamide, ammonium persulfate, and distilled water to 100ml of distilled water at a mass ratio of 15:0.3:0.3 to obtain a dispersion;
[0080] (2) Add 300 μL of ...
PUM
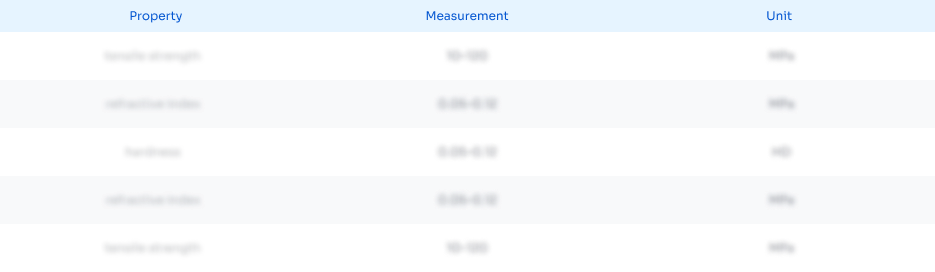
Abstract
Description
Claims
Application Information

- R&D
- Intellectual Property
- Life Sciences
- Materials
- Tech Scout
- Unparalleled Data Quality
- Higher Quality Content
- 60% Fewer Hallucinations
Browse by: Latest US Patents, China's latest patents, Technical Efficacy Thesaurus, Application Domain, Technology Topic, Popular Technical Reports.
© 2025 PatSnap. All rights reserved.Legal|Privacy policy|Modern Slavery Act Transparency Statement|Sitemap|About US| Contact US: help@patsnap.com